МИНИСТЕРСТВО ТРАНСПОРТНОГО СТРОИТЕЛЬСТВА СССР
КРЕПЛЕНИЕ ВЫРАБОТОК
НАБРЫЗГ-БЕТОНОМ И АНКЕРАМИ ПРИ СТРОИТЕЛЬСТВЕ ТРАНСПОРТНЫХ ТОННЕЛЕЙ И МЕТРОПОЛИТЕНОВ
НОРМЫ ПРОЕКТИРОВАНИЯ И ПРОИЗВОДСТВА РАБОТ
ВСН 126-90
Минтрансстрой СССР
Разработаны ВНИИ транспортного строительства Минтрансстроя СССР, Главным координационно-технологическим управлением строительства, ЛИИЖТом, МПС СССР. Руководитель темы д-р техн. наук В. Е. Меркин; ответственные исполнители: канд. техн. наук В. М. Смолянский, инж. И. В. Гиренко, канд. техн. наук Н. С. Четыркин, д-ра техн. наук Д. Т. Голицинский, А. Е. Шейкин.
Внесены ВНИИ транспортного строительства Минтрансстроя СССР.
Подготовлены к утверждению Главтехнормированием Госстроя СССР Ю. А. Кузьмичем.
С введением в действие ВСН 126-90 “Крепление выработок набрызгбетоном и анкерами при строительстве транспортных тоннелей и метрополитенов. Нормы проектирования и производства работ” утрачивают силу ВСН 126-78 “Инструкция по применению анкеров и набрызг-бетона в качестве временной крепи выработок транспортных тоннелей”.
Согласовано с Госстроем СССР 25 июня 1990 г. № 7-524.
ПРЕДИСЛОВИЕ
Настоящие Нормы разработаны в дополнение к главам СНиП по проектированию (СНиП II-44—78 “Тоннели железнодорожные и автодорожные” и СНиП II-40—80 “Метрополитены”) и строительству тоннелей и метрополитенов (СНиП III-44—77 “Тоннели железнодорожные, автодорожные и гидротехнические. Метрополитены”) на основе обобщения передового отечественного и зарубежного опыта применения анкеров и набрызгбетона для крепления подземных выработок.
Нормы содержат: необходимые указания для выбора вида временных и постоянных конструкций крепи из набрызгбетона и анкеров, а также комбинированных конструкций; расчетные положения для определения их параметров; требования к материалам конструкций, технологии и организации работ по их возведению, включая методики контроля качества и оценки состояния закрепленных выработок.
Нормы включают переработанные материалы действующих ведомственных строительных норм (ВСН 126(78) а также результаты исследований, проведенных за последние десять лет ЦНИИСом, СибЦНИИСом, СКТБ Главтоннельметростроя, МИИТом, ЛИИЖТом и другими организациями.
Нормы разработаны д-ром техн. наук В. Е. Меркиным инж. И. В. Гиренко, кандидатами техн. наук В. М Смолянским, Д. И. Колиным, В. М. Кононовым, инженерами А. В. Бурнштейном, Л. А. Воробьёвым, Э. Г. Кобиашвили (ЦНИИС), канд. техн. наук Г. Ф. Петровым (СибЦНИИС), инж. В. В. Филатовым, кандидатами техн. наук Б. А. Виттенбергом, Н. С. Четыркиным (СКТБ Главтоннельметростроя), докторами техн. наук Д. М. Голицинским (ЛИИЖТ) A. Е. Шейкиным, канд. техн. наук Л. М. Добшицем (МИИТ)
Зам. директора института Г. Д. ХАСХАЧИХ
|
Ведомственные строительные нормы |
ВСН-126—90 |
Министерство транспортного строительства СССР |
Крепление выработок набрызгбетоном и анкерами при строительстве транспортных тоннелей и метрополитенов. Нормы проектирования и производства работ |
Взамен ВСН 126—78 |
1. ОБЩИЕ ПОЛОЖЕНИЯ
1.1. Требования настоящих Норм должны соблюдаться при проектировании и возведении конструкций крепления из набрызгбетона, анкеров, арок или их комбинаций в выработках метрополитена, железнодорожных и автодорожных тоннелей.
Нормы предназначены для организаций Министерства транспортного строительства СССР, осуществляющих проектирование и строительство тоннелей, а также других министерств и ведомств, проводящих приемку этих сооружений.
1.2. Нормы разработаны в соответствии с требованиями СНиП II-40—80; СНиП III-44—77; СНиП 2.05.05 и “Правил безопасности и производственной санитарии при строительстве метрополитенов и тоннелей” и других действующих нормативных документов, а также в соответствии с аналогичными требованиями для расчета, установленными главами СНиП по проектированию тоннелей и метрополитенов.
1.3. Работы по возведению рассматриваемых в настоящих Нормах крепей должны выполняться в соответствии с проектами организации строительства и проектами производства работ, разработанными и утвержденными в установленном порядке.
1.4. При выборе способа проходки предпочтение следует отдавать комбайновому способу, как обеспечивающему минимальную шероховатость контура выработки и минимальное нарушение массива.
1.5. При буровзрывном способе ведения работ применение анкеров и набрызгбетона следует сочетать с контурным (гладким) взрыванием, обеспечивающим повышение точности обработки поверхности и устойчивости выработки.
1.6. При возведении крепей с применением анкеров и набрызгбетона следует стремиться к максимальной механизации и автоматизации крепежных процессов и операций уделяя особое внимание технологической надежности применяемых проходческих комплексов.
Внесены Всесоюзным научно-исследовательским институтом транспортного строительства (ЦНИИСом) |
Утверждены указанием Минтрансстроя СССР от 18.07.90 № Св-519 |
Срок введения в действие 1 января 1991 г. |
1.7. Возведение крепи должно выполняться только на основании паспорта крепления подземной выработки, составляемого в соответствии с требованиями настоящих Норм на основании рабочих чертежей и результатов предварительных испытаний.
Паспорт крепления утверждается главным инженером строительной организации. Технический персонал строительной организации обязан вести систематический контроль за соблюдением паспорта крепления, состоянием выработок, закрепленных анкерами, арками, набрызгбетоном и их комбинациями. При изменении инженерно-геологических условий паспорт крепления подлежит корректировке.
1.8. При использовании анкеров, арок и набрызгбетона в постоянных конструкциях в технической документации должны быть указаны меры по обеспечению их долговечности: омоноличивание металлических стержней анкеров и арок; снижение концентрации химических добавок до норм установленных для постоянных конструкций по условиям предотвращения коррозии; применение металлических сеток или дисперсной арматуры.
2. ОБЛАСТЬ ПРИМЕНЕНИЯ АНКЕРОВ И НАБРЫЗГБЕТОНА. ВЫБОР ВИДА И КОНСТРУКЦИИ КРЕПИ
2.1. Анкерную и набрызгбетонную крепи, а также их комбинации в виде анкер-набрызгбетонной, арочно-набрызгбетонной и анкер-набрызгбетон-арочной крепей разрешается применять в горизонтальных и наклонных тоннельных выработках всех видов, проходимых в сухих и слабообводненных массивах (грунтах влажных, капежах) не ниже средней устойчивости (расчетное допустимое время технологического использования незакрепленного обнажения пород до 10 сут), сложенных породами с сопротивлением одноосному сжатию “в массиве” (по СНиП 2.05.05) не менее 30 МПа.
2.2. Применение анкеров и набрызгбетона для крепления выработок в слабоустойчивых массивах (расчетное допустимое время технологического использования неподкрепленного обнажения пород не менее 1 сут) самостоятельно или в сочетании с арками (комбинированная анкер-набрызгбетон-арочная крепь, обязательно с металлической сеткой) разрешается только при наличии инженерного обоснования—подтверждение опытными работами в условиях строительства или на других объектах в аналогичных условиях с учетом применяемой технологии, имеющегося оборудования и квалификации проходчиков.
Применение анкеров и набрызгбетона как самостоятельной крепи или как составной части арочной (рамной) системы крепления (межрамная затяжка) в неустойчивых массивах (расчетное время неподкрепленного обнажения менее 1 сут) и зонах тектонических нарушений разрешается только при получении положительных результатов опытной проверки в условиях строительства.
2.3. Во всех случаях применения набрызгбетонной крепи должно обеспечиваться сцепление набрызгбетона с грунтом не менее сопротивления самого грунта на растяжение “в куске” для слабых и сильнотрещиноватых пород и не менее 0,5 МПа для крепких скальных.
2.4. Выбор крепи предпочтительнее осуществлять в два этапа—сначала ориентировочно выбирают вид крепи (варианты), который может быть технологически осуществлен в данных условиях строительства, а затем уточняют конструкцию и параметры крепи по совокупности инженерно-геологических и технологических факторов.
2.5. В общем случае проектирование крепи с применением анкеров и набрызгбетона должно включать выбор (назначение) следующих параметров: длины анкеров, шага крепления, диаметра штанг, количества слоев набрызгбетона, его класса.
Для предварительного (ориентировочного) выбора типа крепи в зависимости от инженерно-геологических условий и размеров выработки можно пользоваться данными приложения 1.
При возведении набрызгбетонной крепи (обделки) в выработках, проходимых буровзрывным способом, следует обеспечивать допустимую шероховатость поверхности породного обнажения. Критериями допустимой шероховатости являются отношение У суммарной длины отпечатков (следов) шпуров к суммарной длине всех контурных шпуров и высота hk неровностей (выступов впадин) между отпечатками шпуров:
Y = 4,83 Т + 0,52 f + 30,29 %;
hk ( 1,08 T + 0,06 f + 13,23 см,
где Т—категория трещиноватости скального массива по классификации Межведомственной комиссии по взрывному делу; f—коэффициент крепости по М. М. Протодьяконову (приложение 2).
Необходимое качество поверхности контура тоннеля можно обеспечить путем применения контурного взрывания. Методика расчета параметров контурного взрывания, критерии состояния поверхности контура и методы устранения сверхнормативной шероховатости поверхности при набрызгбетонировании приведены в приложении 3.
2.7. Окончательные параметры конструкции крепи тоннеля (толщину набрызгбетонного покрытия, длину анкеров и т. д.) следует устанавливать расчетом согласно требованиям глав 3 и 4 настоящих Норм.
2.8. Выбор оптимального варианта конструкций комбинированной крепи рекомендуется производить на основе технико-экономического сравнения в соответствии с указаниями п. 2.5.
2.9. При применении анкеров и набрызгбетона в вечномерзлых грунтах должны быть обеспечены:
надежное закрепление анкеров и сцепление набрызгбетонного покрытия с породой при температуре породного массива;
достаточная несущая способность крепи и сохранение ее работоспособности при возможном оттаивании мерзлоты.
Указанным требованиям отвечают, прежде всего клинощелевые и распорные анкеры, закрепляемые в массиве (в случае перехода приконтурного слоя пород в неустойчивое состояние при оттаивании) за пределами зоны оттаивания пород.
Применение железобетонных анкеров, анкеров на пласторастворах и набрызгбетона допускается при создании условий для нормального твердения омоноличивающих растворов и бетона покрытий путем введения противоморозных добавок, искусственного подогрева и т. д.
3. НАБРЫЗГБЕТОННАЯ КРЕПЬ
Материалы, подбор состава смеси и технология крепления набрызгбетоном
3.1. Конструкции крепи из набрызгбетона могут выполняться в зависимости от условий применения в виде неармированного или армированного металлической сеткой фибрами покрытия как самостоятельной конструкции так и в сочетании с анкерами или арками.
3.2. Для устройства набрызгбетонного покрытия должны применяться конструкционные бетоны, соответствующие ГОСТ 25192—82, в том числе тяжелый и легкий плотной структуры следующих классов и марок, определяемых в 28-суточном возрасте:
1. Классы бетона по прочности на сжатие:
тяжелый ...................В25; В30; В35; В40; В45
мелкозернистый............. В25; В30; В35
легкий бетон при марках по
средней плотности Д1600—
Д2000..................... В25; В30; В35; В40
2. Классы бетона по прочности на Вt = 1,6; Вt = 2; Вt = 2,4;
осевое растяжение........... Вt = 2,8; Вt = 3,2
3. Марки по морозостойкости..... F100; F150; F'200; F300
4. Марки по водонепроницаемости . W4; W6; W8
3.3. Для приготовления набрызгбетонных смесей следует применять цементы, заполнители и добавки по стандартам и техническим условиям на материалы конкретных видов в соответствии с ГОСТ 26633—85.
3.4. В зависимости от требуемого класса набрызгбетона по прочности на сжатие марку цемента следует назначать по табл.1.
Таблица 1
Класс набрызгбетона |
Марка цемента |
|
рекомендуемая |
допускаемая |
В25 |
400 |
500 |
В30 |
500 |
400, 600 |
В35 |
500 |
400, 600 |
В40 |
550 |
600 |
В45 |
600 |
550 |
3.5. В качестве вяжущего необходимо применять портландцемент, в том числе бездобавочный и с минеральными добавками по ГОСТ 10178—85 и ГОСТ 23464—85.
3.6. При агрессивных воздействиях на набрызгбетонные конструкции при напоре воды до 0,1 МПа в процессе эксплуатации цемент, мелкий и крупный заполнители выбирают в соответствии со СНиП 2.03.11—85 “Защита строительных конструкций от коррозии”.
3.7. Для быстрого закрепления выработки (особенно при обводнении ее поверхности), а также для создания набрызгбетонного покрытия толщиной 20—30 см при использовании обычного (не специального) цемента в состав смеси должны быть введены добавки—ускорители схватывания и твердения.
3.8. Вид вяжущего и химических добавок для технологической крепи выбирают в зависимости от требований, предъявляемых к набрызгбетону, определяемых характеристикой грунтов, их устойчивостью, обводненностью, температурой и наличием агрессивных сред (приложения 4, 5, 6).
3.9. Для получения проектных марок набрызгбетона по морозостойкости и водонепроницаемости рекомендуется применять цементы с содержанием С3А ( 7% и С3А + С4АF ( 20%.
3.10. Каждая новая партия цемента, поступающая на строительство и используемая для набрызгбетона, должна испытываться на активность, нормальную густоту и сроки схватывания в соответствии с требованиями ГОСТ 310.1—76*, ГОСТ 310.4—81*, ГОСТ 310.2—76*, ГОСТ 310.3—76*, ГОСТ 310.5—88, ГОСТ 310.6—85.
3.11. Для обеспечения класса набрызгбетона на осевое растяжение Bt 1,6 и выше рекомендуется вводить в смесь фибры—стальные волокна длиной до 32 м и диаметром до 0,5 мм в количестве до 6% от массы смеси.
3.12. В качестве мелкого заполнителя для набрызгбетона следует использовать плотный песок, удовлетворяющий ГОСТ 8736—85 и имеющий следующие характеристики:
модуль крупности—не менее 2 (использование песка с модулем крупности менее 2 допускается при специальном экспериментальном обосновании);
относительная влажность—до 7%;
предельное содержание глинистых частиц—до 0,5%;
содержание зерен фракции меньше 0,14 мм—до 10%;
предельное содержание фракций крупнее 10 мм—не более 5%.
Допускается применение пористого песка, отвечающего требованиям ГОСТ 9759—83.
3.13. В качестве крупного заполнителя для набрызгбетона следует применять щебень или щебень из гравия, удовлетворяющий ГОСТ 8267—82, ГОСТ 8269—87, ГОСТ 9757—83 ГОСТ 10260—82.
3.14. Максимальный размер крупных частиц заполнителей следует назначать с учетом технических характеристик применяемых набрызгбетонмашин и толщины набрызгбетонного покрытия, но не более 25 мм, причем в покрытиях толщиной до 5 см максимальный размер зерен крупного заполнителя не должен превышать 10 мм, а в покрытиях толщиной от 5 до 10 см—не более 15 мм. Совмещенные кривые гранулометрического состава заполнителей для этих случаев должны укладываться в зону графиков на рис. 1.
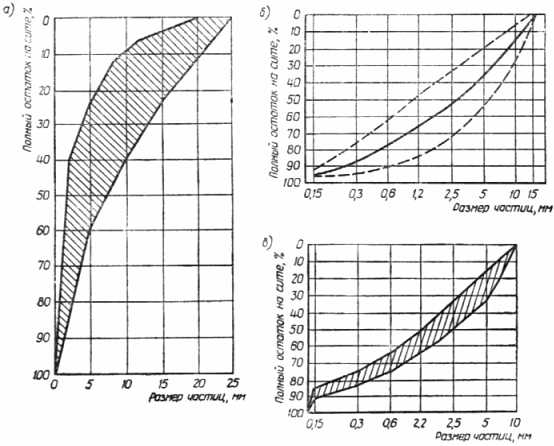
Рис. 1. Гранулометрический состав заполнителей с максимальными размерами зерен 25 мм (а), 15 мм (б) и 20 мм (в):
——— средние значения; — — — предельные значения
3.15. Вода для затворения набрызгбетонной смеси должна соответствовать требованиям ГОСТ 23732—79.
Вода для затворения сухой смеси в условиях температур ниже плюс 5°С должна иметь (на момент подачи ее к соплу) температуру 40—70°С. Влажность смеси заполнителей должна быть не менее 2%. При использовании смеси заполнителей с влажностью до 2% с целью снижения концентрации пыли при набрызгбетонировании следует использовать две камеры смешения, одна из которых отнесена от сопла на расстояние 4—5 м.
3.16. Состав набрызгбетона надлежит подбирать, дозируя компоненты по массе, в соответствии с рекомендуемой методикой (приложение 7).
3.17. Водоцементное отношение набрызгбетона следует принимать в пределах от 0,4 до 0,5 (с учетом влажности заполнителей) .
При определении необходимого количества воды следует учитывать, что оптимальная жесткость набрызгбетонной смеси составляет от 20 до 60 с по ГОСТ 10181—76.
3.18. При нанесении набрызгбетона на слабые или склонные к размоканию породы, а также при низких температурах окружающей среды количество воды следует уменьшать до В/Ц=0,35—0,40. Равномерное смачивание сухой смеси при этом достигается путем подачи в сопло или в камеру смешения распыленной паровоздушной смеси.
3.19. Расчетный (теоретический) состав набрызгбетона необходимо корректировать по величине отскока путем проведения контрольных нанесений материала согласно методике, приведенной в приложении 8.
Рекомендуется величину отскока принимать не более 20% от массы сухой смеси при нанесении на стены выработки и 30%—при нанесении на свод. В случае получения отскока больше приведенных величин состав набрызгбетона следует изменять в сторону уменьшения размера крупного заполнителя.
Наиболее экономичным составом набрызгбетона будет такой, когда при наименьших расходе цемента и величине отскока достигается проектная прочность. Правильно нанесенное покрытие из набрызгбетона с рекомендуемым водоцементным отношением имеет жирный блеск без сухих пятен и оплываний. При нанесении смеси отсутствует напыление.
Расчет набрызгбетонных конструкций
3.20. Классы и марки набрызгбетона по прочности, морозостойкости и водонепроницаемости должны назначаться как для конструкций из монолитного бетона, укладываемого с применением опалубки, в соответствии с требованиями СНиП II-40—80; СНиП 2.05.05; СНиП 2.03.01—84; СНиП 2.06.08—87.
3.21. При расчете крепи нормативные и расчетные характеристики набрызгбетона (прочность, модуль упругости) при отсутствии опытных данных в условиях строительства назначают в зависимости от класса бетона по прочности по таблицам СНиП 2.03.01—84 (приложение 9, табл. 1—3).
При определении прочности набрызгбетона по образцам следует руководствоваться ГОСТ 18105—86, при определении морозостойкости—ГОСТ 10060—86, водонепроницаемости— ГОСТ 12730.5—84.
3.22. Возраст набрызгбетона, отвечающий его классу по прочности на сжатие и осевое растяжение, следует назначать при проектировании, исходя из возможных реальных сроков загружения конструкции проектными нагрузками, способа возведения и условий твердения бетона. При отсутствии этих данных класс набрызгбетона может устанавливаться в возрасте 28 суток по табл. 2.
Таблица 2
Классы набрызгбетона по прочности
на сжатие |
В25 |
В30 |
В35 |
В40 |
В 50 |
Средняя прочность на сжатие бетонов, МПа, при коэффициенте вариации 0,135 |
32,7 |
39,2 |
45,7 |
52,4 |
65,4 |
3.23. Марку набрызгбетона по водонепроницаемости W следует назначать не менее: W4—при градиенте гидростатического напора (отношение максимального напора воды в метрах к толщине обделки в метрах) от 5 до 10; W6—от 10 до 20; W8—от 20 до 30.
3.24. Марку набрызгбетона по морозостойкости F надлежит назначать в зависимости от расчетной зимней температуры наружного воздуха в соответствии с п. 1.8 СНиП 2.03.01—84, F 300—для температуры ниже минус 40°С; F 200— от минус 40 до минус 20°С; F 150—от 20°С и выше.
3.25. Толщина набрызгбетона, применяемого в качестве защитного покрытия против выветривания породного обнажения, принимаемая без расчета, должна быть не менее 3 см.
Толщина набрызгбетона в качестве защитного слоя для рабочей арматуры должна быть не менее 2 см.
Толщину набрызгбетона, применяемого в качестве расчетной несущей конструкции самостоятельно или в сочетании с анкерами или арками, следует назначать не менее 5 см.
Расчет набрызгбетонного покрытия как несущей конструкции
3.26. Нагрузки на набрызгбетонную крепь принимают по результатам натурных исследований в условиях строительства.
До проведения указанных исследований нагрузки на набрызгбетонную крепь могут быть оценены расчетным путем в соответствии с действующими нормами проектирования тоннельных сооружений.
3.27. Толщину набрызгбетонного покрытия, используемого в качестве несущей конструкции, определяют следующим образом.
Если по условиям технологии проходки выработки возможно обеспечение гладкого контура (механизированная проходка), то набрызгбетонное покрытие следует проектировать как распорную конструкцию, работающую совместно с прилегающим грунтом, в которой предельное состояние покрытия обуславливается работой на сжатие. В этом случае для определения толщины покрытия следует руководствоваться положениями п. 3.28.
Если по условиям технологии проходки нельзя гарантировать создание гладкого контура выработки и, следовательно, работу покрытия как распорной конструкции, то покрытие из набрызгбетона следует рассчитывать как жесткую пластину, работающую в упругопластическом режиме от нагрузки в виде локального вывала. В этом случае для определения толщины набрызгбетонного слоя следует руководствоваться положениями п. 3.30.
3.28. Для предварительной (ориентировочной) оценки несущей способности набрызгбетонного покрытия как распорной подземной конструкции, работающей преимущественно на сжатие, следует использовать проверку условия:

где Vн—минимальное радиальное смещение контура выработки, м (рекомендуется пользоваться программой типа FOK-4 и FAK-1, приложение 10); Rв—расчетное сопротивление набрызгбетонного покрытия на сжатие по первой группе предельных состояний, МПа (см. приложение 9); R(радиус свода выработки, м; Ен—модуль упругости набрызгбетона (начальный) на сжатие, МПа (см. приложение 9).
Если указанное условие выполняется, то полагают что прочность набрызгбетонного покрытия будет обеспечена. В противном случае рекомендуется применение анкер-набрызгбетонной крепи.
Если прочность грунта недостаточна для обеспечения устойчивости выработки, то при ровном контуре толщину набрызгбетона следует назначать, исходя из расчета набрызг-бетонного покрытия как монолитной обделки. При этом, учитывая, что технология возведения набрызгбетонной обделки по сравнению с опалубочным бетонированием позволяет существенно снизить разуплотнение массива, особенно в сводовой части выработки, и тем самым способствует большей стабилизации напряженно-деформированного состояния массива, допускается принимать расчетную нагрузку на крепь в этом случае на 30% меньше по сравнению с нагрузкой на монолитную обделку для этих же условий. Учет влияния неровностей фактического контура выработки на несущую способность такой крепи следует проводить в соответствии с п. 3.29.
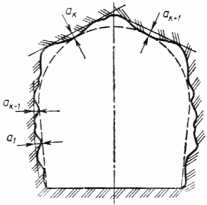
Рис. 2. Определение параметров неровностей контура выработки при расчете
набрызгбетонной крепи:
— — — проектное очертание выработки
3.29. Отклонение реального контура поверхности выработки от гладкого может явиться причиной появления в вершинах неровностей нежелательных растягивающих напряжений. В этом случае необходимо обеспечить корректировку толщины набрызгбетонного покрытия hн из условия недопущения растягивающих напряжений в вершинах неровностей.
Характеристиками неровностей являются их среднее число на контуре Кк и их средняя амплитуда
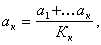
где аi при i=1, ... Кк определяется как расстояние от наиболее выступающей точки реального контура до хорды, стягивающей два соседних наиболее глубоких участка впадин (рис. 2). При этом в расчетах рекомендуется учитывать неровности с амплитудой аi ( 10 см, число которых находится, как правило, в пределах от 8 до 20.
При отсутствии фактических данных среднее число неровностей на контуре Кк рекомендуется определять расчетным путем как половину отношения длины контура к расстоянию между контурными шпурами.
В этом же случае среднюю амплитуду неровностей рекомендуется принимать равной допустимой норме перебора.
Расстояние между шпурами в метрах при опытных взрывах в зависимости от крепости и трещиноватости грунта ориентировочно следует определять по табл. 3, а допустимую норму перебора в сантиметрах—по табл. 4.
Таблица 3
| | | |
Коэффициент |
Степень трещиноватости пород |
крепости пород |
нетрещиноватые |
слаботрещиноватые |
трещиноватые
и сильнотрещиноватые |
4(6 |
0,6 |
0,7 |
0,8 |
6—8 |
0,5 |
0,6 |
0,7 |
8—10 |
0,4 |
0,5 |
0,6 |
10—12 |
0,3 |
0,4 |
0,5 |
Таблица 4
Выработка |
Величина перебора, см |
|
1 ( f ( 4 |
4 ( f ( 12 |
Тоннели |
10 |
15 |
Штольни |
8 |
8 |
Результатом опытных взрывов должно явиться определение окончательного расстояния между контурными шпурами и других режимов взрывания, которые обеспечивают достижение заданных критериев состояния поверхности контура тоннелей.
При наличии статистических данных по отклонениям контура тоннеля от проектного при проходке в аналогичных условиях толщину набрызгбетонного покрытия рекомендуется корректировать из условия отсутствия растягивающих напряжений в вершинах неровностей
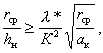
где —приведенный радиус выработки, м; Sв—площадь поперечного сечения выработки, м2; (*—коэффициент, характеризующий соотношение жесткостей породы и набрызгбетона, определяемый по табл. 5.
Таблица 5
Породы |
Средний радиус выработки rср, м |
|
3 |
6 |
9 |
12 |
Туфы |
2,4 |
4,8 |
7,2 |
9,6 |
Глинистые сланцы |
4,8 |
9,6 |
14,4 |
19,2 |
Известняки плотные |
7,8 |
14,4 |
21,6 |
28,8 |
Песчаники |
10,8 |
21,6 |
32,4 |
43,2 |
Граниты, диориты |
84 |
118 |
252 |
336 |
Гнейсы |
51 |
102 |
153 |
204 |
Если данное условие не выполняется, необходимо уменьшить межанкерное (межарочное) расстояние а, исходя из необходимой толщины слоя набрызгбетона hн.
3.30. Ориентировочно, с последующей корректировкой по результатам наблюдений, толщину набрызгбетонного покрытия при неровном контуре выработки (не выполняются требования п. 3.28) рекомендуется определять по формуле, м:
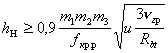
0,03 < hH < 0,20 м, fкр.р ( 2,
где m1, т2, т3 — коэффициенты условий работы, учитывающие соответственно общую конструкцию крепи (обделки); качество сцепления покрытия с грунтом; армирование покрытия; т1=1—при анкер-набрызгбетонной крепи; 1,15—при арочно-набрызгбетонной крепи или арочно-анкер-набрызгбетонной крепи; 3,3/fкр.р—в инженерно-геологических условиях, когда допустимо применение в качестве крепи одного набрызгбетона (обеспечивается эффективное использование несущей способности пород); m2=1—когда гарантируется хорошее сцепление покрытия с грунтом; 1,5—когда имеется опасность нарушения сцепления покрытия с грунтом например при обводненной поверхности выработки; т3=1—покрытие без учета армирования или без армирования; 0,8—с учетом армирования покрытия сеткой, стержнями, устанавливаемыми конструктивно; и—характерный размер возможного вывала, м; (гр—объемный вес грунта вывала, МН/м3 (при отсутствии фактических данных рекомендуется принимать (гр=0,0245 МН/м3=2,5 тс/м3); Rbt—расчетное сопротивление набрызгбетона на осевое растяжение по первой группе предельных состояний, МПа (см. приложение 9, табл. 1); fкр.р( расчетное значение коэффициента крепости грунта “в массиве” (приложение 11);
Значение и принимают в зависимости от следующих условий:
в случае анкер-набрызгбетонной крепи и принимают равным наибольшему расстоянию между анкерами;
в случае арочно-набрызгбетонной крепи и принимают равным шагу арок;
в случае комбинации анкеров, арок и набрызгбетона и принимают либо по межанкерному расстоянию, либо по шагу арок в зависимости от того, какой из этих элементов конструкции крепи принят за определяющий (основной);
в случае применения набрызгбетона как самостоятельной крепи, покрытие рассчитывают на вывал в своде, принимая u=B/4, где B—пролет выработки “вчерне”, м.
По конструктивно-технологическим соображениям в общем случае принимают толщину hH покрытия одинаковым в своде и в стенах. Допускается принимать разную толщину набрызгбетонного покрытия в своде и в стенах, если это целесообразно по результатам наблюдений за состоянием крепи.
Данная формула получена расчетом по предельному состоянию круговой пластины, работающей в упругопластическом режиме, защемленной по краям. При этом учитывается несовершенство защемления пластины по контуру; неровность поверхности и изменения толщины покрытия по площади пластины; частичное включение в работу пластинки омоноличиваемого в процессе набрызга поверхностных слоев грунта (коэффициент надежности по нагрузкам на пластину в расчетах принят равным 1,6).
3.33. При повышенных требованиях к надежности расчетов набрызгбетонной крепи (например, при использовании в качестве обделки) следует применять соответствующее математическое обеспечение по расчету крепей и обделок на ЭВМ (см. прил. 10).
Организация работ
3.34. В комплекс работ по возведению набрызгбетонного покрытия (крепи) входит: подготовка поверхности выработки, послойное нанесение покрытия, уход за свеженанесенным покрытием, контроль качества. В конструкциях крепи, содержащих помимо крепи другие элементы (анкеры, арки, металлическую сетку) в комплекс работ входит также установка и монтаж этих элементов.
3.35. Допустимое отставание возведения набрызгбетонного покрытия от забоя и порядок выполнения операций устанавливается проектом, исходя из конкретных инженерно-геологических условий. Наибольший эффект от применения набрызгбетона достигается при нанесении покрытия сразу после обнажения пород.
3.36. В невыветривающихся грунтах с устойчивостью выше средней допускается наносить набрызгбетонное покрытие с отставанием от забоя на 50 м и более (уточняется в процессе проходки).
В слабовыветривающихся грунтах средней устойчивости и ниже набрызгбетонное покрытие следует наносить без отставания от забоя. При буровзрывном способе покрытие наносят сразу после уборки породы.
В сильновыветривающихся грунтах, склонных к образованию локальных вывалов, интенсивному разуплотнению и трещинообразованию, отставание в нанесении набрызгбетонного покрытия не допускается. При буровзрывном способе проходки первый слой набрызгбетона следует наносить на свод и доступную часть стен после взрывания сразу после проветривания и оборки; последующие слои покрытия наносят после уборки породы.
Для крепления тоннельных выработок в плотных глинах естественной влажности (типа протерозойских) рекомендуется применение дисперсно-армированного набрызгбетона с армирующими волокнами и арматурными стержнями, которые устанавливаются по своду выработки и опираются одними концами в штрабу лба забоя, а другие их концы заводятся между грунтом и набрызгбетоном предыдущей заходки (рис.3).
3.37. Доведение набрызгбетонного покрытия до проектной толщины может выполняться сразу или поэтапно, что должно быть определено проектом, исходя из скорости проявления горного давления и особенностей технологии работ.
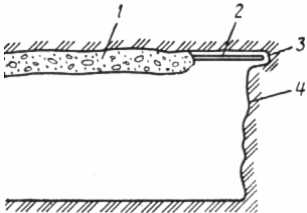
Рис. 3. Пример крепления тоннельных выработок в плотных глинах типа протерозойских:
1—набрызгбетон; 2—металлические стержни; 3—(штраба(; 4— лоб забоя
3.38. В зависимости от конкретных инженерно-геологических условий и принятой схемы организации работ операции по возведению крепи могут выполняться циклично отдельными заходками в соответствии с продвижением забоя или по поточной схеме после окончания проходческих работ на достаточно большой длине тоннеля.
3.39. Непосредственно перед нанесением набрызгбетона на поверхность выработки необходимо очистить ее от отслаивающихся кусков породы, продуть сжатым воздухом и промыть водой при давлении в шланге 0,2—0,3 МПа (промывка исключается, когда набрызгбетон наносят на слабые породы, склонные к размоканию, или на породы с отрицательной температурой).
3.40. При наличии фильтрации и сосредоточенных течей на поверхности породы вода должна быть отведена до нанесения набрызгбетона. Для этого в местах концентрированных течей следует пробуривать шпуры на глубину 10—20 см и устанавливать в них водоотводные трубки. Для выбора способа нанесения набрызгбетона на обводненные поверхности рекомендуется пользоваться данными приложения 12.
3.41. При возведении набрызгбетонных покрытий на обводненных поверхностях рекомендуется применять добавки для ускорения схватывания и твердения (см. приложение 6).
3.42. При нанесении набрызгбетона на поверхность породы с отрицательной температурой необходимо очистить ее от льда, продуть сжатым воздухом и при необходимости пескоструйным аппаратом. Промывать породу водой не следует во избежание образования ледяной корки.
3.43. Набрызгбетонирование армированных покрытий должно производиться при соблюдении следующих требований: арматурная сетка должна иметь ячейки размерами не менее 100 х 100 м при диаметре проволоки 2—4 мм и отстоять от поверхности породы не менее чем на 2 см.
3.44. Сетку прижимают к поверхности выработки, с помощью стержневых подхватов, заводимых за опорные плитки анкеров или привариваемых к выступающим концам анкеров.
При необходимости дополнительного крепления армосетки, например в случае больших неровностей контура, следует устанавливать специальные монтажные анкеры длиной 0,4(0,6 м или заделывать проволочные скрутки в первый (защитный) слой набрызгбетона. При резких колебаниях рельефа контура выработки, например при местных вывалах, для обеспечения требуемых зазоров сетку рекомендуется разрезать и концы ее подогнуть внутрь впадины с последующим дополнительным армированием в местах таких разрезов
3.45. В грунтах, склонных к размоканию или интенсивному разуплотнению из-за выветривания, трещинообразования и т. п., анкеры и сетку следует устанавливать после нанесения первого слоя, при этом надо применять анкеры на омоноличивающих составах, не содержащих воду, например на полимерной основе, а шпуры бурить без промывки.
При использовании набрызгбетона в комбинации с арочной крепью арки рекомендуется монтировать после нанесения первого (выравнивающего) слоя набрызгбетона.
При использовании решетчатых (арматурных) арок набрызгбетонирование выполняется после установки арки и монтажа арматурной сетки.
3.46. Сухую смесь для набрызгбетона следует, как правило, приготовлять централизованно на механизированных бетонных узлах при соблюдении точности дозирования по ГОСТ 7473—76.
Приготовление сухой смеси непосредственно в забое допускается при ограниченных объемах работ в случае, когда невозможно обеспечить доставку сухой смеси в забой в герметичных сосудах за время, меньшее времени схватывания цемента.
Максимальный срок доставки и хранения сухой смеси от момента ее приготовления до момента использования не должен превышать двух часов.
3.47. Доставку сухой смеси следует, как правило, выполнять в закрытых емкостях, капсулах или в сосудах, обеспечивающих ее побуждение, например в бетоносмесителях.
3.48. При ограниченных объемах работ и при коротких плечах возки в сухих выработках допускается доставка сухой смеси в шахтных вагонетках, контейнерах или кузовах автосамосвалов.
3.49. Набрызгбетонирование рекомендуется выполнять механизированным способом с помощью установленного на манипуляторе сопла, управление которым осуществляется оператором из защищенной кабины. Набрызгбетонирование с ручным вождением сопла целесообразно при малых габаритах выработки и незначительных объемах работ.
3.50. Набрызгбетон следует наносить слоями по 5—6 см. При применении быстротвердеющих смесей допускается увеличивать толщину слоев при условии неоплывания свежеуложенного материала и обеспечения его плотности в конструкции не менее 2,2 г/см3.
3.51. Для уменьшения количества отскока нанесение первого (выравнивающего) слоя набрызгбетонного покрытия на породу рекомендуется выполнять смесью без крупного заполнителя (гравия или щебня).
3.52. Набрызгбетонное покрытие следует наносить горизонтальными полосами последовательно снизу вверх, равномерно перемещая сопло по спирали вдоль полосы. Длина участка бетонирования и соответственно длина и ширина горизонтальных полос на этом участке принимаются в зависимости от организации проходческих работ, технических параметров и возможностей манипулятора.
При нанесении покрытия следует обеспечивать перекрытие свежим слоем ранее уложенного покрытия на величину не менее 20 см.
3.53. Для получения покрытия требуемого качества давление воздуха Рн.м в набрызгбетон-машине следует регулировать в зависимости от длины материального шланга, его диаметра, длины горизонтальных zr и вертикальных участков zb и количества поворотов шланга п. Ориентировочно параметры режима работы набрызгбетон-машины камерного типа при диаметре материального шланга (бетоновода) 50 мм рекомендуется определять по выражению:
Рн.м = Ра + ( zr + ( zB + (n,
где Ра(начальное давление при длине шланга 20 м, равное 0,09— 0,10 МПа; (—коэффициент потери давления на горизонтальном участке (для резиновых шлангов равен 0,0022—0,0025); (—коэффициент потери давления при подъеме смеси (для резиновых шлангов равен 0,007— 0,0076); (—коэффициент потери давления при повороте трубопровода на 90° (для резиновых шлангов равен 0,039—0,045).
Давление воздуха в набрызгбетон-машине роторного типа с диаметром материального шланга 65 мм рекомендуется принимать в зависимости от длины бетоновода следующим:
Длина бетоновода, м Давление в
машине, МПа
20 ............................... 0,2—0,25
40 ...............................0,25—0,35
60 ...............................0,35—0,45
80 ...............................0,45—0,50
Давление воздуха в машине необходимо уточнять опытным путем в зависимости от влажности смеси, крупности заполнителя и дозировки смеси, приняв за исходное давление, определяемое по пп. 3.55.
3.54. В процессе нанесения струя набрызгбетона должна быть направлена перпендикулярно к бетонируемой поверхности, а расстояние от сопла до этой поверхности—в пределах 0,7—1,5 м в зависимости от состава исходной смеси.
Так, при соотношении (Ц+П) : Щ ( 2 сопло рекомендуется располагать на расстоянии 0,7—1 м, а при (Ц+П) : Щ < 2 — на расстоянии 1,1—1,5 м с последующим уточнением на месте по результатам пробного нанесения покрытия.
3.55. Толщину набрызгбетонного покрытия следует контролировать с помощью специальных маяков (из цементного теста либо в виде металлических штырей), устанавливаемых в наиболее характерных точках сечения тоннеля, или с помощью передвижных лекал, а также маркшейдерскими замерами.
3.56. Для предотвращения деформаций и сохранения структуры свежеуложенного бетона проектом должны устанавливаться минимальные сроки между нанесением последующих слоев, которые следует уточнять по месту строительной лаборатории, исходя из скорости твердения бетона, температуры воздуха и прочих факторов, определяющих сроки набора набрызгбетоном требуемой прочности. При этом каждый последующий слой набрызгбетона разрешается наносить после приобретения предыдущим слоем прочности не менее 1 МПа.
При применении обычных цементов и добавок-ускорителей очередной слой набрызгбетона ориентировочно можно наносить через 20 мин на стены и 40 мин на свод.
При отсутствии добавок-ускорителей схватывания и твердения интервалы времени между нанесением слоев должны составлять не менее 2 ч.
3.57. Содержание воды в смеси устанавливает (регулирует) оператор по визуальной оценке: при пылении следует увеличивать расход воды до прекращения пыления, а при оплывании свежеуложенного бетона—уменьшить расход до прекращения оплывания.
При использовании водяного насоса для подачи воды расход ее следует назначать в соответствии с приложением 7, п. 15.
3.58. Набрызгбетон в период схватывания и твердения должен быть предохранен от замораживания, высыхания, сотрясений, механических повреждений и химических воздействий до набора прочности не менее 0,1 МПа.
3.59. Набрызгбетон через сутки после нанесения необходимо увлажнять распыленной струёй воды не менее 2 раз в сутки в течение 7 дней. При относительной влажности воздуха в тоннеле более 90% допускается поливать набрызгбетон 1 раз в сутки.
При снижении температуры воздуха ниже плюс 5°С увлажнять набрызгбетон не требуется.
3.60. Для предохранения поверхности набрызгбетона от высыхания рекомендуется покрыть ее раствором эмульсии или лака (поливинилацетатной эмульсией ПВА, поливинилхлоридной эмульсией ПВХ, этиленовым лаком и т. п.), наносимыми методом распыления.
3.61. Во избежание попадания воды из сопла в материальный шланг сопло в перерывах между нанесением покрытия следует держать насадкой вниз.
3.62. Возведение крепи из набрызгбетона должно выполняться оборудованием, обеспечивающим механизированное транспортирование, приготовление и нанесение смеси. В состав оборудования следует вводить:
транспортные средства для доставки смеси или ее составляющих к месту работы;
смесительное оборудование, обеспечивающее приготовление и тщательное перемешивание смеси;
дозирующие устройства;
механизмы для перегрузки сухой смеси с транспортных средств в смесительное оборудование;
машину для нанесения набрызгбетона;
загрузочное оборудование для подачи сухой смеси в машину;
резервуар с водой, обеспечивающий подачу ее к соплу под давлением;
устройства и приспособления для управления движением сопла в процессе набрызга.
Оборудование надлежит комплектовать в зависимости от конкретных условий производства.
При этом в зависимости от конкретных условий производства работ используются два основных типа:
передвижной набрызгбетонный узел, включающий набрызгбетон-машину в сочетании с самоходным или перемещаемым тягой агрегатом для нанесения набрызгбетона и установки анкеров, а также доставочными рельсовыми или безрельсовыми средствами;
технологический состав для доставки в выработку и подачу к соплу сухой смеси в сочетании с самоходным или перемещаемым тягой агрегатом для нанесения набрызгбетона и установки анкеров.
Основное технологическое оборудование современных механизированных комплексов для набрызгбетонирования приведено в приложении 13.
3.63. Монтаж армосетки при армировании набрызгбетонного покрытия надлежит проводить с буровой рамы, люлек самоходных буровых агрегатов или специальных тележек.
3.64. Оборудование механизированных комплексов следует монтировать на передвижных или самоходных транспортных средствах (шасси, тележках, платформах, автомобилях и пр.) в соответствии со схемами, приведенными в приложении 14.
3.65. В состав механизированных комплексов должны, как правило, включаться также следующие приспособления, инструменты и средства малой механизации:
сборники ручные для контроля состояния кровли;
телескопные перфораторы (или перфораторы с пневмоподатчиками) с буровым инструментом для разовых малообъемных буровых работ;
сварочный трансформатор для монтажа поддерживающего каркаса армосетки и срезки выступающих концов анкеров;
маневровые лебедки для перемещения технологических платформ и тележек в рабочей зоне прирельсового транспорта;
тормозные башмаки (для технологических тележек и платформ в прирельсовом транспорте);
комплект предупредительных знаков и сигналов для обозначения границ опасных зон.
3.66. Для обеспечения энергией отдельных механизмов технологического оборудования их электрические кабели. воздушные и водяные шланги должны быть оснащены быстроразъемными соединениями для подключения оборудования к соответствующим тоннельным коммуникациям.
3.67. Организация работ по возведению конструкций крепления из набрызгбетона должна определяться общей схемой организации строительства, т. е. принятыми в проекте транспортной схемой, типом используемых при строительстве транспортных средств, способом и местом приготовления сухой смеси, технологией набрызгбетонных работ и т. п.
Основные схемы организации работ и рекомендации по их выбору приведены в справочном приложении 13.
3.68. Оборудование для нанесения набрызгбетона должно быть обеспечено электроэнергией, сжатым воздухом и технической водой. Давление сжатого воздуха в сети должно быть не менее 0,5 МПа (5 кгс/см2), расход 8—10 м3/мин на одну машину. Давление воды должно превышать давление воздуха не менее чем на 0,1 МПа (1 кгс/см2) при расходе не менее 12 л/мин.
3.69. В случае приготовления сухой смеси вблизи объекта на специальном бетонном заводе ее доставку в выработку следует производить в технологических сосудах или в герметичных капсулах.
3.70. Сухую смесь рекомендуется приготовлять централизованно на бетонных заводах с упаковкой в капсулы или мешки, что позволяет стабильно обеспечить требуемое качество покрытия, улучшить санитарно-технические условия на рабочем месте при большей простоте механизации работ и меньших потерях сухой смеси.
3.71. Ведение взрывных работ в непосредственной близости от покрытия из набрызгбетона допускается при наборе им прочности не менее 1 МПа (10 кгс/см2).
Обеспечение и контроль качества набрызгбетонного покрытия
3.72. Нанесение набрызгбетонного покрытия при креплении подземных выработок должно выполняться специализированной бригадой, имеющей в своем составе опытного крепильщика, на которого возлагается операционный контроль (контроль качества выполнения всех технологических операций по нанесению покрытия).
3.73. Входной контроль качества используемых материалов и готовых смесей следует осуществлять в соответствии с общими правилами контроля выполнения строительных работ.
3.74. Операционный контроль в соответствии со СНиП III-44—77 должен включать в себя проверку соответствия технологического процесса (приготовление и транспортировка исходной набрызгбетонной смеси; подготовка поверхности под набрызг; техническое состояние комплекса оборудования; режимы нанесения набрызгбетонного покрытия; соблюдение требований по уходу за уложенным бетоном) требованиям, установленным проектом производства работ.
3.75. Контроль за приготовлением сухой смеси и транспортировкой (расход компонентов и время перемешивания) рекомендуется проводить непосредственно на месте приготовления (на БСУ). Результаты контроля следует заносить в журнал.
3.76. Режим набрызгбетонирования и соответствие работ по набрызгбетонированию ППР контролируется производителем работ.
3.77. Техническое состояние оборудования и питающих систем следует контролировать в соответствии с инструкцией по эксплуатации комплекса с фиксацией результатов контроля в специальном журнале с указанием места, даты и лица, осуществляющего контроль.
Таблица 6
Вид испытаний |
Частота проведенных испытаний1 |
Допустимые отклонения от проекта |
Исполнитель отбора образцов |
Исполнитель проведения испытаний |
Государственные стандарты, методики испытания |
Прочность при сжатии |
1 раз на 50 м тоннеля |
Только в большую сторону |
Бригада и обслуживающий установку персонал |
Строительные лаборатории |
ГОСТ 10180—78; ГОСТ 18105—86; ГОСТ 18105.0(80; ГОСТ 18105.2—80 |
Водонепроницаемость |
1 раз на 200 м
тоннеля |
То же |
То же |
То же |
ГОСТ 12730.5-84 |
Морозостой-кость |
То же |
” |
” |
” |
ГОСТ 10060—86 или по методике ускоренных испытаний (приложение 16) |
Сцепление с грунтом |
1 раз на 50 м тоннеля |
” |
” |
” |
По методике приложения 8 |
Прочность на растяжение осевое |
То же |
” |
” |
” |
ГОСТ 10180-78, ГОСТ 18105-86 |
Толщина набрызг-бетонного покрытия |
1 раз на 10 м тоннеля |
10% |
” |
Начальник смены |
Три замера на 100 м2 покрытия при установке маяков или щупов |
_________
1При изменении исходных материалов или условий производства работ проводятся все контрольные испытания.
В журнал заносятся также замечания по работе оборудования и задание на следующую смену дежурным слесарю и электрику.
3.78. Контроль за качеством уложенного набрызгбетона должен заключаться в визуальном осмотре и регулярном простукивании покрытия. На поверхности набрызгбетона не должно быть усадочных трещин, вздутий и отслоений. Глухой звук (бунение) указывает на неплотность прилегания набрызгбетона к породе или отслаивание по толщине. Обнаруженные дефектные места (оплывы, отслоения, выкрашивания, мелкие отдельные трещины и т. д.) подлежат устранению путем вырубки, очистки, промывки струёй распыленной воды, а затем заделки набрызгбетоном.
Все указанные виды операционного контроля следует проводить ежесменно с фиксацией данных контроля в соответствующих журналах (приложение 15).
3.79. Приемочный контроль является завершающей частью технологического процесса на определенной стадии строительства и осуществляется постадийно с использованием инструментальных, в том числе неразрушающих методов. Состав работ по контролю крепи из набрызгбетона, частота проведения контрольных испытаний, а также допустимые отклонения от проекта приведены в табл. 6.
3.80. Приемочно-сдаточный контроль законченного тоннеля осуществляется сначала рабочей комиссией, а затем государственной, при этом учитываются результаты входного, операционного и постадийного приемочного контроля.
3.81. Для повышения эффективности контроля качества возводимых тоннельных конструкций рекомендуется использовать статистические методы выборочного контроля на любой стадии возведения сооружения.
При всех видах производственного контроля должна быть выполнена оценка качества.
4. АНКЕРНАЯ КРЕПЬ
Конструкции и материалы анкеров
4.1. По характеру восприятия и передачи нагрузок анкеры подразделяются на две группы: закрепленные в породе концами и омоноличенные по всей длине.
Анкеры первой группы, усилия закрепления которых сохраняются или увеличиваются по мере извлечения их из шпуров, следует рассматривать как разновидность податливой крепи нарастающего сопротивления. Конец стержня со вставленным в прорезь клином образует замок анкера. Из анкеров этой группы наибольшее распространение имеют клинощелевые (рис. 4).

Рис. 4. Конструкция клинощелевых анкеров:
а—сплошной; б—составной; 1—гайка; 2—опорная шайба; 3—стержень;
4— прорезь; 5—клин; 6—контактная сварка
Анкеры второй группы (омоноличиваемые) обладают высокой жесткостью: при возрастании нагрузки до предельной у них практически не наблюдается перемещений. Они подразделяются на набивные, нагнетаемые, анкеры типа “Перфо”, сталеполимерные и предварительно-напряженные. Наиболее просты по конструкции и технологии установки набивные железобетонные анкеры.
4.2. При выборе типа анкера необходимо руководствоваться следующим.
Клинощелевые анкеры просты по устройству и в грунтах с коэффициентом крепости более 4 (сопротивление одноосному сжатию более 40 МПа) обладают достаточной прочностью закрепления в грунте.
Распорные анкеры (первая группа, рис. 5) можно применять в грунтах с коэффициентом крепости не ниже 3. Однако их конструкция более сложна и они могут быть изготовлены только в заводских условиях. Прочность их закрепления в массиве сравнительно невелика.
Железобетонные и сталеполимерные анкеры (вторая группа) при достаточной длине замка обеспечивают высокую прочность закрепления во всех грунтах, где анкерное крепление применимо. Они могут воспринимать поперечные смещения грунтов, так как их армирующие стержни омоноличены со слоями пород по всей длине шпура. Недостатком этих анкеров является невозможность их нагружения омоноличивающим раствором до необходимой прочности.
4.3. Анкерную крепь можно использовать как в качестве самостоятельной конструкции (одиночные анкеры с опорными шайбами и анкеры с сеткой), так и в сочетании с подхватами, арками, армированным и неармированным набрызгбетонным покрытием.
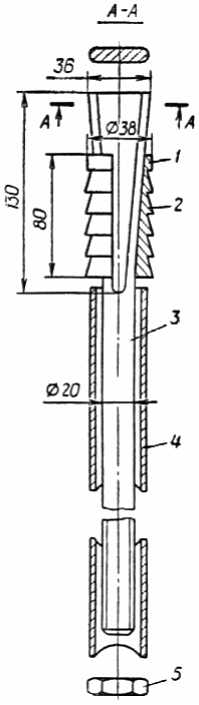
Рис. 5. Конструкция распорного анкера СКШ:
1—распорная муфта из двух полугильз; 2— проволочное кольцо; 3—стержень; 4— установочная труба; 5—гайка
4.4. Анкеры рекомендуется применять также в качестве монтажных элементов при установке арок, подтяжки ограждающих и арматурных сеток и т. п.
4.5. Одиночные анкеры следует применять только в монолитных, слаботрещиноватых и весьма устойчивых грунтах.
4.6. Анкерами с опорными шайбами и армирующей сеткой размерами 50х50 мм (диаметр проволоки 3 мм) следует крепить выработки, заложенные в устойчивых грунтах, в которых возможны небольшие отслоения. Сетку разрешается устанавливать в зависимости от степени трещиноватости грунтов только по своду, либо по своду и стенам выработки.
4.7. Анкерами с подхватом, объединяющим один их ряд, следует крепить выработки в грунтах средней устойчивости, трещиноватых и слаботрещиноватых. В качестве подхватов в зависимости от величины ожидаемых отслоений между анкерами следует применять полосовую сталь или прокатные профили.
4.8. Анкеры следует устанавливать рядами, желательно в шахматном порядке. Расстояние между анкерами должно определяться расчетом (см. пп. 4.42; 4.43) и указываться в проекте (паспорте) крепления.
4.9. В местах возможных (вероятных) локальных вывалов в промежутках между проектными анкерами должна быть предусмотрена постановка по месту дополнительных анкеров, количество, диаметр и глубина которых назначается производителем работ.
4.10. В подземных выработках со сводчатой кровлей анкеры следует располагать радиально. В выработках с плоской кровлей крайние анкеры необходимо устанавливать под, углом 30° к вертикали, но с таким расчетом, чтобы конец анкера выходил за пределы пролета выработки не менее чем на 40 см; средние анкеры устанавливаются вертикально (рис. 6).
4.11. Анкеры следует устанавливать вкрест явно выраженным плоскостям напластования или трещинообразования. При множественных разноориентированных плоскостях нарушений и в массивах нетрещиноватых и слаботрещиноватых анкеры следует устанавливать перпендикулярно закрепляемой поверхности.
4.12. Комплект клинощелевого анкера (см. рис. 4) включает анкерный стержень с резьбой на наружном конце и прорезью для клина на заглубляемом конце (замке), клин, гайку и опорную шайбу. Диаметр замкового участка анкерного стержня для шпуров от 40 до 42 мм составляет 36 мм, для шпуров от 36 до 37 мм—30 мм.
4.13. Комплекты распорных анкеров включают замки различных конструкций, расклинивающихся в шпуре при натяжении или вращении анкерного стержня (см. рис. 5).
4.14. Металлические клиновые и распорные анкеры рекомендуется изготавливать в заводских условиях, так как отклонения в размерах элементов и грубое исполнение деталей анкера значительно снижают прочность закрепления замков.
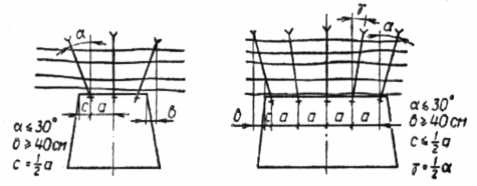
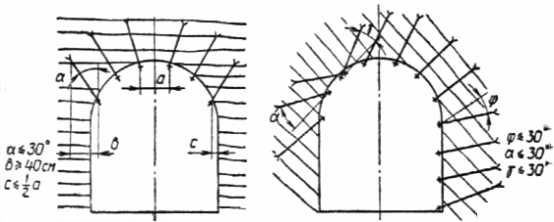
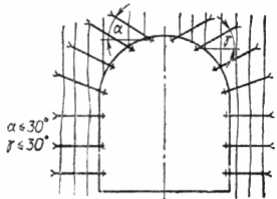
Рис. 6. Схема расположения анкеров при слоистой кровле
4.15. При изготовлении металлических анкеров необходимо выполнять следующие условия:
а) стержень должен быть прямым, а торцы—перпендикулярными к его оси; стержень длиной до 2 м рекомендуется изготовлять из стали марки Ст.З, при большей длине—из стали с более высоким пределом текучести; диаметр стержня клинового анкера определяют расчетом, однако, из условия обеспечения необходимой жесткости, он должен быть не менее 20 мм при длине анкера до 1,8 м и 25 мм—при длине анкера от 1,8 м до 3,3 м.
Если расчетный диаметр стержня анкера меньше диаметра его замка, то анкер целесообразно делать составным. Соединение замка со стержнем необходимо осуществлять на резьбе или контактной сваркой встык;
б) резьба должна быть образована накаткой; нарезка резьбы допускается при условии, если при расчете анкеров учтено ослабление в результате нарезки сечения стержня;
в) поверхность прорези в замке анкера должна быть гладкой, без заусенцев и окалины. Прорезь при ширине 2—4 мм не должна отклоняться от оси анкера более 1 мм; кромки прорези в верхнем конце анкера должны быть округлены; режущие кромки в торце замка должны быть острыми;
г) клин, отлитый из чугуна или штампованный из стали марки Ст.З, должен быть очищен от заусенцев и окалины;
д) гайки должны соответствовать ГОСТ 5915—70;
е) стыки составных анкеров должны быть равнопрочными со стержнем; длина резьбовых соединений должна быть не менее 40 мм;
ж) опорные шайбы из стали Ст.З должны иметь размеры от 100 х 100 х 8 до 200 х 200 х 12 мм.
4.16. Применение клиновых и распорных анкеров рекомендуется в технологических крепях для подвески ограждающих сеток и закрепления отдельных вывалов или неустойчивых участков обнажения.
4.17. Цельноомоноличиваемый набивной железобетонный анкер представляет собой арматурный стержень периодического профиля с заостренным заглубляемым концом, омоноличенный по всей длине шпура песчано-цементным раствором (рис. 7).
При использовании анкеров для подвески ограждающей сетки или армирующих элементов обделки наружный конец анкерного стержня должен иметь отверстие для шплинта.
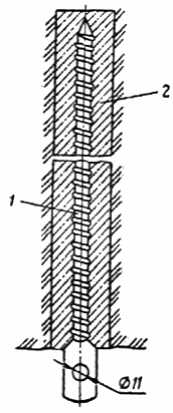
Рис. 7. Схема набивного железобетонного анкера:
1—арматурный стержень; 2— раствор
4.18. Железобетонные анкеры следует применять в слабообводненных или сухих выработках, расположенных в монолитных или слаботрещиноватых породах, т. е. в условиях, исключающих утечку или вымывание из шпура песчано-цементного раствора.
4.19. В комплект цельноомоноличиваемого анкера типа “Перфо” (рис. 8) входят арматурный стержень периодического профиля и перфоцилиндр с отверстиями диаметром от 4 до 6 мм, заполненный консистентным песчано-цементным, быстротвердеющим раствором.
Из приведенных на рис. 8 двух типов перфоцилиндров более удобным для снаряжения и установки анкера является щелевой.
4.20. Диаметры анкерных стержней и перфоцилиндров должны приниматься в зависимости от диаметра шпура в соответствии с данными табл. 7.
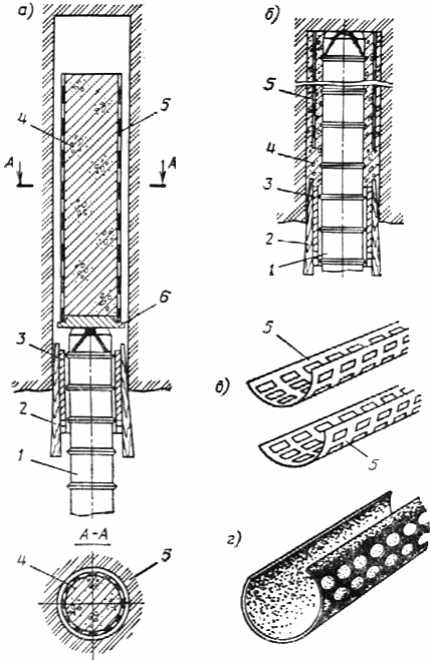
Рис. 8. Цельноомоноличенный анкер типа “Перфо”:
а—анкер в сборе при установке в шруп; б—анкер после установки;
в—перфоцилиндр разъемного типа; г—разрезной перфоцилиндр; 1—анкерный арматурный стержень; 2—деревянный клин; 3—кондуктор; 4(песчано-цементный раствор; 5— перфоцилиндр; 6—разрушаемое фибровое дно перфоцилиндра
Таблица 7
| | | |
Диаметры анкеров типа “Перфо”, мм |
шпура |
перфо-
цилиндра |
стержня-
анкера
“Перфо” |
стержня сталеполимермого или железобетонного набивного и нагнетаемого анкера |
34 |
29 |
18(22 |
16—18 |
36 |
31 |
22—25 |
18—20 |
40 |
35 |
25—28 |
22—25 |
43 |
38 |
28—32 |
25—28 |
4.21. Анкеры “Перфо”, ввиду их более высокой стоимости и сложности изготовления, рекомендуется применять в постоянных и временных конструкциях в условиях, непригодных для набивных железобетонных анкеров.
Наиболее целесообразно использование таких анкеров в интенсивно деформируемых и разуплотняющихся сильнотрещиноватых и обводненных грунтах.
4.22. Применяемые для железобетонных анкеров растворы должны состоять из материалов, соответствующих требованиям государственных стандартов: портландцемент— ГОСТ 10178—85; глиноземистый цемент—ГОСТ 969—77; песок—ГОСТ 10268—80; хлористый кальций—ГОСТ 450—77; вода—ГОСТ 23732—79.
4.23. С целью удовлетворения требованиям технологичности (свободное прохождение раствора через растворонагнетатель, подводящие шланги и инъектор, а также исключение вытекания раствора из шпуров) на месте производства работ допускается корректировать величину водоцементного отношения.
4.24. В комплект сталеполимерного анкера входят заостренный анкерный стержень из стали периодического профиля и ампул-патроны, заполненные пластораствором на основе эпоксидной, полиэфирной или других синтетических смол с капсулой, заполненной отвердителем.
Омоноличивание анкера после достижения им в течение 5—10 мин расчетной несущей способности осуществляют путем разрушения оболочек ампул-патрона и капсулы и последующего перемешивания их содержимого при внедрении в шпур и вращении анкерного стержня.
4.25. Цельноомоноличиваемые сталеполимерные анкеры с соответствующими быстросхватывающимися составами рекомендуется использовать в сложных гидрогеологических условиях, в том числе при высокой степени трещиповатости пород.
4.26. Армирующие стержни омоноличиваемых анкеров следует изготовлять из горячекатаной стали периодического профиля (ГОСТ 5781—82). Корневой конец стрежня должен быть заострен, другой конец—расклепан с отверстием для шплинта.
Допускается использование иных конструктивных решений концов стержня, выступающего в выработку (резьба с гайкой, петля и т. д.). Корневые концы сталеполимерных анкеров должны быть кососрезанными для обеспечения внедрения в ампул-патрон и качественного перемешивания пласторастворов.
4.27. Перед применением анкеров необходимо проверять свойства закрепляющих составов (методика по ГОСТ 5802—86) и проводить испытания анкеров, установленных на этих растворах.
4.28. Для закрепления в слабоустойчивых грунтах на глубину более 5 м подземных выработок пролетом более 10 м сопряжении выработок, а также откосов котлованов при соответствующем технико-экономическом обосновании следует применять омоноличиваемые в скважине по всей длине или в замковой части предварительно напрягаемые анкеры прядевой или стержневой конструкции (приложение 17)
4.29. Во всех обделках, а также в крепях, устанавливаемых в агрессивных средах или со сроком службы крепей от 1 года и более, анкерные стержни должны иметь покрытие в виде консистентной смазки, резиновой или полиэтиленовой рубашки, песчано-цементного камня и пр., обеспечивающее необходимую антикоррозийную защиту.
Расчет анкеров и составление паспорта
4.30. Параметры анкерной крепи—тип, размеры замка длина анкеров, расстояние между ними, величина натяжения стержней—определяются строением горного массива механическими свойствами грунтов и размерами подземной выработки. Как правило, параметры анкерной крепи следует назначать с учетом опыта ее применения в аналогичных инженерно-геологических условиях.
4.31. Основной эффект от крепления выработок анкерами состоит в том, что окружающие выработку породы, имеющие склонность к расслоению и обрушению, прикрепляются к устойчивым областям горного массива, лежащим за пределами расчетного свода давления, при помощи анкеров. В отдельных случаях кровля выработки, закрепленная анкерами, может рассматриваться как несущая армокаменная конструкция, уменьшающая высоту свода давления грунта.
4.32. Анкеры, применяемые в качестве временной крепи подземных сооружений, рассчитывают по прочности закрепления замков и прочности стержней по аналогии с соответствующими требованиями глав строительных норм и правил на проектирование тоннелей и бетонных (железобетонных) конструкций.
Под прочностью закрепления замка анкера понимают максимальную нагрузку, при приложении которой к стержню установленного анкера осевое перемещение его конца не превышает 10 мм.
4.33. В расчете основных параметров анкерной крепи (рис. 9), исходя из гипотезы “подвешивания” зоны возможного обрушения к ненарушенным грунтам, согласно требованиям к временному креплению, расчет следует производить в следующем порядке:
определить расчетную (рабочую) длину стержня анкера lр;
определить длину части анкера, заглубленную в ненарушенный грунт (замковой части) l3;
определить предельное расстояние между анкерами а по прочности закрепления заглубленной части замка;
выбирать диаметр и материал стержня dст.
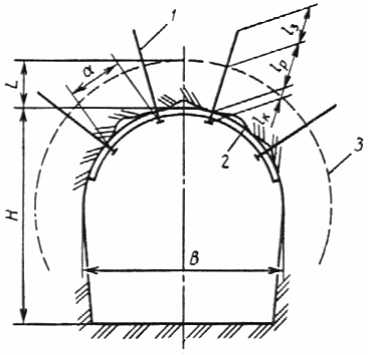
Рис. 9. Основные параметры анкерной крепи:
1—анкер; 2—шайба или подхват; 3—граница зоны возможного обрушения
4.34. Расчетную длину стержня анкера lр следует назначать равной не менее высоты возможного обрушения , принимаемой на основании опыта строительства в аналогичных инженерно-геологических условиях.
При отсутствии опытных данных расчетную глубину зоны возможного обрушения следует определять по формуле, м:

где Кт—коэффициент учета трещиноватости скальных грунтов, принимаемый здесь равным: для слаботрещииоватых грунтов 1; для трещиноватых 2; для сильнотрещиноватых 2,5.
Если коэффициент крепости грунта f (см. приложение 11) определен с учетом трещиноватости, то Кт=1.
В слабоустойчивых грунтах типа аргиллитов должно удовлетворяться условие
lр ( 0,5В (z—1),
где z—относительная величина, принимаемая в зависимости от глубины заложения тоннеля Н и предела прочности грунта на сжатие (к по номограмме (рис. 10).
Расчетную величину прочности закрепления заглубленной части необходимо корректировать натурными испытаниями согласно пп. 4.40.
4.35. Длину замковой части l3 и концевой части lк, выступающей в выработку, следует назначать конструктивно в зависимости от типа замка и конструкции крепления подхвата. При этом для клинощелевых анкеров длина замковой части должна быть не менее 20 см.
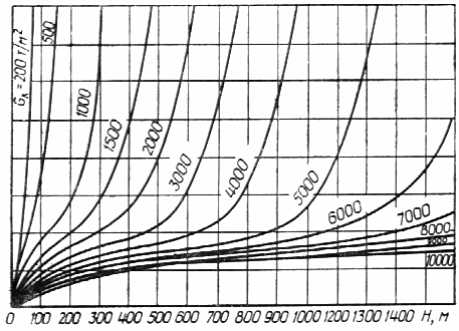
Рис. 10. Номограмма для определения относительных
размеров зоны возможного обрушения z в зависимости
от глубины заложения тоннеля
4.36. Разница между диаметрами шпура и замка клинощелевого анкера не должна превышать 8 мм. Толщину клина в в основании рекомендуется назначать равной диаметру замка анкера, но не менее величины, определяемой из выражения
вmin = 2l + (dш ( dа) + tп ,
где l—глубина внедрения “усов” анкеров и породу, принимаемая при отсутствии фактических данных но табл. 8; dш и da—соответственно диаметры шнура и замка анкера; tп—ширина прорези.
Таблица 8
| | | |
Коэффициент крепости грунта f |
10-20 |
6 |
4 |
Глубина внедрения l, мм |
2 |
4 |
6 |
Длину клина следует назначать конструктивно, но при условии, что его длина не должна превышать половину основания более чем в 12 раз.
4.37. Правильность назначения параметров замка необходимо обязательно проверить путем испытаний прочности за крепления замков в производственных условиях, проводимых в соответствии с указаниями пп. 4.71—4.81 настоящих Норм.
Для конструкций замков, приведенных в пп. 4.13; 4.14 и предназначенных для применения в грунтах с коэффициентом крепости 6—10 (“в куске”), разрешается принимать расчетную прочность закрепления по табл. 9 без предварительных испытаний.
Таблица 9
| | | |
Диаметр замка, мм |
Толщина клина, мм |
Диаметр коронки, мм |
Расчетная прочность закрепления, кН1 |
25 |
25 |
32 ( 1 |
90 |
36 |
25 |
41 ( 1 |
60 |
_________
1Расчетная прочность закрепления приведена для фрезерованных поверхностей прорези и боковых граней клина анкера.
4.38. В случаях, когда замки анкеров могут подвергаться воздействию попеременного замораживания и оттаивания, испытания замков на прочность закрепления следует проводить в талом грунте.
4.39. Длину замковой части железобетонных анкеров сначала назначают ориентировочно, как правило, в пределах от 20 до 60 см. При этом прочность N1, МПа, закрепления замка определяют по формуле
,
где —предварительная длина замка, см; dст—диаметр армирующего стержня, см; (сц—удельное сцепление бетона с армирующим стержнем, МПа, принимая по табл. 10.
Таблица 10
| | | | | |
Температура твердения, 0С |
(сц , МПа, при сроке твердения бетона, ч |
|
2 |
4 |
6 |
24 |
48 и более |
+5 |
0,5 |
1,0 |
1,5 |
4,0 |
4,5 |
+10 |
0,8 |
1,5 |
2,0 |
4,0 |
4,5 |
+15 |
1,0 |
2,0 |
3,0 |
4,5 |
4,5 |
+20 |
1,5 |
3,0 |
3,5 |
4,5 |
4,5 |
Примечания: 1. Удельные сцепления даны для следующих быстротвердеющих растворов:
указанного в п. 4.22 (для набивных анкеров); раствора из глиноземистого цемента марок 400—500 и воды (В/Ц=0,45—0,55) с добавкой 6% хлористого кальция от массы цемента (для нагнетаемых анкеров).
2. Удельное сцепление цементно-песчаных растворов состава 1 : 1 без ускорителей твердения следует принимать равным 4,5 МПа при глиноземистом цементе марок 400—500 в возрасте 48 ч и более; портландцементе марок 400—500 в возрасте 72 ч и более.
Ориентировочно прочность закрепления железобетонных анкеров с замковой частью длиной 50 см при температуре в шпуре не ниже +5°С допускается принимать:
при содержании СаСl2 5—6% от массы цемента 50 кН через 6 ч и 100 кН через 24 ч после установки; при содержании CaCI2 менее 3% от массы цемента 100 кН через 48 ч после установки.
Прочность закрепления замков железобетонных анкеров должна быть подтверждена результатами испытаний (см. п. 4.37).
4.40. Если результаты проведенных испытаний покажут прочность закрепления замков анкеров ниже расчетной, необходимо изменить конструкцию замка или отдельные параметры (диаметр, толщину клина и т. д.).
Длину замковой части железобетонных анкеров l3, м, на основе результатов испытаний следует откорректировать по соотношению:
,
где N—расчетная прочность закрепления, определяемая в результате испытаний, кН.
4.41. Для крепления тоннельных выработок запрещается применять анкеры длиной менее 1 м, а также анкеры с прочностью закрепления замка менее 40 кН.
4.42. Предельное расстояние между анкерами а, м, следует определять по формуле
,
где (гр—объемный вес грунта, кН/м3.
4.43. Чтобы исключить возможность образования вывалов между анкерами, должно быть выполнено условие а ( lр.
В сильнотрещиноватых породах расстояние между анкерами следует назначать не более 0,5 lр.
4.44. Расчетная нагрузка Р, кН, на анкер будет
P=1,5( a2 lр
где 1,5—коэффициент перегрузки.
4.45. Ориентировочно выбранный диаметр стержня анкера необходимо корректировать по формуле
,
где Р= l,5(гра2L, Ra—расчетное сопротивление материала стержня, кПа.
4.46. Для нетрещиноватых, слаботрещиноватых и трещиноватых грунтов с одной или двумя системами трещин, где возможно омоноличивание грунтовых блоков анкерами, крепь рекомендуется рассчитывать по гипотезе образования несущей конструкции из окружающих выработку грунтов (рис. 11). Представляя эту конструкцию в виде породной арки, следует пользоваться соотношением, связывающим длину анкеров la и расстояние между ними (межанкерное расстояние) а.
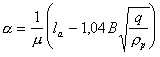
где коэффициент ( принимается равным
, для одиночных анкеров;
, при наличии групповой шайбы или подхватов;
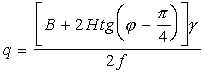
(р—предел прочности породы на растяжение (табл. 11)
;

Таблица 11
| | | | | | |
№
пп |
Горные породы |
Предел прочности на растяжение (p, МПа |
1 |
Порфирит |
20,0 |
2 |
Габбро-диабаз |
23,9—16,0 |
3 |
Базальт |
9,0—19,0 |
4 |
Алеврит |
8,0—12,0 |
5 |
Известняк |
9,0 |
6 |
Аргиллит |
4,6(7,1 |
7 |
Песчаник |
4,4—8,0 |
8 |
Сланец |
3,0 |
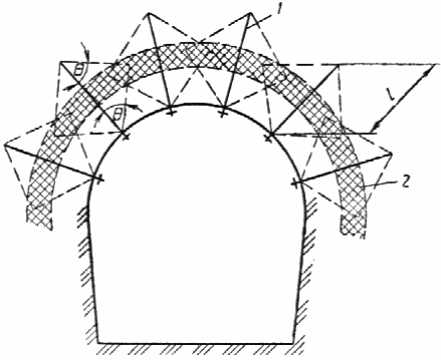
Рис. 11. Схема несущей породной конструкции,
образуемой вокруг выработки с помощью анкеров:
1—анкер; 2—несущая породная конструкция
4.47. При установке анкеров непосредственно возле забоя сразу после обнажения выработки в стержнях возникают дополнительные усилия, связанные с взаимовлияющим деформированием крепи и породы. Определение этих усилий рекомендуется выполнять по программе для ЭВМ “Анкер-контакт” (см. приложение 10), в которой учтены взаимное влияние анкеров, место и время их установки, ползучесть окружающего выработку грунта.
Технология установки анкерной крепи
4.48. Анкеры следует устанавливать сразу вслед за продвижением забоя. В слаботрещиноватых породах допускается отставание постановки подхватов или сетки (должно быть отражено в паспорте крепления), но не более чем на 20 м от лба забоя. В этом случае для навешивания подхватов или сетки па стальной анкер устанавливают вторую опорную шайбу и гайку.
4.49. Перед установкой крепи следует произвести тщательную оборку кровли и подтянуть ганки на двух последних рядах анкеров способом, указанным в п. 4.55 настоящих Норм.
4.50. Бурение шпуров под анкеры следует производить по размеченной сетке, строго соответствующей паспорту крепления, бурильными машинами с манипуляторами на самоходных шасси или на буровых рамах.
Допускается бурение анкерных шпуров телескопическими или ручными перфораторами с пневмоподатчиками.
4.51. Бурение с промывкой водой разрешается при последующей тщательной продувке шпура сжатым воздухом; в нестойких по отношению к воде грунтах бурение следует производить только всухую при обеспечении пылеулавливания (отсосе пыли).
4.52. Отклонения диаметра и длины шпуров от указанных в паспорте крепления не должны превышать соответственно 1 мм и 5 см.
4.53. Перед установкой необходимо осмотреть детали анкера. Смазка элементов замка должна быть удалена за исключением стержней корневых анкеров, где смазка предусмотрена как защита от коррозии. Запрещается устанавливать анкеры с плохо нарезанной или поврежденной резьбой, гнутым стержнем и прочими механическими дефектами.
4.54. При установке клинового анкера стержень с вставленным в прорезь на 20—30 мм клином вводят в шпур. Для создания предварительной расклинки следует доводить анкер до конца резким движением до упора в дно шпура, после чего анкер следует забивать пневматическим ударным инструментом со специальной насадкой до прекращения заглубления анкерного стержня.
Забивка анкера кувалдой допускается как исключение при установке отдельных анкеров или их малочисленных партий.
После забивки на наружный конец анкера следует установить опорную шайбу, гайку.
4.55. В клинощелевых и распорных анкерах сразу после установки следует произвести натяжение стержня для предотвращения расслоений и частичной релаксации напряжений в горном массиве.
Величина натяжения менее 40 кН (4 тс) при установке анкеров не допускается.
Гайки анкеров должны быть затянуты до отказа ключом длиной 0,7 м, либо пневматическим или электрическим сбалчивателем с крутящим моментом 350 кН(см.
4.56. В набивных железобетонных анкерах нагнетание раствора в шпуры следует производить растворонагнетателями.
4.57. Заполнение шпуров раствором производится через шланг с соплом в два приема; первая доза нагнетается при сопле, недоведенном на 20—30 см до дна шпура, вторая при сопле, выдвинутом к устью на 20—30 см.
4.58. Анкерный стержень следует устанавливать в шпур сразу после извлечения сопла и закреплять в устье шпура деревянным клином.
4.59. Зазор между стенками шпура и шлангом при нагнетании раствора и между стержнем и стенками шпура при установке следует перекрывать в устье резиновым или сальниковым уплотнением, препятствующим утечке раствора из шпура до твердения.
4.60. Навешивать сетку или подхват разрешается после достижения раствором 20%, а производить взрывные работы—60% проектной прочности. Сроки достижения этой прочности должны быть оговорены в паспорте крепления подземной выработки.
4.61. При анкерном креплении с жестким подхватом вначале следует установить анкеры в средней трети свода и к ним подвешивать подхват. Шпуры для остальных анкеров пробуривают через отверстия в подхвате, после чего устанавливают анкеры.
4.62. Если анкер установлен не перпендикулярно подхвату, вместо обычных опорных шайб следует устанавливать специальные: сферические, клиновые или из неравнобоких уголков.
4.63. Установку омоноличиваемых преднапрягаемых анкеров (рис. 12) производят после устройства оголовка в такой последовательности:
очистка скважины сжатым воздухом;
промер глубины скважины;
сборка анкера;
установка анкера в сборе в скважину на заданную глубину;
нагнетание раствора в корневой замок до истечения его из воздухоотводной трубки;
глушение нагнетательной и воздухоотводной трубок;
натяжение (после набора песчано-цементным камнем 100% прочности) анкерного стержня с фиксацией его в оголовке.
В анкерах с песчано-цементной изоляцией напрягаемого участка стержня нагнетание раствора в незаполненную часть скважины осуществляется после напряжения стержня.
4.64. При возможности утечки или вымывания раствора из скважины установку анкеров с нагнетаемым корневым замком (см. рис. 12) следует производить только после цементации, глинизации или силикатизации закрепляемой области породного массива.
4.65. Натяжение анкерных стержней следует производить гайкой при помощи динамометрического ключа или гидравлическими домкратами с цанговым или резьбовым захватом. Рекомендуется применять домкраты с цанговым захватом и полым штоком.
Домкраты и маслостанции должны быть укомплектованы тарированными манометрами.
4.66. Операции по установке анкеров с закрепляющим составом в ампул-патронах и жестким стержнем (рис. 13) осуществляются в такой последовательности:
заполнение шпура требуемым количеством ампул-патронов;
заглубление стержня с разрушением оболочек ампул и капсул до упора в дно, вращение стержня до начала схватывания полимерного состава;
натяжение и фиксация стержня после отверждения омоноличивающего состава (в анкерах замкового типа).
При использовании анкеров с канатной тягой операции по установке следует выполнять в следующей последовательности:
заглубление при помощи трубчатого упора анкера в сборе, включая требуемое количество ампул-патронов и уплотнительную диафрагму, до упора анкера в дно шпура;
досылка замковой части анкера трубчатым упором до отказа и вращение анкерного стержня до начала схватывания закрепляющего раствора;
извлечение трубчатого упора из шпура;
натяжение стержня после схватывания (отверждения) до достижения расчетной нагрузки и фиксация наружного конца в оголовке.
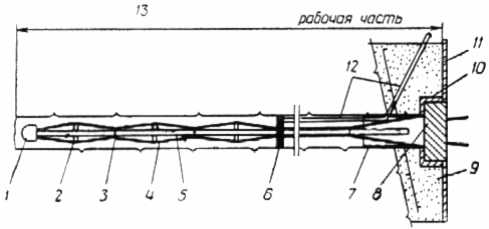
Рис. 12. Нагнетаемый корневой многопрядевый анкер:
1—наконечник; 2—распорки; 3—хомут; 4—арматурная высокопрочная прядь;
5—растворонагнетательная трубка; 6—разделительная диафрагма; 7—кондуктор; 8—фиксатор натяжения арматурных прядей; 9—железобетонный оголовок; 10— гнездо фиксатора;
11—металлическая опорная плита; 12—воздухоотводная трубка; 13— корневой замок
467. Установку анкеров с жестким анкерным стержнем с размещением закрепляющего раствора в ампул-патронах рекомендуется осуществлять анкероустановочными модулями, смонтированными на манипуляторах буровых установок и позволяющими с одной позиции выполнить механизированно весь комплекс операций—бурение шпура, подачу в шпур ампул-патронов и установку анкерного стержня.
4.68. Операции по установке цельноомоноличиваемых стержневых анкеров типа “Перфо” следует производить в такой последовательности:
приготовление песчано-цементного раствора;
формовка и заполнение раствором перфоцилиндров;
заглубление перфоцилиндров в шпур с последующим внедрением арматурного стержня на заданную глубину, фиксация стержня деревянным клином в устье шпура.
Формовку и заполнение раствором перфоцилиндров производят в шаблоне на верстаке вблизи места установки анкеров партиями не более 8—10 шт. Готовые перфоцилиндры скрепляют проволокой или хомутами через 0,3—0,5 м.
4.69. Забивку в шпур анкерного стержня следует производить пневматическим инструментом (отбойным или чеканочным молотком, перфоратором с насадкой).
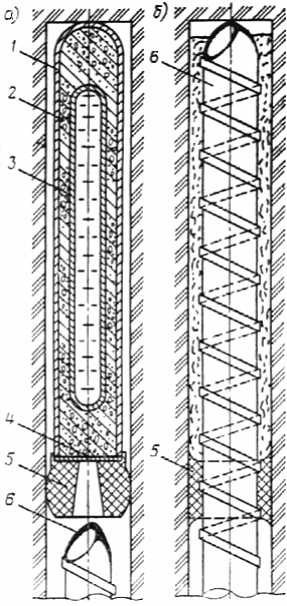
Рис. 13. Корневой сталеполимерный анкер:
а—анкер в сборе в процессе установки в шпур; б—анкер после установки: 1(ампул-патрон;
.2—пластораствор; 3—капсула с отвердителем; 4—разрушаемое (фибра, резина и т. п.) дно;
5—разделительное эластичное уплотнение; 6—анкерный арматурный стержень
4.70. При установке преднапряженных анкеров типа “Перфо” с плунжером на замковом конце анкерного стержня (рис. 14) последовательность операций должна быть такой:
приготовление песчано-цементного раствора;
заполнение раствором и формовка перфоцилиндров в количестве не более 3 шт. при ранее уложенном в перфоцилиндр анкерном стержне;
установка анкера в сборе в скважину до упора в дно;
внедрение плунжера в перфоцилиндр с вытеснением раствора в зазор между перфоцилиндром и стенками скважины;
натяжение анкерного стержня после набора песчано-цементным раствором проектной прочности с фиксацией наружного конца в оголовке.
Внедрение плунжера в перфоцилиндр может производиться двумя способами:
надвижкой вглубь скважины перфоцилиндра трубчатым упором (например, буровым снарядом, подаваемым буровым станком) при зафиксированном в устье скважины рабочем стержне;
вытягиванием анкерного стержня натяжным устройством (домкратом или механизмом подачи бурового станка) при застопоренном в скважине трубчатом упоре или распорном стопоре перфоцилиндра.
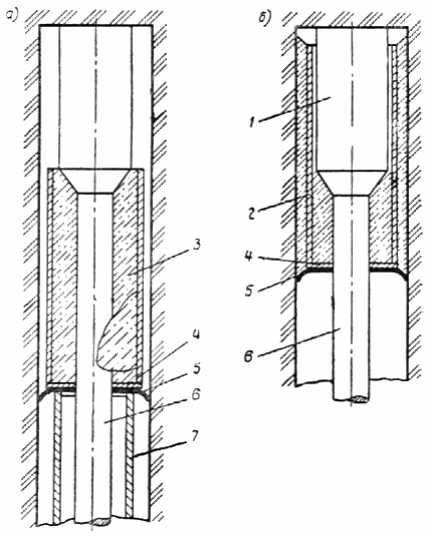
Рис. 14. Схема плунжерного корневого анкера типа “Перфо”:
а—анкер в сборе в процессе установки; б—анкер после установки; 1—плунжер;
2—перфоцилиндр; 3—песчано-цементный раствор; 4— жесткое дно перфоцилиндра;
5—разделительная диафрагма-уплотнение; 6—анкерный стержень; 7—трубчатый упор
Испытания анкеров на прочность закрепления.
Контроль качества при возведении анкерной крепи
4.71. Установку анкеров следует производить только под наблюдением ответственного представителя технического персонала, имеющего необходимый опыт, на которого возложен операционный контроль и обеспечение соответствия конструкции анкеров и шпуров проекту (паспорту крепления), а также контроль за проявлением особенностей инженерно-геологических условий, влияющих на качество и эффективность анкерной крепи.
Выработки, закрепленные анкерной крепью, следует осматривать ежесуточно. Осмотр производится начальником участка или его заместителем и участковым маркшейдером. Начальники смен и сменные маркшейдеры должны осматривать призабойные участки выработок с анкерной крепью ежесменно.
4.72. Все отступления от проекта при установке анкеров подлежат исправлению, либо должны быть обоснованы и согласованы с представителями, компетентными принимать решения по изменению паспорта крепления или его корректировке.
4.73. Определяющие параметры в виде расчетных значений характеристик анкерного крепления, подлежащие выходному контролю, должны быть указаны в паспорте крепления выработки.
Обязательным является включение в число определяющих параметров анкеров, контролируемых с особой тщательностью и ответственностью, расчетных значений несущей способности замков (для клиновых и других анкеров этого типа) или прочности закрепления замковой части анкеров омоноличиваемой конструкции (железобетонных, на пласторастворах и т. д.).
4.74. Для испытания анкеров рекомендуется применять гидравлический домкрат типа СМ-514 с насосной станцией, а также комплект гидроинструмента УВШ-5/15.
4.75. При проведении испытаний металлические анкеры следует устанавливать в кровле или в стенах выработки, но обязательно в тех инженерно-геологических условиях, в которых они будут применяться. Железобетонные анкеры и анкеры на пласторастворах необходимо устанавливать для испытаний только в кровле выработки, причем осуществлять .проверку только прочности закрепления замковой части.
Длина металлических анкеров, отобранных для испытаний, должна соответствовать паспорту крепления.
Для определения прочности закрепления необходимо испытать не менее 10 анкеров.
4.76. Перед началом испытаний необходимо снять с установленных анкеров гайки и опорные шайбы, выровнять поверхность выработки вокруг анкеров и удалить выступы, мешающие опиранию домкратов. На анкер следует надеть сферическую шайбу и навинтить гидравлический домкрат. Нагрузка должна фиксироваться по показателям манометра.
Перемещение конца анкера следует определять, как правило, с помощью теодолита. В скальных грунтах с коэффициентом крепости более 6, Rc(60 МПа, когда есть уверенность, что грунт под сферической шайбой не будет сминаться, допускается измерять перемещение конца анкера с помощью линейки.
4.77. При испытаниях металлических анкеров нагрузку следует прикладывать ступенями через 10 кН, начиная с 40 кН, и при каждой ступени нагрузки фиксировать перемещение. Испытания следует прекратить при достижении перемещения 10 мм. Полученные результаты отмечают в журнале испытаний (приложение 18).
4.78. При испытаниях прочности закрепления замков железобетонных и сталеполимерных анкеров перемещения не измеряют, а фиксируют только максимальное усилие, развиваемое испытательным домкратом, которое резко падает при нарушении сцепления стержня с раствором.
В случаях, когда шаг и длина таких анкеров приняты .конструктивно заведомо больше расчетных значений по несущей способности при испытании их усилием, превосходящим расчетное в 1,5 раза, вырыва анкера может и не произойти В этих случаях дальнейшее нагружение не производят, а несущую способность замка условно принимают равной этому испытательному усилию.
4.79. Результаты натурного определения прочности закрепления замков анкеров следует обрабатывать по форме указанной в табл. 12.
Таблица 12
| | | | | | |
Номера испытанных анкеров |
Прочность закрепления замка |
Отклонения от среднего арифметического |
Квадраты отклонений величин от среднего арифметического |
1 |
N1 |
Nн( N1 |
(Nн( N1)2 |
2 |
N2 |
Nн( N2 |
(Nн( N2)2 |
3 |
N3 |
Nн( N3 |
(Nн( N3)2 |
( |
|
|
|
n |
Nn |
Nн( Nn |
(Nн( Nn)2 |
|
(Ni |
— |
((Nн( Ni)2 |
|

|
(
|
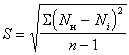
|
Разброс результатов испытания оценивают коэффициентом вариации V=S/Nн. Результаты следует считать удовлетворительными, если V(0,25. При V>0,25 испытания анкеров необходимо повторить. Разброс результатов можно уменьшить путем повышения качества изготовления анкеров и освоения технологии их установки.
Конечной целью обработки результатов испытаний является определение расчетной прочности закрепления N, вычисляемой по формуле

4.80. Для замков, находящихся в условиях сезонного замораживания и оттаивания, расчетное значение прочности закрепления принимают с понижающим коэффициентом 0,85.
4.81. При определении прочности закрепления замка должна быть исключена возможность пластических деформаций стержня анкера.
Появление пластических деформаций стержня характеризуется наличием перемещений его конца без увеличения давления жидкости в домкрате.
4.82. Натяжение установленных в выработке металлических анкеров с течением времени уменьшается. Снижение напряжения до величины менее 20 кН не допускается. Для контроля за изменением натяжения следует применять предварительно протарированные пружинные шайбы, гипсовые маячки или резиновые динамометры.
Допускается определять натяжение по величине крутящего момента при завинчивании гайки анкера.
Контролю подлежат не менее 2% всех установленных металлических анкеров, но не менее 10 штук.
4.83. По усмотрению главного инженера строительной организации не реже чем 1 раз в два месяца необходимо производить осмотр всех анкеров и в необходимых случаях производить подтягивание гаек. Эти работы должны выполнять квалифицированные крепильщики.
Результаты осмотра анкеров с указанием пикетов и устраненных нарушений, результаты контроля натяжения и выборочных испытаний анкеров, а также допущенные отклонения от паспорта анкерной крепи следует заносить в журнал производства горных работ, предусмотренный главой СНиП на строительство тоннелей.
5. ОСОБЕННОСТИ ПРОЕКТИРОВАНИЯ КОМБИНИРОВАННЫХ КОНСТРУКЦИЙ
5.1. Комбинированные конструкции крепей из сочетании анкеров с набрызгбетоном, арок с набрызгбетоном, анкеров с арками и набрызгбетоном следует рассчитывать на нагрузки, определяемые в соответствии с п. 3.26. При этом необходимую толщину набрызгбетона следует определять в соответствии с пп. 3.29, 3.30.
5.2. Обделки из набрызгбетона и анкеров рекомендуется рассчитывать как многослойные конструкции, внешний слой которых—омоноличенная (набрызгбетоном, анкерами) породная зона (рис. 15). В качестве исходных данных для расчета следует принимать: толщину породобетонного слоя hо с усредненным модулем деформации Е2; толщину слоя грунта, омоноличенного анкерами ha с модулем деформации E1; толщину набрызгбетонного покрытия hн с модулем деформации Eн. В результате расчета определяется нормальное давление Pо и сдвигающее усилие Рс на контакте “обделка(грунт”.
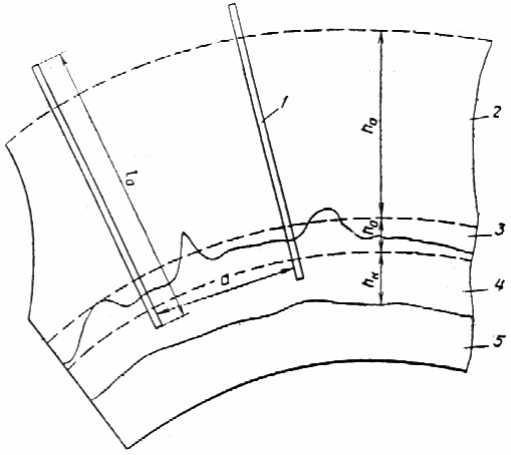
Рис. 15. Конструкция комбинированной анкер-набрызгбетонной крепи (обделки):
1—анкер: 2—слой грунта, “прошитый” анкерами; 3—породобетонный слой; 4— первичная крепь: 5—вторичная крепь (обделка)
Толщину hо бетонопородного слоя (см. рис. 15) следует определять на основании натурных измерений или теоретически.
Для вычисления указанных параметров конструкции рекомендуются следующие выражения:
,
где (т—ширина трещин, см; Кт—категория трещиноватости;
E2 = (0,5(0,7)Е + (0,5(0,3)Ен ,
где Е—модуль деформации грунта “в куске”, МПа.
, где 
, где ;
(—коэффициент Пуассона грунта.
5.3. Сцепление Рс на контакте “обделка—порода” необходимо проверять на выполнение условия
,
где Ро—нормальное давление грунта на обделку, МПа; f*—коэффициент трения по контакту “обделка—порода”; К*—сцепление “обделка—порода”, МПа.
При невыполнении этого условия возможно проскальзывание покрытия по контакту, в этом случае обделку следует рассматривать как обычное монолитное кольцо.
Анкеры повышают надежность совместной работы набрызгбетонного покрытия с породой. При этом перемещение конца анкера Wp, в см, должно удовлетворять условию
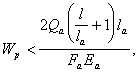
где Qa—предельная несущая способность анкера, кН.
5.4. При проектировании анкер-набрызгбетонной обделки в грунтах, склонных к ползучести, последнюю следует учитывать, полагая модуль деформации Е и коэффициент Пуассона у грунта функциями времени, определяемыми путем натурных исследований, МПа:
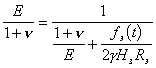
где fэ (t)—конвергенция экспериментальной выработки, м; Нз—глубина заложения выработки, м; Rэ—радиус экспериментальной выработки, м.
В качестве условия устойчивости выработки в таких грунтах в различные периоды времени рекомендуется пользоваться соотношением:
,
где f(zy)—функция, учитывающая место установки крепи, допускается принимать f(zy)=
5.5. При проектировании анкер-набрызгбетонной обделки в сейсмических зонах параметры конструкции, полученные расчетным путем, следует проверять в соответствии с “Инструкцией по учету сейсмических воздействий при проектировании горных транспортных тоннелей” (ВСН 193—81). М., ВПТИтрансстрой, 1982.
Особенность расчета в этом случае состоит в том, что напряжения сжатия от сейсмических волн следует суммировать со статическими напряжениями сжатия в первичной обделке, что может явиться причиной разрушения обделки в то время, как напряжения растяжения от сейсмических волн могут стать опасными для менее нагруженной вторичной обделки.
5.6. Варьируя межанкерное расстояние а, длину анкера lа и толщину покрытия из набрызгбетона hн, добиваются устойчивости выработки при минимальных затратах труда и материалов на их возведение. Задача оптимизации комбинированной конструкции в этом случае сводится к определению такого сочетания параметров крепи а, lа и hн, при котором будет обеспечено устойчивое состояние выработок и вместе с тем минимизируются функции себестоимости и трудозатрат на возведение крепи (целевая функция).
Методика решения этой задачи и выбора оптимальных значений параметров анкер-набрызгбетонной крепи в большом диапазоне горно-геологических условий приведена в приложении 19.
5.7. При расчете конструкции арочно-набрызгбетошюй крепи следует учитывать, что набрызгбетон может быть использован: в качестве затяжки между арками; как забутовка, обеспечивающая гарантированный контакт по периметру выработки; как элемент обделки, для которой арки являются армирующим элементом. В зависимости от функций, в расчетной схеме должны приниматься соответствующие условия контакта конструкции с контуром выработки. Принципы оптимизации параметров арочно-набрызгбетонной крепи приведены и приложении 20, расчет арочной крепи как самостоятельной конструкции приведен в приложении 21.
5.8. При проектировании арочно-анкерной крепи длину анкеров ориентировочно можно выбирать по п. 4.34 таким образом, чтобы она превосходила глубину зоны возможного обрушения.
Упругие опоры, моделирующие контакт с породой, следует совмещать с местами установки анкеров, причем жесткость опоры в направлении внутрь выработки—по формуле:

где Еа—модуль упругости материала анкера, МПа; Fa—площадь сечения анкерного стержня, м2; lс—свободная (до замка) длина анкера, м.
6. КОНТРОЛЬ И ОЦЕНКА СОСТОЯНИЯ КРЕПИ
6.1. При сооружении тоннеля с использованием набрызг-бетонной крепи в грунтах, заметно проявляющих горное давление, для обеспечения безопасности работ необходимо помимо обоснованного назначения параметров крепи также проведение специальных наблюдений с последующей оценкой состояния крепи.
6.2. Оценивать состояние системы крепления следует, прежде всего, по скорости прироста деформаций контура выработки, а также по абсолютной величине деформации (конвергенции). На основе этих оценок принимают решение о необходимости возведения постоянной обделки или усиления временной крепи.
Дополнительно целесообразно измерять усилия в элементах крепи, сопоставляя их с предельными для повышения значимости обоснования решения.
6.3. Конвергенцию выработки следует определять по осадкам свода выработки нивелированием и измерением сближения стен. Точность измерения должна составлять не менее 0,5 см. В крепких слабодеформируемых грунтах точность измерений должна быть повышена, например с помощью рулетки ЦНИИС (точность 0,2 мм) и прецизионного нивелирования.
6.4. Частоту проведения измерений следует выбирать в зависимости от скорости изменения параметра. Чтобы надежно зафиксировать начальные изменения параметров, следует вначале проводить частые измерения (от 1 раза в смену до 1 раза в сутки). При стабилизации параметров допускается уменьшать частоту измерений (до 1 раза в один-три месяца).
6.5. Сначала измерения проводят в сечениях, удаленных друг от друга на расстояние 10—30 м. На участках значительных геологических изменений, а также участках изменений расположенного над тоннелем массива, участках сбросов и разрушенных слоев измерения проводят на более близком расстоянии (5—10 м). При выявлении участков значительных деформаций оборудуют дополнительные измерительные сечения.
6.6. Оценку состояния системы крепления рекомендуется проводить путем сопоставления:
эталонной и реальной кривых конвергенции;
предельного значения конвергенции и реальной конвергенции.
Дополнительно для повышения достоверности выводов можно сопоставить реальные усилия в конструкции крепи с предельными расчетными усилиями для данных конструкций.
6.7. Эталонную кривую конвергенцию с учетом полученных опытным путем характеристик грунта (уточненных реологических параметров грунта, определяемых с помощью замеров конвергенции Wk=fk(t) стен экспериментальной выработки радиусом Rэ) определяют по выражению:
,
Расположение на графике реальной кривой конвергенции над эталонной свидетельствует о развитии зон неупругих деформаций в грунте, окружающем выработку, и является предупреждающим сигналом к необходимости принятия решения об усилении крепи. Таким выработкам следует уделять повышенное внимание.
Предельное значение конвергенции, обеспечивающее прочность элементов крепи, определяют по формуле:
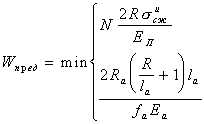
6.8. Усиление крепи (корректировка ее конструктивных параметров) необходимо при условии, если в какой-либо момент времени

Параметры крепи предварительно уточняют с использованием эталонной кривой конвергенции при условии

Рекомендации по устранению возможных дефектов в обделке из набрызгбетона приведены в приложении 22.
6.9. Дополнительно рекомендуется измерять напряжения в анкерах. При помощи глубинных реперов измеряется абсолютная разность смещения точек грунта у концов анкера . Усиление крепи необходимо, если реальное усилие в анкере больше расчетного предельного усилия в анкере или несущей способности анкера, т. е. если не выполняется условие
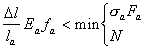
7. ТЕХНИКА БЕЗОПАСНОСТИ
7.1. Работы по креплению выработок должны выполняться в соответствии с требованиями следующих документов:
1. СНиП III-4—80*. Техника безопасности в строительстве. (М., Стройиздат, 1989).
2. Правила техники безопасности и производственной санитарии при строительстве метрополитенов и тоннелей (М., Оргтрансстрой, 1975).
3. Правила технической эксплуатации железных дорог Союза ССР (М., Транспорт, 1985).
4. Правила технической эксплуатации метрополитенов Союза ССР. (М., Транспорт, 1985).
5. Инструкция по движению поездов и маневровой работе на железных дорогах Союза СССР (М., Транспорт, 1985).
6. Инструкция по движению поездов и маневровой работе на метрополитенах (М., Транспорт, 1978).
7. Инструкция по сигнализации на железных дорогах Союза ССР (М., Транспорт, 1985).
8. Инструкция по сигнализации на метрополитенах (М., Транспорт, 1978).
7.2. Рабочие и инженерно-технический персонал, выполняющие работы по установке анкеров и нанесению набрызгбетона, должны быть ознакомлены с принципами работы этих видов крепи, их конструктивными особенностями и паспортом под расписку.
7.3. Паспорт крепления должен быть вывешен вблизи забоя или на фанере или металле.
7.4. Работы, связанные с обслуживанием стандартных машин, механизмов и приспособлений, должны выполняться в соответствии с требованиями типовых инструкций и указаний по технике безопасности для данного оборудования.
При обслуживании нестандартного оборудования, механизмов и приспособлений местного изготовления следует руководствоваться требованиями инструкций по их эксплуатации, утвержденными главным инженером строительной организации.
7.5. Напорные емкости (бак для воды, ресивер и т. п.) должны быть снабжены паспортами, инструкцией по обслуживанию и зарегистрированы в Госгортехнадзоре.
Установки и трубопроводы, работающие под давлением, не реже 1 раза в три месяца должны подвергаться гидравлическим испытаниям на давление, превышающее рабочее в 1,5 раза.
7.6. Запрещается пользоваться установками и аппаратами, работающими под давлением, при отсутствии или неисправности манометров и предохранительных клапанов. Исправность манометров необходимо проверять ежедневно перед началом смены.
7.7. Устранение неисправностей, чистка и смазка оборудования или отдельных его узлов, подтягивание соединений в трубопроводах должны проводиться после снятия давления воздуха и отключения сети электропитания.
7.8. При закреплении поверхности выработок на высоте более 2 м работы должны проводиться со специальных подмостей или технологической тележки.
7.9. Конструкция технологических платформ, тележек, площадок и другого оборудования для производства работ по установке анкеров и нанесению набрызгбетона должны соответствовать “Правилам по технике безопасности и производственной санитарии при строительстве тоннелей и метрополитенов” (М., Оргтрансстрой, 1975).
Все площадки на тележке на высоте более 1,5 м должны быть оборудованы ограждающими перилами высотой не менее 1 м и сплошным настилом с бортовой доской высотой не менее 15 см.
7.10. До установки крепи необходимо произвести тщательную оборку кровли, лба забоя и боков выработки, а также проверить на призабойном участке состояние ранее установленной крепи.
Нарушения крепи, вызванные взрывными работами, должны быть устранены немедленно.
7.11. Запрещается снимать или ослаблять гайки после установки анкерной крепи. Для замены сетки и дополнительного навешивания подхватов необходимо устанавливать вторую опорную шайбу и гайку.
7.12. Запрещается производить подработку породы около анкеров для установки затяжки.
7.13. Запрещается крепить на выступающие в выработку концы анкеров или на подхваты вентиляционные трубы и леса. Для этой цели нужно использовать специально установленные анкеры.
7.14. При установке железобетонных анкеров сопло должно быть снабжено специальным козырьком для защиты крепильщика от смеси, вылетающей из шпура.
7.15. Растворонагнетатели должны быть проверены в соответствии с правилами Котлонадзора.
7.16. При появлении на закрепленной анкерами породе свежих трещин необходимо на опасном участке установить дополнительное анкерное или стоечное крепление.
7.17. Испытывать анкерную крепь следует в закрепленной выработке. Во время испытаний необходимо следить за состоянием устойчивости выработки.
7.18. При проведении испытаний анкеров гидравлический домкрат должен быть подвешен к элементам крепи, чтобы при разрыве стержня анкера исключить возможность падения домкрата.
7.19. Находиться против испытываемого анкера или под ним запрещается. Не разрешается производить замеры перемещений во время работы насосной станции.
7.20. При возведении и испытаниях анкерной и набрызг-бетонной крепи запрещается нахождение лиц, не связанных с этими работами, в пределах опасной зоны:
при нанесении набрызгбетона—не менее 30 м; при оборке—не менее 15 м; при прочих работах—не менее 10 м.
7.21. Рабочие места машиниста набрызгбетон-машины и сопловщика должны быть оборудованы двухсторонней звуковой и световой сигнализацией. Персонал должен быть под расписку ознакомлен с системой сигналов, а таблицы сигналов—вывешены на рабочих местах.
7.22. Машинисту набрызгбетон-машины запрещается подавать сжатый воздух в машину и включать ее в работу без сигнала сопловщика.
7.23. Перед началом работы материальные трубопроводы и шланги должны быть продуты сжатым воздухом. Запрещается перегибать материальные шланги, а также устранять пробки путем подачи воздуха под давлением, превышающим рабочее.
Во время продувки материального шланга в начале и в конце работы или после устранения пробки запрещается держать в руках сопло или свободный конец материального шланга. Они должны быть отведены в сторону от места нахождения или постоянного движения людей и закреплены.
Рабочие, непосредственно не занятые на этой работе, должны быть удалены из рабочей зоны на расстояние не менее 30 м.
7.24. В процессе бетонирования сводовой части выработки рабочие не должны находиться под поверхностью свеженанесенного набрызгбетона. Запрещается производить работы в двух ярусах но одной вертикали при отсутствии между ярусами сплошного настила.
7.25. Рабочее место сопловщика и место размещения технологической установки должно быть оборудовано системой вентиляции. Запыленность воздуха в пределах рабочего места не должна превышать 5 мг/м3.
7.26. Рабочие, приготовляющие смесь для набрызгбетона, должны работать в предохранительных очках с небьющимися стеклами и респираторах, сопловщики—в резиновых перчатках и предохранительных масках и в спецодежде, предусмотренной действующими нормами для бетонщиков. Лицо и руки сопловщик должен смазывать вазелином или специальной защитной пастой.
7.27. Разгрузка, а также очистка барабанов и корыт смесительных машин лопатами и другим ручным инструментом во время работы машин запрещается. Очистка допускается только после полной остановки машины и снятия давления воздуха.
7.28. Передвижение технологических тележек или подмостей на очередной участок следует производить только с разрешения лица, ответственного за ведение работ по креплению, после осмотра закрепленного участка выработки и соответствующей записи в журнале.
После передвижки на очередной участок тележку следует застопорить тормозными устройствами, подложить под колеса тормозные башмаки и оградить опасную зону специальными сигнальными знаками.
7.29. Все места работы, а также лестницы и проходы должны иметь освещение. В местах нанесения покрытий источники света должны быть расположены так, чтобы на рабочие поверхности не попадали тени от работающего, его инструмента или элементов оборудования. Все осветительные приборы, расположенные в зоне работы сопловщика, должны иметь защитные колпаки из небьющегося стекла.
7.30. При работе с добавками (ускорителями сроков схватывания бетонной смеси) следует соблюдать правила работы с едкими веществами. Вблизи мест, где производятся работы”. должен находиться бак с чистой водой и специальные нейтрализующие растворы для оказания первой помощи.
Приложение 1
Рекомендуемое
РЕКОМЕНДАЦИИ ПО ПРЕДВАРИТЕЛЬНОМУ ВЫБОРУ КОНСТРУКЦИИ КРЕПИ
Предварительно конструкцию крепи выбирают, исходя из вида грунтового массива, его устойчивости и склонности грунта выработки к размоканию (табл. 1).
Таблица 1
| | | | | | | | | | | | | | | | | | | | | | |
|
Вид грунтового массива |
|
Скальный с категорией устойчивости1
с учетом обводненности |
Глинистый с оценкой
устойчивости2 |
Глинисто-песчаный без |
Конструкция крепи |
I |
II |
III |
IV |
V |
|
неустойчивый |
оценки устойчивости |
|
|
|
|
|
|
устойчивый |
неразмокаемый |
размокаемый |
с |
в |
|
с |
в |
с |
в |
с |
в |
с |
в |
с/в |
|
|
с |
в |
|
|
Анкерная:
отдельные анкеры |
Р |
Р |
Д |
Д |
Н |
Н |
Н |
Н |
П
р |
Н |
Н |
Н |
Н |
Н |
Н |
система анкеров |
Д |
Д |
Р |
Р |
Д |
Н |
Н |
Н |
и |
Н |
Н |
Н |
Н |
Н |
Н |
Набрызгбетонная, покрытие:
простое |
Р |
Д |
Н |
Н |
Н |
Н |
Н |
Н |
м
е
н |
Д |
Н |
Н |
Н |
Н |
Н |
простое |
Д |
Д |
Д |
Д |
Р |
Д |
Н |
Н |
е |
Р |
Д |
Н |
Н |
Н |
Н |
сложное |
Д |
Д |
Р |
Р |
Р |
Д |
Н |
Н |
н |
Н |
Р |
Р |
Д |
Н |
Н |
Арочная:
без затяжки |
Н |
Н |
Н |
Н |
Н |
Н |
Н |
Н |
и
е |
Д |
Н |
Н |
Н |
Н |
Н |
с затяжкой:
местами |
Н |
Н |
Д |
Д |
Н |
Н |
Н |
Н |
с |
Д |
Д |
Н |
Н |
Н |
Н |
сплошь |
Н |
Н |
Д |
Р |
Р |
Д |
Н |
Н |
п |
Д |
Р |
Д |
Д |
Д |
Д |
Комбинированная:
набрызгбетон с
анкерами:
точечными без
подхватов |
Д |
Д |
Р |
Р |
Д |
Д |
Н |
Н |
е
ц
п
р |
Н |
Н |
Н |
Н |
Н |
Н |
точечными с
подхватами |
Н |
Н |
Д |
Д |
Р |
Д |
Н |
Н |
о
х |
Н |
Н |
Н |
Н |
Н |
Н |
с распределен-ными |
Н |
Н |
Д |
Д |
Р |
Д |
Н |
Н |
о
д |
Р |
Д |
Н |
Н |
Н |
Н |
набрызгбетон с арками:
без затяжки |
Н |
Н |
Д |
Д |
Д |
Н |
Н |
Н |
к
и
|
Д |
Н |
Н |
Н |
Н |
Н |
с затяжкой |
Н |
Н |
Д |
Д |
Р |
Р |
Р |
Р |
|
Д |
Р |
Р |
Р |
Р |
Р |
_________
1 Категория устойчивости скального грунта—по приведенной ниже методике.
2 Устойчивый—с допустимым временем стояния неукрепленной выработки более 1 мес.; неустойчивый—менее 1 мес.
р—тип крепи, рекомендуемый к применению; д—то же допускаемый к применению; н—то же не рекомендуемый к применению; с—массив сухой или влажный; в—то же существенно обводненный.
Методика оценки устойчивости неподкрепленной выработки в скальном массиве
Методика позволяет получать относительные оценки устойчивости, которые подлежат корректировке по результатам наблюдений за состоянием выработки при проходке и креплении.
Методика определяет зависимость предельного (допустимого) времени tпр, сут, снабжения пород в зависимости от характеристической прочности S, МПа, массива в виде
tпр = KS,
где К—коэффициент ответственности прогноза, сут/МПа, K=20 сут/МПа(для нормального прогноза; 10 сут/МПа—для особо ответственного прогноза.
Характеристическую прочность грунта “в массиве” находят по формуле:
S=1,07 Rc k1 k2 k3 k4 k5 k6 k7
где 1,07—нормирующий множитель; Rc—временное сопротивление образца грунта одноосному сжатию (прочность “в куске”), МПа; k1 . . . k7—безразмерные коэффициенты (нормированные к 1), обеспечивающие переход от прочности грунта “в куске” к прочности “в массиве” приведены ниже.
Учет ориентации выработки по отношению к наиболее развитой (опасной) системе трещин
k1
Ориентация благоприятная (90°—70°) ................ 1
Ориентация неблагоприятная (70°—20°) .............. 0,667
Ориентация крайне неблагоприятная (20°—0°) ......... 0,5
Учет расчлененности массива трещинами
k2
Одиночные случайные трещины ..................... 1—0,5
Одна система трещин .............................. 0,25
То же и слоистость ................................ 0,167
Две системы трещин ............................... 0,125
То же и слоистость ................................ 0,083
Три системы трещин ............................... 0,056
То же и слоистость ................................ 0,042
Четыре системы трещин ............................ 0,033
Раздробленный массив ............................. 0,025
Учет интенсивности сетки трещин в породах
k3
Нетрещиноватые, n<6 .............................. 1—0,90
Слаботрещиноватые, п=6—12 ....................... 0,95—0,75
Трещиноватые, n=12—25 ........................... 0,75—0,5
Сильнотрещиноватые, n=25—60 ..................... 0,50—0,25
Раздробленные, n>60 ............................... 0,25—0,05
п—модуль относительной трещиноватости массива n=B/bt,
где В—пролет выработки, м; bt—среднее расстояние между
трещинами, м.
Учет сопротивления отдельностей смещениям по поверхности трещин
k4
Прерывистые трещины ............................. 1
Волнистые трещины:
неровные ....................................... 0,75
ровные ......................................... 0,50
зеркальные ..................................... 0,375
Плоские трещины, ровные, заполненные породой........... 0,25
Зеркала скольжения................................ 0,125
Учет ширины раскрытия трещин, мм, без учета их заполнения
k5
До 3 ............................................ 1
От 3 до 15 ....................................... 0,5
15 и более ....................................... 0,25
Учет заполнения трещин в зависимости от заполнителя
k6
При наличии контакта стенок трещин:
песок, упрочненная порода ........................ 1—0,75
песок, измельченная порода (без глины) .............. 0,375
глина ........................................ 0,25
каолинит, слюда, тальк, графит .................... 0,188
При отсутствии контакта стенок трещин:
песчано-глинистый .............................. 0,15
глина в зависимости от ширины раскрытия
трещин ...................................... 0,125—0,0375
Учет степени обводненности выработки
k7
Сухо ............................................ 1
Влажно .......................................... 0,8
Капеж ........................................... 0,5
Струи ........................................... 0,3
При учете интенсивности сетки трещин следует принимать во внимание, что при взрывной разработке забоя возможно увеличение первоначальной (бытовой) трещиноватости массива вокруг выработки, что можно оценить по эмпирической формуле
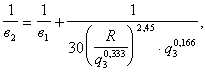
где в1—среднее расстояние между трещинами при изыскательских работах; в2—то же после взрывания забоя; R—расстояние от центра заряда до оцениваемой зоны, м; q3—масса тротилового заряда, кг.
Пример 1
S = 1,1 ( 30 ( 0,667 ( 0,042 ( 0,40 ( 0,25 ( 0,5 ( 0,375 ( 0,3 = 0,0052 МПа;
tпр = 20 ( 0,0052 = 0,104 сут = 2,52 ч.
Порода весьма неустойчива, пересчитываем, принимая значение К для условий повышенной опасности:
ч.
Вывод: Обнажение может обрушиться почти сразу вслед за разработкой (наиболее сильное влияние k2 = 0,042).
Пример 2. В условиях примера 1 принимаем решение—омоноличивание массива путем применения химического закрепления грунта.
S = 1,1 ( 30 ( 0,667 ( 0,056 ( 0,90 ( 1 ( 1 ( 0,75 ( 0,8 = 0,666 МПа
tпр = 20 ( 0,666 = 13,3 сут.
Вывод: Химическим закреплением грунта достигается существенное повышение устойчивости выработки.
Допустимое время обнажения увеличилось с 1,26 ч до 13,3 сут. Возможна проходка при условии крепления выработки лишь в отдельных местах.
Категорию устойчивости грунта скального массива определяют в соответствии с табл. 2.
Таблица 2
Характеристическая прочность грунта |
Устойчивость массива |
“в массиве”, МПа |
Категория |
Характеристика |
tпр, сут. |
>9 |
I |
Вполне устойчивый |
Практически неограничено |
9—1,5 |
II |
Устойчивый |
180—30
(6—1 мес.) |
1,5—0,35 |
III |
Средней устойчивости |
30—7 |
0,35—0,05 |
IV |
Слабоустойчивый |
7—1 |
<0,05 |
V |
Неустойчивый |
1 |
Приложение 2
Справочное
КЛАССИФИКАЦИЯ ГРУНТОВ ПО М. М. ПРОТОДЬЯКОНОВУ
Таблица 1
Грунты |
Коэффициент крепости, f |
Плотность
(, т/м3 |
Наиболее крепкие плотные и вязкие кварциты и базальты, исключающие по крепости другие породы |
20 |
2,8—3 |
Очень крепкие гранитовые породы, кварцевый порфир, очень крепкий гранит, кремнистый сланец; менее крепкие, чем указанные выше, кварциты, самые крепкие песчаники и известняки |
15 |
2,6—2,7 |
Гранит (плотный) и гранитовые породы, очень крепкие песчаники и известняки, кварцевые рудные жилы, крепкий конгломерат, очень крепкие железные руды |
10 |
2,5—2,6 |
Известняки (крепкие), некрепкий гранит, крепкие песчаники, крепкий мрамор, доломит, колчеданы |
8 |
2,5 |
Обыкновенный песчаник, железные руды |
6 |
2,4 |
Песчанистые сланцы, сланцеватые песчаники |
5 |
2,5 |
Крепкий глинистый сланец, некрепкий песчаник и известняк, мягкий конгломерат |
4 |
2,8 |
Разнообразные сланцы (некрепкие), плотный мергель |
3 |
2,5 |
Мягкий сланец, мягкий известняк, мел, каменная соль, гипс, мерзлый грунт, антрацит, обыкновенный мергель, разрушенный песчаник, сцементированная галька и хрящ, каменистый грунт |
2 |
2,4 |
Щебенистый грунт, разрушенный сланец, слежавшиеся галька и щебень, крепкий каменный уголь, отвердевшая глина |
1,5 |
1,8—2 |
Глина (плотная), средний каменный уголь, крепкий насос, глинистый грунт |
1 |
1,8 |
Легкая песчанистая глина, лёсс, гравий, мягкий уголь |
0,8 |
1,6 |
Растительный грунт, торф, легкий суглинок, сырой песок |
0,6 |
1,5 |
Песок, осыпи, мелкий гравий, насыпной грунт, добытый уголь |
0,5 |
1,7 |
Плывуны, болотистый грунт, разжиженный лёсс и другие разжиженные грунты |
0,3 |
1,5—1,8 |
Таблица 2
Трещиноватость скального массива по классификации межведомственной комиссии по взрывному делу
Категория трещиноватости |
Степень трещиноватости (блочности) массива |
Среднее расстояние между |
Удельная трещиноватость, м |
Содержание, %, в массиве отдельностей, мм |
|
|
трещинами, м |
|
300 |
700 |
1000 |
I |
Чрезвычайно трещиноватый (мелкоблочный) |
До 0,1 |
10 |
До 10 |
0 |
Нет |
II |
Сильнотрещиноватый (среднеблочный) |
0,1—0,5 |
2—10 |
10—70 |
До 30 |
До 5 |
III |
Среднетрещиноватый (крупноблочный) |
0,5—1 |
1-2 |
70—100 |
30—80 |
5—40 |
IV |
Мелкотрещиноватый (весьма крупноблочный) |
1,0—1,5 |
1,0—0,65 |
100 |
80—100 |
40(100 |
V |
Практически монолитный |
Свыше 1,5 |
0,65 |
100 |
100 |
100 |
Приложение 3
Рекомендуемое
МЕТОДИКА РАСЧЕТА ПАРАМЕТРОВ КОНТУРНОГО ВЗРЫВАНИЯ И УСТРАНЕНИЯ СВЕРХНОРМАТИВНОЙ ШЕРОХОВАТОСТИ ПОВЕРХНОСТИ ПОРОДЫ ПРИ ПРОХОДКЕ ТОННЕЛЕЙ
Расчет параметров контурного взрывания
Контурным взрыванием при проходке тоннелей и других горных выработок решается две задачи:
обеспечение максимального соответствия фактической площади сечения тоннеля проектной (снижение переборов) для снижения расходов бетона на возведение крепи;
снижение нарушений (трещиноватости и шероховатости) в приконтурной части массива для повышения его несущей способности.
Основные требования при производстве контурного взрывания:
вынос проектной линии контура на “грудь” забоя;
расположение контурных шпуров на проектной линии, а их бурение производить с минимальным (постоянным) углом наклона к продольной оси тоннеля;
заряжание шпуров специальными зарядами из низкоэнергетических типов ВВ с отношением диаметра шпура к диаметру заряда не менее 2;
одновременное инициирование зарядов в контурных шпурах;
обеспечение контроля за состоянием поверхности контура тоннеля и оперативное изменение режимов БВР при изменении горно-геологических условий.
Применяют два вида контурного взрывания—предварительное щелеобразование и последующее оконтуривание (метод контурной отбойки). В их основу положен метод сближенных зарядов, при котором расстояние между контурными шпурами не превышает 0,3—0,5 м. Низкоэнергетические заряды должны при этом обеспечивать разрушение массива между шпурами.
Для уменьшения объема буровых работ при применении контурного взрывания рекомендуется в скальных массивах с категорией трещиноватости 2—5 применять контурное взрывание на основе шпуров с надрезами, а в массивах с меньшей категорией трещиноватости—метод сближенных зарядов.
Наилучшие результаты от контурного взрывания достигаются при выполнении условия
(1)
где а—расстояние между шпурами, м, В—линия наименьшего сопротивления (л.н.с.), м.
Удельный расход ВВ при контурном взрываний определяется из условия разрушения объема грунта взрывом заряда контурных шпуров и соответствует нормам, установленным СНиП IV-2—82, сб. 29 “Тоннели и метрополитены”.
При взрываний методом сближенных зарядов расчет параметров БВР следует выполнять в соответствии с “Рекомендациями по производству БВР с применением механизированного заряжания и гидрозабойки при проходке транспортных тоннелей”, М., ЦНИИС, 1980.
При применении технологии контурного взрывания на основе шпуров с надрезами удельный расход ВВ q определяют по формуле:
(2)
где q0—удельный расход ВВ для заданных условий проходки, кг/м3, определяемый или по существующим формулам, или по СНиП IV-2—82, сб. 29 “Тоннели и метрополитены”, Кэ—коэффициент снижения энергоемкости разрушения, определяемый из условия:
Кэ = 0,8335 + 0,0336f—0,0015f2—0,1014H + 0,0037H2 + 0,0018Hf, (3)
где f—коэффициент крепости породы по М. М. Протодьяконову (см. приложение 2); Н—средняя глубина надреза, мм.
Последовательность расчета паспорта БВР при контурном взрываний на основе шпуров с надрезами (метод последующего оконтуривания) следующая:
1. Определяют удельный расход ВВ для заданных условий проходки тоннеля по СНиП IV-2—82, сб. 29 “Тоннели и метрополитены”.
2. Определяют по формуле (3) значение коэффициента Кэ, а по формуле (2)—удельный расход ВВ для шпуров с надрезами.
3. Задаются расстоянием а между контурными шпурами и из условия (1) определяют л.н.с.
4. Находят общую массу Q заряда для контурных шпуров по формуле
(4)
где l—глубина шпуров, м; П—периметр поперечного сечения тоннеля (кроме подошвы), м.
5. Определяют число контурных шпуров Nк по формуле:
шт. (5)
6. Находят массу шпуров заряда ВВ по формуле
кг. (6)
7. Проводят уточненный расчет расстояния aк между контурными шпурами по формуле
м, (7)
где r—радиус заряда, м; n—коэффициент затухания волн в скальном грунте (обычно, для зоны дробления п=2, для зон единичных трещин n==1,5); [(]р—динамический предел прочности грунта на растяжения, кПа (для большинства скальных грунтов ); Н и (—соответственно, сумма глубины надреза и радиуса шпура или радиус закругления вершины надреза ((=0,001 м); Р—усредненное давление взрыва в шпуре, кПа, которые можно принять Р(Ед или определить из упрощенной формулы:
кПа, (8)
где Qшп и Е—соответственно, масса ВВ в шпуре и теплота его взрыва, кг и кДж/кг (таблица); V— объем шпура, заполненного зарядом, м3; (— показатель изоэнтропы ВВ (для промышленных ВВ ((3).
8. Определяют количество остальных шпуров (врубовых, подошвенных, отбойных и т. д.), а также расстояние между ними и массу зарядов по существующим методикам.
Проведением двух-пяти опытных взрывов уточняют параметры БВР, рассчитанные по формулам (1—8) и при необходимости их корректируют.
Критерием качества поверхности стенок горной выработки при применении контурного взрывания является допустимая ее шероховатость, которую измеряют фактическим отношением Yф суммарной длины отпечатков (следов) шпуров на поверхности выработки к суммарной длине всех контурных шпуров и фактической линейной величиной неровностей (выступов и впадин) между отпечатками шпуров, т. е.
,% (9)
см, (10)
где Lc—сумма длин отпечатков шпуров на поверхности, определяемая маркшейдерскими измерениями, м; Lш—длина контурных шпуров (кроме подошвенных), м; (—к.и.ш. шпуров (((0,9—0,95); —линейная величина (средняя) неровностей поверхностей, определяемая маркшейдерскими измерениями, см; Y и hк— нормативные значения показателей шероховатости контура, определяемые в соответствии с п. 2.6 настоящих Норм.
Устранение сверхнормативной шероховатости контура тоннеля
Правильное применение технологии контурного взрывания при соблюдении технологической дисциплины обеспечивает требуемое качество поверхности контура тоннеля.
Нормативные значения характеристик шероховатости контура определяют для конкретных условий проходки. Соответствие фактических величин характеристик шероховатости нормативным устанавливают маркшейдерскими измерениями и в случае несоответствия корректируют режимы БВР.
Сверхнормативная шероховатость поверхности выработки может появиться при резком падении инженерно-геологических условий проходки а также при превышении углов забуривания контурных шпуров.
В данных ситуациях требуются дополнительные затраты труда материалов и времени на устранение неровностей путем заполнения локальных впадин черновым слоем набрызгбетона. Последующие (расчетные) слои набрызгбетона наносят на поверхность контура и на слой чернового набрызгбетона.
Характеристика некоторых ВВ, применяемых на подземных горных работах
Тип ВВ, ГОСТ |
Теплота взрыва, кДж/кг |
Объем газов взрыва,
л/кг |
Скорость детонации, км/с |
Гранулит АС-8 ГОСТ 21987—76 |
5191 |
847 |
3,0—3,6 |
Аммонит скальный № 1 ГОСТ 21985—76 |
5400 |
830 |
6,0(6,5 |
Детонит М ГОСТ 21986—76 |
5786 |
832 |
4,9—5,3 |
Аммонит 6ЖВ ГОСТ 21984—76 |
4305 |
895 |
3,6—4,8 |
Аммонит ПЖВ-20 ГОСТ 21982—76 |
3404 |
717 |
3,5—4,0 |
Угленит Э-6 ГОСТ 21983—76 |
2680 |
560 |
1,9—2,2 |
Приложение 4
Рекомендуемое
ОСНОВНЫЕ ХАРАКТЕРИСТИКИ ВЯЖУЩИХ, ПРИМЕНЯЕМЫХ ДЛЯ НАБРЫЗГБЕТОНИРОВАНИЯ
| | | | | | | | | | | | | | | | |
Вид цемента |
В/Ц |
Сроки схватывания, мин |
Предел прочности на сжатие, МПа, раствора в возрасте |
|
|
нача-ло |
окончание |
2ч |
1 сут |
3 сут |
7 сут |
14 сут |
28 сут |
Напрягающий цемент (НЦ) |
0,31 |
4 |
6,5 |
( |
40,8 |
( |
( |
( |
65,0 |
Водонепроницаемый расширяющийся цемент |
0,36 |
5 |
8 |
— |
10,5 |
— |
— |
27,3 |
— |
Пуццолано-белитовый раствор:
низкоалюминатный |
0,31 |
8,5 |
9 |
( |
1,75 |
2,4 |
3,1 |
9,3 |
16,2 |
высокоалюминатный |
0,31 |
2,3 |
5 |
— |
3,5 |
5,5 |
6,9 |
19,0 |
22,0 |
Пуццолано-алитовый раствор:
низкоалюминатный |
0,31 |
4 |
8 |
( |
2,1 |
8,4 |
16,5 |
25,5 |
37,0 |
высокоалюминатный |
0,31 |
3 |
5 |
— |
2,9 |
10,8 |
24,6 |
24,2 |
38,1 |
Водонепроницаемый безусадочный |
0,31 |
3 |
5 |
5,0 |
— |
25,0 |
— |
— |
30,0 |
Набрызгцемент Днепродзержинского завода |
0,4 |
5 |
10 |
2,3 |
5,1 |
24,1 |
— |
— |
50,9 |
Быстросхватывающийся безусадочный Нижне-Салдинского завода |
0,4 |
6 |
8 |
2,0 |
4,9 |
— |
— |
— |
37,0 |
Быстросхватывающийся “быстряк” Криворожского завода |
0,4 |
3 |
5 |
1,5 |
2,7 |
16,1 |
25,3 |
— |
45,6 |
Быстросхватывающийся “быстряк” Усть-Каменогорского
завода |
0,4 |
1,5 |
3,5 |
0,3 |
1,4 |
10,4 |
15,7 |
— |
23,3 |
Быстросхватывающийся быстротвердеющий бесалит Подольского завода НИИцемент |
0,3 |
15 |
20 |
14,9 |
30,4 |
(
|
31,1 |
( |
40,2 |
Глиноземистый цемент |
0,4 |
5 |
10 |
— |
10-15 |
30-35 |
— |
— |
50 |
Приложение 5
Рекомендуемое
ВИДЫ И ХАРАКТЕРИСТИКА ДОБАВОК
Вид добавки |
Количество, % от массы цемента,
плотность (, г/см3 |
Вид вяжущего |
Назначение |
При наличии агрессивных сред |
Na2S04+K2C03 при соотношении 5:3 |
2 |
Любой портландцемент (п/ц) |
Ускоритель, не уменьшающий стойкости бетона в агрессивных средах |
Fe(МО3)3+Са(КО3)2 |
2
3(10+3(10 |
То же |
Повышает прочность сцепле-ния, улучшает состав и структуру контактного слоя, повышает долговечность кон-такта даже при действии минерализованных вод. Бетон повышенной водонепроница-емости и коррозионной стой-кости, быстро схватывается и твердеет |
Любой ускоритель схватывания |
— |
Сульфато-стойкий п/ц М500 |
Повышает стойкость бетона при наличии агрессивных вод по SO4 |
Na2SO4
K2SO4
CaSO4 2H2O
Fе2(SO4)3 |
1(4
1(6
2(5
1(5 |
Пуццолановый или шлаковый п/ц |
Повышает стойкость бетона при наличии агрессивных вод по SO4 |
Ca(NO2)2+Ca(NO3)2 |
1(5 |
Любой п/ц |
Повышает стойкость в агрес-сивной среде, повышает водо-непроницаемость и морозо-стойкость |
Для обводненных грунтов с водопритоком, по всей поверхности |
NaAlO2 |
2(5 |
Любой п/ц |
Повышает сопротивляемость размыву свежих растворов и бетонов и уменьшает их водонепроницаемость. Уменьшает адгезию набрызг-бетона, несколько увеличивает усадку, возможно повышение водопроницаемости в возрасте 1—6 месяцев в 3—4 раза и снижение конечной прочности |
ОЭС |
2(5 |
” |
Повышает сопротивляемость размыву при водопритоке до 2 л/(мин(м). Возможно снижение конечной прочности бетона, увеличение усадки, повышение водопроницаемости бетона в возрасте 1—6 мес. в 3—4 раза |
Жидкое стекло (ЖС) |
( =1,18—1,21 |
” |
Повышает сопротивляемость размыву при водопритоке до 5 л/(мин(м). Увеличивает усадку, замедляет рост прочности (в большом количестве снижает прочность набрызгбетона и сцепление с породой) |
ЖС (Na2O(SiO2) + “Альфа” |
( =1,19—1,21+ +0,2—0,9 |
”
|
Повышает сопротивляемость размыву до 8—10 л/(мин(м) и более. Возможно применение при пониженной температуре грунта и воздуха |
ЖС+Оксикарбоновая кислота |
( =1,19—1,21+ +0,005—0,010 |
” |
То же |
CaCl2+FeCI3
соотношение определяется опытным путем |
5(9 |
” |
Повышает сопротивляемость размыву при водопритоке до 8—10 л/(мин(м) и более. Возможно применение при пониженной температуре грун-та и воздуха |
СаСl2+ОЭС |
4(5+2(3 |
” |
То же |
А1С13 |
1—5 |
”
|
Повышает сопротивление размыву. Для алитовых цемен-тов повышает односуточную прочность в 1,5 раза, 28-суточная прочность такая же, как и для бетона без добавки |
НКА-1, НКА-2 (NаАlO2+K3СО3)
1:0,6 |
2(6 |
” |
Повышает сопротивление размыву при водопритоке до 3 л/(мин(м) |
NaAlO2+K2CO3+Na2SO4 |
2+0,5—1
1—4 |
” |
Повышает сопротивление размыву при водопритоке до 3 л/(мин(м) |
ОЭС+NaF |
2+0,5(1 |
” |
Токсичен |
NaF |
1—4 |
” |
|
Для мерзлых грунтов |
NaCl
СаСl2
К2СО3 |
1—3
2(5
1—10 |
П/ц с умеренной экзотермией при C3S(55%
С3А(6% |
Не дает снижения прочности в 28-суточном возрасте, но вызывает коррозию арматуры, способствует интенсивному нарастанию прочности при схватывании за счет выделения тепла при его растворении |
Ca(NO3)2 Ca(NO3)2+Ca(NO2)2 |
1(6 |
То же |
Эффективная противоморозная добавка, повышает водо-непроницаемость, увеличивает стойкость в агрессивной среде, не влияет на морозостойкость |
Приложение 6
Обязательное
ТРЕБОВАНИЯ К ФИЗИКО-МЕХАНИЧЕСКИМ ХАРАКТЕРИСТИКАМ НАБРЫЗГБЕТОНА В ЗАВИСИМОСТИ ОТ ХАРАКТЕРИСТИК ГРУНТОВ
| | | | | | | | | | | | | | | |
№ |
Характеристики грувтов |
Возможвая продолжительность |
Требуемая прочность набрызгбетона на сжатие, МПа |
Требуемые сроки схватывания вяжущего для набрызгбетона технологи- |
пп |
|
обнажения грунта выработки без |
технологической крепя в возрасте |
обделки |
ческой крепя, мин. |
|
|
крепления |
1 ч |
6 ч |
1 сут |
7 сут |
28 сут |
1 сут |
28 сут |
|
1 |
Устойчивые, монолитные, крепкие или очень крепкие, не оказывающие горного давления |
Практически постоянно |
— |
— |
— |
— |
— |
5(10 |
30 |
— |
2 |
Крепкие, слаботрещиноватые, выветривающиеся, склонные к вывалообразованию |
Несколько месяцев |
( |
( |
( |
( |
( |
8(12 |
30 |
— |
3 |
Средней крепости, слаботрещиноватые, склонные к вывалообразованию |
Несколько суток |
— |
2 |
10—15 |
— |
30 |
— |
30 |
Начало схватывания—30; конец схватывания—60 |
4 |
Средней крепости, слаботрещиноватые, оказывающие небольшое давление |
Несколько часов |
0,5—1 |
5(8 |
10(15 |
20 |
30 |
— |
30 |
Начало схватывания—10; конец схватывания—30 |
5 |
Средней крепости, сильнотрещиноватые, оказывающие значительное горное давление |
Несколько минут |
1—2 |
5(8 |
15—20 |
( |
30—40 |
8—10 |
30 |
Начало схватывания—10; конец схватывания— 80 с |
6 |
Мерзлые устойчивые грунты |
Несколько месяцев |
— |
— |
5—6 |
— |
20—30 |
— |
30 |
— |
7 |
Мерзлые грунты средяей крепости |
От нескольких суток до нескольких мес. |
— |
— |
6—10 |
20 |
30 |
— |
30 |
( |
8 |
Водоприток 1—3 л/(мин(м) |
— |
0,7-1 |
— |
10 |
— |
30 |
— |
30 |
Начало схватывания—1; конец схватывания—2 |
9 |
Водоприток более 3 л/(мин(м) |
— |
0,7-1 |
( |
10 |
( |
30 |
(
|
30 |
Начало схватывания—15 с; конец схватывания—40 с |
Примечание. Способ нанесения набрызгбетона и требования к вяжущему определяются в зависимости от характера обводнённой поверхности по рекомендуемому приложению 13. Вид вяжущего выбирается по рекомендуемому приложению 4.
Приложение 7
Рекомендуемое
МЕТОДИКА ПОДБОРА СОСТАВА СУХОЙ СМЕСИ, ОПРЕДЕЛЕНИЯ РЕЖИМА НАНЕСЕНИЯ, РАСХОДА МАТЕРИАЛОВ ДЛЯ ПОЛУЧЕНИЯ 1 м3 НАБРЫЗГБЕТОНА
1. Определение характеристик материалов:
цемента—активность цемента Ац и нормальная густота цементного теста (н.г.ц.т) (в соответствии с ГОСТ 310.4—81 и ГОСТ 310.3—76);
песка—плотность (п; насыпная плотность (нас.п ; модуль крупности Мк ГОСТ 8735—75) и содержание пыли, глины и ила;
щебня—плотность (щ; насыпная плотность (нас,щ; содержание пыли, глины и ила, т. е. фракции, проходящей через сито № 014; гранулометрический состав щебня должен отвечать составу, представленному в п. 3.13 настоящих Норм.
Максимальную крупность заполнителя следует назначать в соответствии с требованием п. 3.13.
2. Определение производственного коэффициента К в зависимости от производственных условий (табл. 1).
Таблица 1
| | | | | | | | | | | | | | | |
№
пп |
Уровень производства |
Коэффициент
вариации Vп, % |
Производственный коэффициент К. |
1 |
Высокий |
12—8 |
0,96—1 |
2 |
Средний |
13 |
0,95 |
3 |
Низкий |
17—14 |
0,90—0,94 |
3. Уточнение производительности набрызгбетом-машины Пнб, м3/ч; длина материального шланга Lш, м; диаметр шланга dш, мм.
4. Определение требований к набрызгбетону; класс по прочности на сжатие В, марка по морозостойкости F, марка по водонепроницаемости W.
5. Предварительное определение водоцементного отношения по формуле
, (1)
где А—коэффициент, учитывающий качество заполнителей (табл. 2);
(2)
Здесь —марочная требуемая прочность; К—производственный коэффициент (см. табл. 1); Rp—расчетная прочность набрызгбетона.
Таблица 2
| | | |
Суммарное содержание пыли и ила, % (в |
Значение коэффициента А для бетона на |
навеске щебня 2 кг, песка 2 кг) |
щебне |
гравии горном |
гравии речном и морском |
0 |
0,64 |
0,60 |
0,57 |
0,75 |
0,61 |
0,56 |
0,54 |
1,5 |
0,58 |
0,53 |
0,51 |
2,25 |
0,55 |
0,5 |
0,48 |
3 |
0,52 |
0,47 |
0,45 |
Таблица 3
| | | |
Марка по водонепроницаемости |
Марка по морозостойкости |
Предельное максимальное В/Ц |
W2 |
— |
0,7 |
W4 |
F 100 |
0,6 |
W6 |
F 200
F 300 |
0,55
0,5 |
W8 |
F 400 |
0,45 |
W12 |
F 500 |
0,4 |
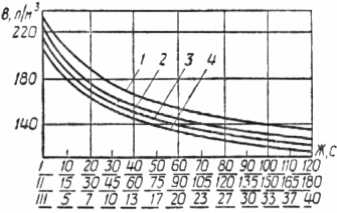
Рис. 1. График расхода воды на 1 м3 бетонной смеси
в зависимости от жесткости бетонной смеси:
I, II, III—определение жесткости соответственно
по техническому вискозиметру; по упрощенному способу,
по ГОСТ 10181—76; 1—для песка; 2—4—для щебня
соответственно HK1O, НK15, НК20
6. Уточнение водоцементного отношения, исходя из условий службы бетона марки по морозостойкости и водонепроницаемости (табл. 3).
7. Определение расхода воды в зависимости от крупности заполнителя и жесткости набрызгбетонной смеси по рис. 1.
8. Уточнение расхода воды в зависимости от вида применяемых материалов (табл. 4).
(3)
Таблица 4
| | | |
Материал |
Изменение расхода воды , л/м3 |
Дополнительные указания |
|
увеличение |
уменьшение |
|
Щебень из метаморфических осадочных пород |
4(13 |
(
|
4 л/м3 при прочности камня 80 МПа, 13 л/м3— при прочности 40 МПа (для нужной прочности поправки определяются по интерполяции) |
Гравий:
горный
морской и речной |
—
( |
5—10
9—15 |
Меньшие значения — при средней окатанности зерен, большие — при хорошо скатанной поверхности зерен |
Щебень из пород камня с гладкой поверхностью излома (диабаз, базальт, кварцитовый песчаник и др.) |
(
|
3 |
(
|
Промытый щебень |
— |
6 |
— |
Щебень при увеличении содержания в щебне ила, пыли (сверх 1%) и частиц меньше 5 мм (сверх 5%) на каждый процент сверх нормы |
1—2 |
(
|
1 л—при содержании частиц меньше 5 мм; 2 л—при содержании только ила и пыли |
Песок с гладкой, хорошо скатанной поверхностью типа Вольского |
— |
4 |
(
|
Песок с модулем крупности, отличным от 3:
в меньшую сторону
в большую сторону |
3; 4; 5
( |
(
3; 4; 5 |
Изменения расхода воды, равные 3, 4 и 5 л/м3, соответствуют содержанию пыли, ила и глины 1, 3 и 5% |
Промытый песок при увеличении содержания в песке ила, пыли (но не глины) на каждый процент сверх 3% |
2 |
( |
( |
Цемент с нормальной густотой цементного теста НГЦТ, отличной от 28%:
в большую сторону |
4 |
( |
( |
в меньшую сторону |
— |
4 |
— |
Бетонная смесь при температуре, "С:
5 |
( |
5 |
( |
10 |
— |
4 |
( |
15 |
— |
2 |
( |
20 |
— |
— |
Эталон |
25 |
3 |
— |
( |
30 |
7 |
— |
( |
35 |
11 |
— |
— |
9. Определение расхода цемента на 1 м3 набрызгбетона:
. (4)
10. Определение расхода цемента на 1 м3 сухой смеси по формуле:
, (5)
где Купл= 1,2— коэффициент уплотнения при набрызгбетонировании.
11. Определение соотношения между песком и щебнем (доля песка в смеси заполнителей r) в зависимости от марки цемента, модуля крупности песка Мк и необходимой прочности набрызгбетона (с учетом коэффициента производственных условий К) по рис. 2.
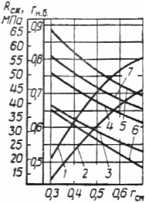
Рис. 2. Зависимости предела прочности набрызгбетона на сжатие
Rсж и доли песка в заполнителях уложенного набрызгбетона
от доли песка в заполнителях исходной смеси:
1 ( rнб без химических добавок; 2 ( rнб с химическими ускорителями схватывания; 3 ( Rсж для Мц 300 и Мк =3; 4 ( Rсж для Мц 400 и Мк=3; 5 ( Rсж для Мц 500 и Мк=3; 6 ( Rсж для Мц 400 и Мк=2; 7 ( Rсж для Мц 400 и Мк=3,4. Мк( модуль крупности песка
12. Определение расхода песка на 1 м3 сухой смеси по формуле
Псм = ((см — Цсм)r см, (6)
где (cм — насыпная плотность смеси, равная 1440—1520 кг/м3 (для смеси на гранитном щебне и кварцевом песке) в зависимости от rм (1440 кг/м3 для rсм = 0,7; 1520 кг/м3 — для rсм = 0,3; остальные значения определяются интерполяцией).
13. Определение расхода щебня в 1 м3 сухой смеси но формуле:
Щсм = (см ( Цсм ( Псм, (7)
14. Определение оптимального режима нанесения набрызгбетона (давление в набрызгбетон-машине и расстояние от сопла до бетонируемой поверхности) по п. 3.55.
Расход воздуха для разных типов набрызгбетон-машин при влажности смеси до 10% определяют по рис. 3 и табл. 5.
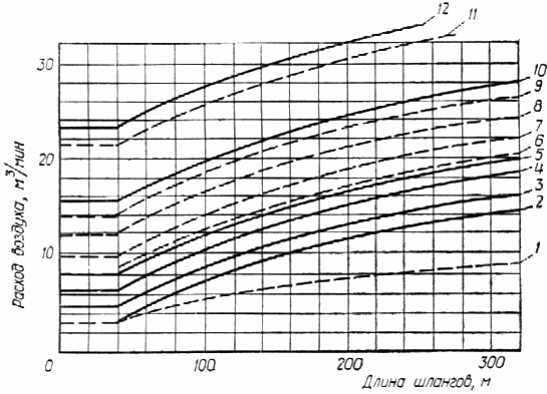
Рис. 3. График зависимости расхода воздуха от длины
и диаметра шлангов набрызгбетон-машины
(см. табл. 5 приложения 7)
15. Назначение расхода поды при подаче насосом в зависимости от водоцементного отношения В/Ц, расхода цемента Цсм , производительности набрызгбетон-машины.
Определение производительности набрызгбетон-машины по цементу , кг/мин:
(8)
Расход воды Всм, л/мин,
(9)
Таблица 5
| | | | |
Производительность, м3ч |
Диаметр материального шланга, мм |
Плотность.
кг/дм3 |
Номер кривой на рис. 3 |
Двигатель |
2 |
32 |
0,6 |
1 |
Э |
2 |
32 |
1,6 |
2 |
Э |
2 |
38 |
1,6 |
3 |
Э |
4 |
50 |
1,6 |
4 |
Э |
5 |
38 |
1,6 |
5 |
Э |
8 |
38 |
0,6 |
6 |
П |
4 |
50 |
1,6 |
7 |
П |
8 |
50 |
1,6 |
8 |
П |
5 |
50 |
1,6 |
9 |
П |
8 |
90 |
1,6 |
10 |
Э |
8 |
90 |
1,6 |
11 |
П |
12 |
110 |
1,6 |
12 |
Э |
Э—электродвигатель; П—пневмодвигатель.
16. Определение количества материалов для получения 1 м3 набрызгбетона по коэффициенту выхода для оценочного расчета стоимости набрызгбетона:
Квых = Купл + Ко, (10)
где Купл=1.2; Ко — коэффициент отскока материала (табл. 6).
Таблица 6
Материал |
Ко при доле песка r в заполнителе |
|
0,3 |
0,5 |
0,7 |
Цемент |
0,04 |
0,07 |
0,08 |
Песок |
0,2 |
0,4 |
0,5 |
Щебень |
0,8 |
0,5 |
0,4 |
Количество материалов в килограммах для получения 1 м3 набрызг-бетона равно:
(11)
(12)
(13)
17. Состав нанесенного набрызгбетона отличается от состава исходной смеси, так как смесь в процессе набрызга уплотняется и частично теряется из за отскока материала.
Для определения ориентировочного состава набрызгбетона по рис. 2 находят rнб—долю песка в заполнителях набрызгбетона. Для этого от заданного значения rсм проводят прямую до r и от точки пересечения опускают перпендикуляр на ординату rнб.
Значение точки на оси rнб соответствует значению доли песка в заполнителях в уложенном набрызгбетоне.
С учетом полученного значения rнб определяют количество составляющих, кг/м3, в набрызгбетоне:
цемента ............. Цнб = Цсм ( 1,7; (14)
воды ............... Внб = Цнб ( ); (15)
песка ............... Пнб = ((нб — Цнб — Внб)rнб; (16)
щебня .............. Щнб = (нб ( Цнб — Внб — Пнб. (17)
(нб определяют опытным путем: делают выломку куска из свежеуложенного набрызгбетона, кусок укладывают в полиэтиленовый пакет, который завязывают и взвешивают, определяют Qнб. Затем опускают в сосуд, до верха наполненный водой, и определяют объем вытесненной воды Vнб. Тогда .
18. Определение сроков схватывания цементного раствора с добавкой для нахождения оптимального количества добавки выполняют на приборе Вика.
Навеска цемента принимается равной 100 г. Цемент тщательно перемешивается с порошкообразной добавкой, количество которой принимается в начале опыта минимальным. В раствор заливается вода в количестве, соответствующем нормальной густоте данного цемента.
Примечания: 1. Нормальная густота цементного теста определяется по стандартной методике.
2. Жидкая добавка — ускорителя схватывания — вводится в смесь вместе с водой.
Минимальное количество добавки в начале опыта принимается равным 2%-й массы цемента. После затворения смесь быстро перемешивается и укладывается в кольца прибора Вика.
Игла доводится до соприкосновения с поверхностью теста, после чего стержень иглы массой 100 г освобождается и игла свободно погружается. За начало схватывания принимается время от начала затворения до того момента, когда игла не доходит до дна на 1 мм. За конец схватывания принимается время, прошедшее от начала затворения до момента, когда игла проникает в раствор не более 1 мм.
Оптимальное количество добавки должно соответствовать времени окончания схватывания не более 3 мин.
После определения оптимального количества добавки производится проверка прочности цементно-песчаного раствора. Прочность определяется на образцах-кубиках размерами 3х3x3 см, приготовленных из цементно-песчаного раствора состава 1 : 3 (цемент: песок по массе). Ввиду того что цементно-песчаный раствор с добавкой быстро схватывается, образцы должны приготовляться из небольших порций смеси. Навески (цемента 50 г, песок 160 г) и добавка перемешиваются в металлической или фарфоровой чаше. Затем в смесь вводится вода в количестве 20(25 см3 что соответствует водоцементному отношению 0,4—0,5.
После перемешивания раствор быстро (до начала схватывания) укладывается в формы на один час, после чего образцы распалубливаются.
Количество образцов назначается из расчета на проведение 5 серий испытаний в возрасте 3 ч, 1, 3, 7 и 28 суток. Одновременно изготавливаются и испытываются контрольные образцы из цементно-песчаного раствора аналогичного состава без добавки.
Прочность образцов с добавкой в возрасте 1, 3, 7 и 28 суток не должна быть ниже прочности контрольных образцов того же состава
Пример. Расчет состава сухой смеси, определение режима нанесения и ориентировочного состава набрызгбетона
Исходные данные. 1. Характеристики материалов: цемента(портландцемент марки 400, ПГЦТ = 28%; песка кварцевого — (п= 2,65; (нас(п = 1,56; = 3,27; содержание пыли 3%, глины и ила 2%; содержание органических примесей — в пределах нормы; щебня (щ =2,66 (нас(щ = 1,38; НКЩ = 15 мм. Гранулометрические составы песка и щебня представлены в табл. 7 и 8.
Таблица 7
| | | | | | |
Наименование остатков на |
Гранулометрическнй состав песка, мм, для сит размерами, мм |
ситах, % от массы |
2,5 |
1,25 |
0,63 |
0,315 |
0,14 |
Поддон |
Частные |
25 |
26 |
19 |
16 |
9 |
5 |
Полные |
25 |
51 |
70 |
86 |
95 |
100 |
Таблица 8
Наименование остатков на |
Гранулометрический состав щебня, мм для сит размерами, мм |
ситах, % от массы |
15 |
10 |
5 |
Поддон |
Частные |
5 |
57 |
37 |
1 |
Полные |
5 |
62 |
99 |
100 |
2. Производственные условия: дозировка материалов — по массе; общая культура производства — низкая; коэффициент вариации Vп=16%; производственный коэффициент К=0,91.
3. Применяемое оборудование: набрызгбетон-машина СБ-67 производительностью 4 M3/4; длина материального шланга 40 м; диаметр шланга 50 мм; камера смешения отнесена от сопла на 4 м; вода подается водяным насосом.
Задание. Подобрать состав набрызгбетона со следующими свойствами: В 22,5 (средняя прочность при коэффициенте вариации Vп=13,5%, =30,4 МПа); F 300; W6 (для вторичной обделки), расчетная толщина (= 15 см.
Решение. 1. Определяем водоцементное отношение по формуле (9), а значение А — по табл. 2.
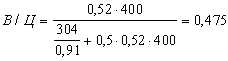
2. Уточняем водоцементное отношение.
Из условий службы бетона по водонепроницаемости В/Ц < 0,55. В зависимости от марки бетона по морозостойкости для F 300 В/Ц < 0,5. Принято наименьшее значение В/Ц = 0,475.
3. Определяем расход воды в зависимости от крупности заполнителя и жесткости набрызгбетонной смеси по рис. 1.
Исходя из того, что оптимальная жесткость набрызгбетонной смеси равна 20 с, крупность щебня 5 — 15 мм, расход воды равен 175 л/м3.
Уточняем расход воды в зависимости от вида применяемых материалов по табл. 4.
л.
Принят расход поды В = 178 л/м3.
4. Определяем расход цемента на 1 м3 набрызгбетона.
кг/м3.
Тогда количество на 1 м3 сухой смеси определяем по формуле (5).
.
5. Определяем соотношение между песком и щебнем (долю песка в смеси заполнителей rсм) в зависимости от марки цемента, модуля крупности песка Мк и необходимой прочности набрызгбетона, а также с учетом коэффициента производственных условий К по рис. 2.
Для МПа, Мц = 400, Мк = 3,27 r = 0,7.
6. Расход песка определяем из условия
Псм = ((cм — Цcм)rсм = (1440—313) ( 0,7=789 кг/м3
7. Количество щебня в смеси будет
Щсм = (см — Цсм — Псм = 338 кг/м3
Исходный состав на 1 м3 сухой смеси, кг/м3:
Цсм = 313; Псм = 789; Щсм = 338.
8. Выбор оптимального режима нанесения набрызгбетона: для материального шланга длиной 40 м и диаметром 50 мм давление в набрызгбетон-машине определяется согласно п. 3.55:
Рмм = 0,1+0,0022 ( 40 + 0,007 ( 2 + 0,04 ( 2 = 0,28 МПа.
Расстояние от сопла до набрызгиваемой поверхности определяется в соответствии с п. 3.56:
(Ц + П) : Щ = (313 + 789) : 338 = 3,26.
Оптимальное расстояние нанесения 0,7 м.
9. Расход воды при подаче насосом при набрызгбетонированин назначается в зависимости от водоцементного отношения, расхода цемента и производи-тельности набрызгбетон-машины. При производительности набрызгбетон-машины П = 4 м3 смеси/ч или 0,067 м3/мин при расходе цемента Цсм = 313 кг/м3 производительность по цементу равна
П = 0,067 ( 313 = 21 кг/мин.
Необходимый расход воды будет
Всм = П = 21 ( 0,475 = 10 л/мин.
10. Определяем расход материалов для получения на 1 м3 набрызг-бетона в килограммах:
= 313 ( 1,28 = 401;
= 789 ( 1,7 = 1341;
= 338 ( 1,4 = 473.
11. Определение ориентировочного состава набрызгбетона:
по рис. 2 определяем изменение состава в процессе набрызгбетонирования: rисх = 0,7; rнб = 0,81.
В набрызгбетоне:
цемента ............... Цнб = 401 ( 1,7=532 кг/м3;
воды ................. Внб = 532 (0,475 — 0,01) = 247 л/м3;
песка ................. Пнб = (2272 ( 532 — 247) ( 0,81 = 1209;
щебня ................ Шнб = 2272 — 532 — 247 — 1209 = 284 кг/м3.
Приложение 8
Рекомендуемое
МЕТОДИКА ПРИГОТОВЛЕНИЯ И ИСПЫТАНИЯ ОБРАЗЦОВ ИЗ НАБРЫЗГБЕТОНА
Набрызгбетонные образцы получают из специально приготовленных плит большого размера.
Плиты изготовляют в деревянных ящиках размерами 50 х 50 х 12 см. Крайние части плиты с нарушенной структурой спиливают, а из средней выпиливают 9 кубиков размерами 10 х 10 х 10 см, используемых для испытания на сжатие, осевое растяжение и морозостойкость. Испытания проводятся в соответствии с ГОСТ 101080—78, ГОСТ 18105—86. Допускается получение образцов из набрызгбетона в виде кернов диаметром 75 — 135 мм, выбуриваемых с помощью станка вращательного бурения с кольцевой коронкой.
Выпиливание и выбуривание образцов производят после того, как набрызгбетон наберет достаточную прочность (7 суток и более).
Для достижения сопоставимости результатов испытаний образцов, размеры или формы которых нестандартны, со стандартными образцами необходимо вводить поправочные коэффициенты, приведенные в таблице.
Вид образцов |
Размер грани или диаметр, см |
Переходный коэффициент |
Кубики |
7 |
0,75 |
|
10 |
0,85 |
|
15 |
0,90 |
|
20 |
1,00 |
|
30 |
1,10 |
Цилиндр (керн) |
h=d |
1,25 |
То же |
h=2d |
1,80 |
Для испытания на водонепроницаемость по ГОСТ 12730,5—84 применяют керны из набрызгбетона диаметром и длиной 15 см.
Возможно проведение испытаний по упрощенной методике с изготовлением образцов из набрызгбетона в виде плит размерами 70 х 40 х 18 см с тремя цилиндрическими полостями диаметром 36 мм. Образец изготовляют в деревянной форме, к днищу которой прикреплены три металлических вкладыша, образующие полости. При испытаниях в полости подается вода через специальные штуцеры. Режим испытаний устанавливают в соответствии с ГОСТ 12730,5—84.
При возведении тоннельных обделок из набрызгбетона для определения качества материала в процессе производства работ рекомендуется определять сцепление набрызгбетона с породой путем отрыва образцов при помощи сетчатой рамки (рис. 1) или прибора конструкции ЛИИЖТа (рис. 2), а в слабых породах—прибора конструкции НИИСПа Госстроя УССР (рис. 3).
При испытаниях с помощью сетчатой рамки (см. рис. 1) образцы изготовляют следующим образом. Па выбранный относительно ровный участок поверхности выработки наносят слой набрызгбетона толщиной 2 — 3 см. В этот слой втапливают сетчатую рамку. Затем наносят слой набрызгбетона толщиной 8 — 10 см. Через 1 — 1,5 ч после этого образец оконтуривают ручным зубилом. Применять для этой цели механизированный инструмент не рекомендуется, так как можно повредить образец.
Отрывая образцы домкратом с использованием опорного приспособления, определяют величину сцепления с учетом особенностей данной поверхности (шероховатости, микротрещиноватости и т. п.). Для более разносторонней оценки величины сцепления производят серию контрольных покрытий набрызгбетоном не на поверхности выработки, а на специально подобранных монолитных блоках породы.
Описанная методика позволяет определить сцепление в любом возрасте набрызгбетона, начиная с нескольких часов после нанесения.
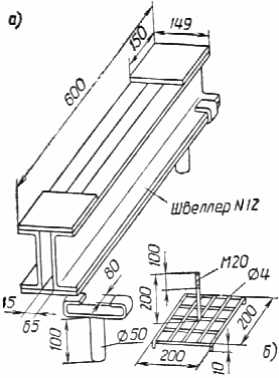
Рис. 1. Приспособление для определения сцепления набрызгбетона:
а—опорное приспособление; б— рамка
Уменьшить трудоемкость испытаний на сцепление в натурных условиях помогает прибор, разработанный в Ленинградском институте инженеров железнодорожного транспорта. Прибор состоит из двух колец— наружного и внутреннего (см рис. 2). Вставленные одно в другое кольца постепенно вдавливают вращением и слой свежеуложенного набрызгбетона и оставляют в нем до полного схватывания материала. Диаметр внутреннего кольца 100 —150 мм, сцепление определяют путем отрыва внутреннего кольца гидродомкратом, опирающимся на внешнее кольцо.
Вследствие большого сцепления набрызгбетона с внутренним кольцом, имеющим спиральную нарезку, отрыв происходит но контакту с породой.
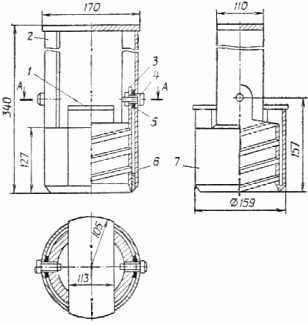
Рис. 2. Прибор для определения сцепления набрызгбетона с грунтовой поверхностью:
1—опорный столик: 2—захват; 3—внутреннее кольцо; 4—штифт; 5—уплотняющая шайба;
6—фиксирующее кольцо; 7—наружное кольцо
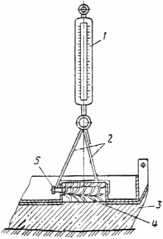
Рис. 3. Прибор для определения сцепления набрызгбетона со слабой породой:
1—динамометр; 2— тяги; 3—набрызгбетон; 4— порода; 5—фиксирующие винты
При использовании прибора НИИСПа Госстроя УССР (см. рис. 3) для определения сцепления набрызгбетона со слабыми породами производят отбор образцов породы при помощи компрессионных колец для испытания грунтов, вдавливаемых в породу. Компрессионные кольца с отобранными образцами породы закрывают крышками и помещают в специальный прибор так, чтобы они открытой лицевой стороной были прижаты по контуру к отверстиям в панели прибора. Затем на панель с образцами наносят набрызгбетон и после схватывания динамометром определяют усилие отрыва породы от набрызгбетона. Во всех случаях следует испытывать не менее трех образцов-близнецов одного возраста, а сами испытания проводить непосредственно на месте производства работ.
Приложение 9
Обязательное
ХАРАКТЕРИСТИКИ БЕТОНА
(извлечение из СНиП 2.03.01—84)
Таблица 1
Расчетное сопротивление бетона для предельных
состояния первой группы Rb, и Rbt, МПа,
при классе бетона по прочности на сжатие
Вид сопротивления |
Бетон |
В25 |
В30 |
В35 |
В40 |
В45 |
Сжатие осевое (призменная прочность) Rb |
Тяжелый и мелкозернистый |
14,5 |
17,0 |
19,5 |
22,0 |
25,0 |
|
Легкий |
14,5 |
17,0 |
19,5 |
22,0 |
— |
Растяжение осевое Rbt |
Тяжелый |
1,05 |
1,20 |
1,30 |
1,40 |
1,45 |
|
Мелкозернистый групп:
A (Мк > 2) |
1,05 |
1,20 |
1,30 |
1,40 |
( |
|
Б (Мк ( 2) |
0,90 |
1,00 |
— |
— |
— |
|
Легкий при
мелком заполнителе: плотном |
1,05 |
1,20 |
1,30 |
1,40 |
( |
|
пористом |
0,90 |
1,00 |
1,10 |
1,20 |
( |
Таблица 2
Расчетные сопротивления бетона для предельных состояний
второй группы Rb,ser и Rbt,ser , МПа,
при классе бетона по прочности на сжатие
Вид сопротивления |
Бетон |
В25 |
B30 |
В35 |
В40 |
В45 |
Сжатие осевое (призменная прочность) Rb,ser |
Тяжелый мелкозернистый |
18,5 |
22,0 |
25,5 |
29,0 |
32,0 |
|
Легкий |
18,5 |
22,0 |
25,5 |
29,0 |
— |
Растяжение |
Тяжелый |
1,60 |
1,80 |
1,95 |
2,10 |
2,20 |
осевое
Rbt.ser |
Мелкозернистый групп:
A (Мк > 2) |
1,60 |
1,80 |
1,95 |
2,10 |
( |
|
Б (Мк ( 2) |
1,35 |
1,50 |
— |
— |
— |
|
Легкий при мелком заполнителе: плотном |
1,60 |
1,80 |
1,95 |
2,10 |
( |
|
пористом |
1,35 |
1,50 |
1,65 |
1,80 |
— |
Таблица 3
Начальные модули упругости бетона при сжатии и растяжении, МПа,
при классе бетона по прочности на сжатие
Бетон |
В25 |
B30 |
B35 |
В40 |
В45 |
Тяжелый естественного твердения |
30,0 |
32,5 |
34,5 |
36,0 |
37,5 |
Мелкозернистый естественного твердения групп:
A (Мк > 2) |
24,0 |
26,0 |
27,5 |
28,5 |
( |
Б (Мк ( 2) |
21,5 |
23,0 |
— |
— |
— |
Легкий поризованный марки по средней плотности Д:
1600 |
16,5 |
17,5 |
18,0 |
( |
( |
1800 |
18,5 |
19,5 |
29,5 |
21,0 |
( |
2000 |
21,0 |
22,0 |
23,0 |
23,5 |
— |
Приложение 10
Справочное
СВЕДЕНИЯ ОБ АЛГОРИТМАХ И ПРОГРАММАХ РАСЧЕТА КРЕПИ ТОННЕЛЬНЫХ ВЫРАБОТОК
| | | | | | | |
№
пп |
Название программы |
Авторы алгоритма и программы |
Язык программирования |
Тип
ЭВМ |
Краткая характеристика программы |
Организация—держатель программы |
1 |
Расчет обделок не кругового поперечного сечения |
Н. Н. Фотиева
В. Л. Кипенев
А. А. Ланда |
ФОРТРАН |
ЕС |
Определение напряженного состояния монолитных обделок некругового очертания. Расчет основан на решении плоской контактной задачи о равновесии кольца в упругой среде |
Ленметрогипротранс |
2 |
Расчет многослойных и комбинированных обделок кругового очертания |
Н. С. Булычев
Е. Е. Левин
А. А. Ланда |
ФОРТРАН |
ЕС |
Расчет сборной или монолитной трехслойной обделки кругового очертания методами теории упругости |
То же |
3 |
Крепь |
Б. 3. Амусин
Н. С. Булычев
Н. А. Романова |
ФОРТРАН |
ЕС |
Расчет обделки подземной выработки некругового очертания замкнутой, незамкнутой монолитной, шарнирной или сборной при условии сцепления или проскальзывания по контакту и с возможной потерей устойчивости. Расчет проводится по методу начальных параметров |
” |
4 |
Комбинированная крепь |
Д. И. Колин
Л. Н. Колина |
АЛГОЛ-60 |
ЕС |
Определение оптимальных параметров комбинированной крепи из анкеров и набрызгбетона по критериям минимума себестоимости и трудовых затрат при возведении крепи |
ЦНИИС |
5 |
“Недра” |
Б. 3. Амусин
К. А. Ардашев
Ю. М. Васинский |
ФОРТРАН |
ЕС |
Автоматизация системы проектирования капитальных горных выработок позволяет выбрать параметры крепи по заданным габаритам, данным геологических изысканий и т. п. |
ВНИМИ |
6 |
“Сейсм” |
Н. Н. Фотиева
И. Я. Дорман
С. Ю. Хазанов
С. А. Абдрафикова |
ФОРТРАН |
ЕС |
Расчет круговых обделок глубокого заложения на сейсмические воздействия |
ЦНИИС |
7 |
Расчет круговых обделок |
И. Е. Левин |
ФОРТРАН |
ЕС |
Расчет круговых обделок мелкого заложения на сейсмические воздействия |
Ленметрогипротранс |
8 |
Анкер |
Л. Л. Старчевская |
ФОРТРАН |
ЕС |
Определение напряженно-деформированного состояния и устойчивости выработки, подкрепленной анкерами |
То же |
9 |
RAK |
В. В. Чеботаев |
ПЛ-1 |
ЕС |
Расчет арочной крепи. Определение шага арок в зависимости от горно-технических условий. Определение эпюры моментов, нормальных сил и реакции от единичный нагрузок |
ГТМ |
10 |
Нелинейный расчет обделки |
В. А. Гарбер |
ФОРТРАН |
ЕС |
То же с учетом нелинейности физико-механических свойств грунта, материала обделки, диаграммы деформирования |
ЦНИИС |
11 |
Расчет крепи |
Л. Б. Кучумова |
АП |
|
Расчет анкер-набрызгбетонной крепи подземных гидротехнических сооружений в породах с коэффициентом крепости больше 4 |
ЦНИИС |
12 |
“Спринт” |
Н. Н. Шапошников В. Б. Бабаев
Г. В. Полторак
Е. Г. Перушев |
ПЛ-1, ФОРТРАН, АССЕМБЛЕР |
ЕС |
Система пространственного расчета конструкции и материалов, находящихся под воздействием статических и динамических нагрузок. Алгоритм расчета основан на методике конечных элементов (МКЭ) |
МИИТ |
13 |
STATUS |
Т. Л. Бердзенешвили О. К. Постольская |
ФОРТРАН |
ЕС |
Программный комплекс для статического расчета по МКЭ плоских и пространственных систем с анизотропными и нелинейными характеристиками |
МИСИ |
14 |
FAK-1 |
Н. Н. Фотиева |
ФОРТРАН |
ЕС |
Расчет напряженного состояния замкнутой некруговой обделки с учетом места установки и сейсмических воздействий |
ТПИ |
15 |
“Анкер-контакт” |
Д. И. Колин
Л. Н. Колина |
АЛГОЛ-60 |
ЕС |
Определение усилий, возникающих в анкерах в процессе взаимодействия их с грунтом, с учетом влияния их друг на друга, времени и места установки, ползучести грунта |
ЦНИИС |
16 |
FOK-4 |
Н. Н. Фотиева
А. Н. Козлов |
ФОРТРАН |
ЕС |
Расчет набрызгбетонной крепи на действие собственного веса пород |
ТПИ |
Приложение11
Обязательное
ОПРЕДЕЛЕНИЕ РАСЧЕТНОГО КОЭФФИЦИЕНТА КРЕПОСТИ fкp.p, СКАЛЬНЫХ ГРУНТОВ ДЛЯ РАСЧЕТОВ НАБРЫЗГБЕТОННЫХ И АНКЕРНЫХ КРЕПЕЙ
Коэффициент крепости fкр.р (коэффициент крепости “в массиве”) определяют по формуле
fкр.р = a ( fкр ,
где fкр — нормативный коэффициент крепости пород (коэффициент крепости по М. М. Протодьяконову) “в куске”; а — коэффициент, учитывающий трещиноватость массива и обеспечивающий переход от коэффициента крепости “в куске” к коэффициенту крепости “в массиве” (табл. 1).
Коэффициент крепости “в куске” определяют по формуле:
fкр = g ( Rc
где Rс—временное сопротивление образца грунта в водонасыщенном состоянии, МПа; g—постоянная сводообразования, равная 0,1 МПа-1.
Таблица 1
Значения коэффициента а
| | | | | |
Категория скальных грунтов по
степени трещиноватости |
Временное сопротивление Rс
грунта одноосному сжатию, МПа |
|
10 |
20 |
40 |
80 |
160 |
1. Практически нетрещиноватые |
1,7 |
1,4 |
1,2 |
1,1 |
1,0 |
2. Слаботрещиноватые |
1,4 |
1,2 |
1,0 |
0,9 |
0,8 |
3. Трещиноватые |
1,2 |
0,9 |
0,7 |
0,6 |
0,5 |
4. Сильнотрещиноватые |
0,9 |
0,7 |
0,5 |
0,4 |
0,3 |
Категорию грунтов по степени трещиноватости определяют согласно табл. 2 в зависимости от трещинной пустотности и густоты трещин (среднее расстояние между трещинами, м); наличие микротрещин не учитывается.
Таблица 2
Категории грунтов
Трещинная пустотность, % |
Степень трещиноватости и густота трещин, м |
|
очень
редкая,
более 1,0 |
редкая,
1,0—0,3 |
густая,
0,3—0,1 |
очень
густая,
менее 0,1 |
Малая, менее 0,3 |
I |
II |
III |
IV |
Средняя, 0,3—1,0 |
II |
III |
IV |
— |
Большая, 1,0—3,0 |
III |
IV |
— |
— |
Очень большая, более 3,0 |
IV |
— |
— |
— |
Примечание. Прочерки в табл. 2 означают, что в этих условиях применение анкерной или набрызгбетонной крепей неэффективно или невозможно.
При определении трещинной пустотности рыхлый или глинопородный материал заполнения трещин не учитывают.
При большой и очень большой трещинной пустотности и хорошо выраженной расчлененности массива на блоки его относят к V категории (прочерки в табл. 2).
В условиях ожидаемого полного нарушения сплошности скальных грунтов в результате интенсивного их расслоения (кливаж) грунты относят к V категории (прочерки в табл. 2).
При наличии поверхностей скольжения категорию грунта повышают на одну ступень.
При трещинах, частично залеченных твердым (кристаллическим) материалом, категорию грунта понижают на одну степень, а при полностью залеченных трещинах грунт относят к I категории.
В условиях обводненной выработки расчетные значения коэффициента крепости fкр.р следует дополнительно снижать умножением на понижающий коэффициент по табл. 3.
Таблица 3
Значения дополнительного понижающего коэффициента
к коэффициенту крепости породы fкp.p за счет обводненности выработки
| | | |
Интенсивность водопритока в |
Грунты скальные при трещинной пустотности |
выработку |
малой |
средней |
большой и очень большой |
Слабый капёж |
1,0 |
1,0 |
0,9 |
Сильный капёж |
1,0 |
0,9 |
0,8 |
Очень сильный капёж и струи |
0,9 |
0,8 |
0,7 |
Если наиболее развитой системой трещин являются трещины напластования, составляющие с осью тоннеля угол менее 45°, на расчетный коэффициент крепости fкр.р вводят дополнительный коэффициент 0,9.
При проходке выработки в скальных грунтах без применения буровзрывных работ расчетный коэффициент крепости умножают на повышающий коэффициент:
1,3—для сильнотрещиноватых и раздробленных грунтов;
1,2—для прочих грунтов.
Приложение 12
Рекомендуемое
ДАННЫЕ ДЛЯ ВЫБОРА СПОСОБА НАНЕСЕНИЯ НАБРЫЗГБЕТОННОГО ПОКРЫТИЯ НА ОБВОДНЕННУЮ ПОВЕРХНОСТЬ. ТРЕБОВАНИЯ К ВЯЖУЩИМ
| | | | |
Характер обводненной поверхности |
Рекомендации по технологии нанесения набрызгбетонного покрытия |
Необходимое время схватывания вяжущего (не позднее). |
Небольшой водоприток в виде капежа или незначительных течей |
Первый слой набрызгбетона рекомендуется наносить с пониженным В/Ц |
— |
Сконцентрированный водоприток |
Предварительно осуществляют отвод воды посредством выбуривания коротких шпуров и установки на быст-ротвердеющем цементе коротких патрубков-кондукторов, на которые надевают шланги. Набрызгбетон на осушенные поверхности наносят обычным способом |
( |
Водоприток по всей поверх-ности, л/(мин(м):
до 1 |
Выбирают расстояние от сопла до поверхности набрызга от 0,5 до 0,6 м |
2 |
до 2 |
|
1 |
до 3 |
|
1 |
до 5 |
|
Мгновенное |
8 |
Сначала закрепляют сухие или сырые поверхности обычным способом, затем сжатым воздухом, истекающим из насадки с овальным щелевым отверстием, сдувают воду на уже закрепленные поверхности с интенсивным водопритоком. Под защитой воздушной струи наносят набрызгбетон с ускорителями на еще не закрепленные поверхности |
” |
>8 |
В местах течей устанавливают резиновые и металлические трубки для отвода воды, при наличии водоносных трещин—разрабатывают канавки |
” |
Примечание. Во всех случаях, указанных в таблице, используют смеси с повышенным содержанием цемента. Для выбора вида вяжущего и химических добавок следует использовать данные табл. 1 прил. 7.
Приложение 13
Справочное
ОБОРУДОВАНИЕ ДЛЯ НАБРЫЗГБЕТОННЫХ РАБОТ
Таблица 1
Технические характеристики набрызгбетон-машины
| | | | | | | | | | | | | |
|
Камерные |
Шнековые |
Роторные |
Показатели |
С-630Л |
С-702* |
БМ-60 |
БМ-60П |
СБ-67
(С-1007) |
ТП-2 |
ПБМ-1 |
ПБМ-2 |
ПБМ-1,5 |
БМ-68У |
БМ-70** |
Производительность по сухой смеси, м3/ч |
4 |
3 |
4 |
3—4 |
4 |
2 |
8 |
8 |
11 |
6 |
6 |
Максимальная крупность заполнителей, мм |
25 |
10 |
25 |
25 |
20 |
15 |
10 |
10 |
10 |
16 |
16 |
Внутренний диаметр материального шланга, мм |
50 |
38 |
50 |
50 |
50 |
50 |
50 |
50 |
50 |
50 |
65 |
Давление сжатого воздуха, МПа (кгс/см2) |
0,15(0,5 (1,5(5) |
0,15(0,5 (1,5(5) |
0,15(0,5 (1,5(5) |
0,5
(5) |
0,5
(5) |
0,3(0,5
(3(5) |
0,2(0,3 (2(2,8) |
0,2(0,3 (2(2,8) |
0,2—0,3 (2(2,8) |
0,4—0,5
(4(5) |
0,5
(5) |
Дальность транспор-тировки, м:
по горизонтали |
200 |
150 |
200 |
200 |
200 |
100 |
200 |
200 |
200 |
200 |
200 |
по вертикали |
50 |
40 |
30 |
30 |
35 |
40 |
— |
— |
— |
10 |
50 |
Мощность электропривода, кВт |
2,8 |
2,8+1 |
4,5 |
— |
2,8 |
7 |
— |
— |
— |
5,5 |
1,5 |
Мощность пневмопривода, кВт |
— |
— |
— |
2,2 |
— |
— |
8,8 |
10,2 |
8,8 |
— |
— |
Основные размеры, мм:
высота |
1660 |
1830 |
1600 |
1600 |
1700 |
( |
( |
1630 |
1630 |
1625 |
( |
ширина |
1000 |
895 |
1100 |
1100 |
1100 |
540 |
1320 |
1270 |
880 |
850 |
1080 |
длина |
1670 |
1537 |
1420 |
S700 |
2000 |
1000 |
4313 |
3300 |
3470 |
1400 |
3400 |
Загрузочная высота, мм |
1660 |
— |
1600 |
!600 |
1700 |
800 |
1780 |
1630 |
1630 |
1400 |
— |
Масса, кг |
886 |
1000 |
1000 |
1000 |
1000 |
470 |
4500 |
3100 |
2225 |
850 |
5400 |
_________
* Отличается от С-630А наличием загрузочного ковша.
** Отличается от БМ-68У наличием загрузочного устройства грейферного типа.
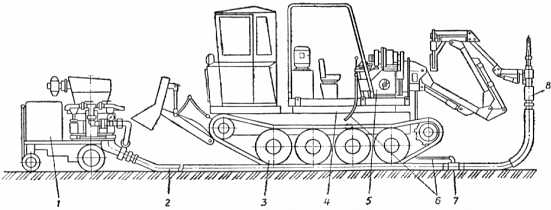
Рис. 1. Комплект оборудования для набрызгбетонирования при возведении транспортных сооружений:
1—набрызгбетон-машина: 2—материальный шланг; 3—трактор трелевочный ГТД-55А; 4—рама промежуточная: 5—манипулятор; 6—водяной шланг; 7—смеситель; 8—сопло
Комплект оборудования ЦНИИС для набрызгбетонных работ
Комплект механизированного оборудования для набрызгбетонироиания “сухим” методом состоит из набрызгбетон-машины роторного типа с материальными шлангами и манипулятора, выполненного в виде автономного модуля, который может устанавливаться на соответствующее транспортное средство на гусеничном, пневмоколесном или рельсовом ходу в зависимости от условий строительного объекта (рис. 1).
Комплект предназначен для работы и наземных и подземных условиях при температуре от 0 до + 40°С при влажности до 100%.
Для обеспечения работы комплекса необходимы источники: электроэнергии общей мощностью не менее 1,5 кВт, напряжением 380 В и частотой 50 Гц; сжатого воздуха давлением не менее 0,6 МПа и расходом 12 м3/мин; водоснабжения давлением 0,6 МПа и расходом 4 м3/мин.
Набрызгбетон-матина (рис. 2) предназначена для дозированного ввода сжатым воздухом готовой сухой бетонной смеси в систему материальных рукавов для пневмотранспорта ее к соплу.
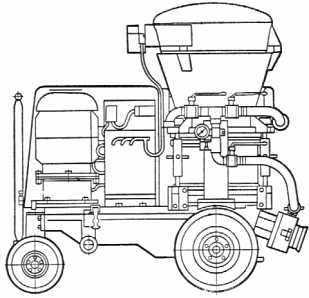
Рис. 2. Набрызгбетон-машина
От машины сухая смесь естественной влажности, в том числе содержащая волокна (дисперсное армирование), транспортируется по рукавам в воздушном потоке с низкой концентрацией материала, примерно 20%.
Вода для затворения цемента впрыскивается в транспортную систему за 3 м до сопла.
Машина работает по принципу непрерывной подачи сухой смеси и шланг для транспортировки. Загрузка заранее приготовленной смеси естественной влажности происходит через загрузочную воронку в бункер машины, снабженный вибратором. Из бункера, благодаря вибрации, смесь попадает в загрузочные камеры вращающегося ротора, футерованные резиновыми вставками в виде коротких отрезков шланга, забивка которых исключается благодаря вибрации под действием сжатого воздуха.
Техническая характеристика
Производительность, м3/ч ....................... 8
Тип привода набрызгбетон-машины ..............Электрический
Электродвигатель:
тип ....................................... 4А1604/6УЗ
потребляемая мощность, кВт:
при n=16,3 с-1 (970 мин-1) ..................... 7,5
при n=24,6 с-1 (1470 мин-1) ................. 8,5
напряжение, В ........................... 380, 50 Гц
Частота вращения ротора с-1 (мин-1):
при n=16,3 с-1 электродвигателя ............... 0,11 (6,5)
при n=24,6 с-1 электродвигателя ............... 0,16 (9,8)
0,11—0,16
Расход воздуха, м3 с-1 (м3, мин-1) ................. (6,5—9,5)
Давление подводимого воздуха, МПа .............. 0,4—0,6
Расход воды, м3/ч .............................. 4—5
Давление подводимой воды, МПа ................. 0,4—0,6
Максимальный размер фракций бетонной
смеси, мм, не более ............................. 16
Емкость приемной виброворонки, м3............... 0,25
Дальность транспортировки, м, не более ........... 100
Высота подъема, м, не более ..................... 30
Габаритные размеры, мм, не более:
длина ...................................... 1850
ширина .................................... 860
высота ..................................... 1552
Масса, кг, не более ............................. 1100
Ротор с загрузочными камерами вращается вокруг вертикальной оси. Герметизация ротора осуществляется верхним и нижним неподвижными резиновыми дисками. Верхний диск имеет систему отверстий, служащих для загрузки камер сухой смесью, продувки камер сжатым воздухом, выпуска остатка сжатого воздуха в конце цикла. Нижний диск имеет только два отверстия—для выхода смеси ротора и выпуска сжатого воздуха.
При совпадении отверстия загрузочной камеры с отверстием для загрузки в верхнем диске сухая смесь попадает в загрузочную камеру, а при совпадении нижнего отверстия заполненной загрузочной камеры с отверстием для выхода в нижнем диске смесь через продувочную камеру уносится постоянным непрерывным потоком сжатого воздуха в транспортную систему. За три метра до подхода к соплу смесь проходит через специальную камеру где ее затворяют регулируемым количеством воды, впрыскиваемой перпендикулярно к воздушному потоку. На выходе из сопла получается смоченный и перемешанный песчано-гравийный раствор, который с большой скоростью под действием сжатого воздуха наносится на обрабатываемую поверхность. Материальные рукава соединяются между собой, а также с набрызгбетон-машиной при помощи специальных быстрорязъемных соединений.
Манипулятор стрелового типа (рис. 3) предназначен для производства набрызгбетонирования безопасным механизированным способом, обеспечивая дистанционное управление соплом и ведение его по требуемой траектории.
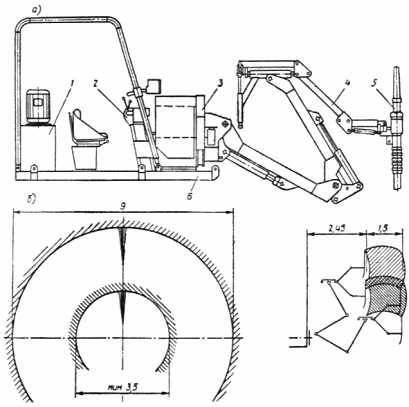
Рис. 3. Общий вид (а) и зона действия (б) манипулятора для набрызг-бетонирования:
1(насосная станция; 2—пульт управления; 3—опорно-поворотное устройство;
4—стрела; 5—сопло; 6—рама с кабиной
При этом сохраняется необходимое строго перпендикулярное положение сопла на консоли стрелы к обрабатываемой поверхности на постоянном заданном расстоянии от нее.
Манипулятор может применяться для работы с машинами как для “сухого”, так и “мокрого” способов набрызг-бетона.
Техническая характеристика
Зона действия, мм:
максимальный диаметр тоннеля ................. 9000
минимальный диаметр тоннеля ................. 3800
максимальный вылет стрелы (сопла) ............. 3950
Максимальная величина подачи сопла вдоль
центральной оси машины (рабочий ход), мм 1500±50
Тип привода манипулятора ..................... Гидравлический
Максимальное давление рабочей жидкости
в гидросистеме, МПа, не более .................. 10
Электродвигатель насосной станции:
потребляемая мощность, кВт ................. 7,5
тип ...................................... 4А132 4Ц1
напряжение, В ............................. 380
Диаметр материального рукава, мм .............. 65
Угол поворота стрелы вокруг горизонтальной
оси ......................................... 360
Частота вращения стрелы, мин-1, не менее ........ 1,3
Угол поворота 1-го и 2-го колен стрелы, град ...... 60 ±3
Угол поворота 3-го колена стрелы вокруг
горизонтальной оси, град ....................... ±45
Угол поворота сопла в плоскости третьего
колена стрелы, град ............................ 60 ±3
Величина подачи сопла вдоль продольной
оси манипулятора, мм .......................... 1500±50
Скорость перемещения сопла, мм/с-1 .............. 0—500
Диаметр сопла, мм, не менее .................... 50
Частота вращения сопла, с-1 ..................... 0—0,6
Величина эксцентриситета вращения сопла, мм ..... 17; 20; 25
Габаритные размеры в транспортном
положении, мм, не более:
длина ..................................... 4940
ширина .................................... 982
высота .................................... 157
Масса, кг, не более ............................. 1500
Шарнирно-сочлененная стрела имеет возможность неограниченного вращения в опорно-поворотном устройстве вокруг центральной оси манипулятора.
Держатель сопла шарнирно закреплен на консоли 3-го колена стрелы и с помощью гидроцилиндра может изменять наклон в плоскости этого колена. Само сопло при помощи гидромотора совершает вращательные эксцентричные движения, имитирующие движение сопла при ручной технологии набрызгбетона.
Манипулятор работает по принципу последовательного нанесения сплошной полосы набрызгбетона заданной толщины и ширины, слой набрызгбетона равномерно покрывает обрабатываемый участок поверхности.
При обработке боковой поверхности (стен тоннелей, откосов и т. п.) сопло перемещается параллельно этой поверхности на величину рабочего хода. После нанесения набрызгбетона на обрабатываемом участке поверхности сопло поднимают или опускают в зависимости от технологии ведения работ при помощи соответствующих механизмов управления. После этого производится обработка следующего соседнего участка (полосы верхней или нижней) при обратном рабочем ходе сопла. Затем технологический цикл повторяется. В процессе технологических перемещений сопла идет непрерывная подача смеси на обрабатываемую поверхность.
При обработке перпендикулярных к центральной оси машины поверхностей, например лба забоя выработки, рабочим движением является вращение стрелы манипулятора вокруг его центральной оси. Направление сопла на консоли стрелы при этом переориентируется на 90°.
При технологии “сухого набрызгбетонирования” в кабине манипулятора устанавливается вентиль управления режимов ввода воды в материальный шланг.
Таблица 2
Предотвращение и устранение неисправностей в работе
набрызгбетон-машины
| | | | | | | | | | | | | |
Признаки неисправности |
Возможные причины |
Способ предотвращения и устранения |
При открытом впускном кране воздух выходит медленно, при работе машины замечается пыление из-под прокладки верхнего затвора |
Порча или загрязнение резиновой прокладки под верхним колокольным клапаном; засорение отверстий распределительной втулки сопла |
Осмотр резиновой прокладки, очистка при ее загрязнении, замена новой при неисправности; поддержка рычага нижнего затвора рукой во время загрузки верхней камеры, очистка или замена прокладки новой во время перерыва или после окончания работы; разборка сопла, прочистка отверстия в распределительной втулке |
Замечается пыление из-под прокладки верхнего клапана. При открытом проходном кране выпускной трубы нижний клапан самопроизвольно открывается |
Образование пробки в материальном шланге или в сопле вследствие попадания в сухую смесь зерен размером более 25 мм, а также в результате резких перегибов материального шланга |
Простукивание шланга на участке предполагаемого засорения, разборка сопла и прочистка, продувка и распрямление шланга, снятие выходного материального патрубка и прочистка его |
Материал при выходе из сопла сильно пылит, наблюдается усиленный отскок материала от рабочей поверхности или наносимый на поверхность слой материала чрезмерно жидкий (материал оплывает) |
Резкое изменение консистенции смеси из-за неравномерной подачи воды или неравномерной загрузки сухой смеси в набрызгбетон-машину |
Поддержка равномерного давления в водяном баке и слежение за равномерной подачей воды; загрузка набрызгбетон-машин равномерная и слежение за тем, чтобы в нижней камере было всегда достаточно материала |
Прекращение подачи сухой смеси к соплу |
Прорыв воздуха в местах соединений |
Замена резиновых прокладок в случае их порчи или подтяжка гаек при их ослаблении |
Резкое повышение давления па манометре |
Недостаточность числа оборотов двигателя, засорение воздушного фильтра, понижение давления в компрессоре |
Разборка и прочистка воздушного фильтра; увеличение давления воздуха в компрессоре |
Понижение давления в материальном шланге, шум воздуха в месте прорыва или стыка |
Отказ в работе двигателя при пуске вследствие торможения распределительной тарелки машины схватывающейся смесью |
Очистка распределительной тарелки |
Медленное вращение маховика пневмодвигателя, не вращаются пиевмодвигатель при показании нормального давления на манометре
Неравномерное гудение мотора на высоких тонах |
Нагревание подшипников вала, недостаток смазки или ее загрязнение |
Проверка смазки и в случае ее загрязнения замена новой, а при недостатке смазки—дополнение до требуемого количества |
Приложение 14
Рекомендуемое
ОРГАНИЗАЦИЯ РАБОТ ПРИ ВОЗВЕДЕНИИ НАБРЫЗГБЕТОННОИ КРЕПИ
Таблица 1
Варианты схем организации набрызгбетонных работ
| | | | | | |
Способ и место приготовления сухой |
Технологический транспорт |
Варианты транспортных схем |
Средства для доставки сухой смеси в рабочую |
Используемое оборудование при технологических операциях |
смеси |
|
|
зону |
подача материалов к набрызгбетон-машине |
очистка основания и нанесение набрызгбетонного покрытия |
Централизованно с упаковкой в капсулы |
Безрельсовый |
Через портал выработки по транспортной штольне и сбойкам между выработкой и транспортной штольней |
Капсулы, автотранспортом |
Переставной набрызгбетонный узел на нерельсовом ходу |
Самоходный агрегат на нерельсовом ходу, снабженный манипулятором |
То же |
Рельсовый, шахтная колея с электровозной тягой всех типов |
То же, а также через клетьевой ствол |
Капсулы, на тележках шахтной колеи |
То же, на рельсовом ходу или смонтированный на буровой раме или технологической тележке по типу тележки для нагнетания |
Передвижной агрегат на шахтной колее или манипулятор, смонтированный на буровой раме |
Централизованно, с упаковкой в капсулы |
Рельсовый, железнодорожная колея 1524 мм с локомотивной тягой |
Через портал тоннеля |
Капсулы на технологических платформах железнодорожной колеи |
Оборудование технологического состава на железнодорожной колее, включающее бето-носмесители, набрызгбетон-машину и манипулятор для вождения сопла |
Централизованно, с упаковкой в капсулы |
Рельсовый, железнодорожная колея 1524 мм с локомотивной тягой |
Через портал тоннеля |
Капсулы до перегрузочного узла тележками на шахтной колее, далее на технологических платформах на железнодорожной колее |
Оборудование технологического состава на железнодорожной колее, включающее бето-носмесители, набрызгбетон-машину и манипулятор для вождения сопла |
На бетонном узле на шахтной поверхности |
Безрельсовый |
Через портал выработки по транспортной штольне и сбойкам между выработкой и транспортной штольней |
Автобетоносмесители одиночные или автобетоносмесители в сцепе (автопоезда) |
Переставной на-брызгбетонный узел на нерельсовом ходу |
Самоходный агрегат на нерельсовом ходу, снабженный манипулятором |
То же |
Рельсовый, шахтная колея, электровозная тяга всех типов |
То же |
Шахтные вагонетки саморазгружающиеся или опрокидные: пневмобетононагне-татели типа ПБМ |
То же, на рельсовом ходу или технологическая тележка (по типу тележки для нагнетания) пневмонагнетателями |
То же на рельсовом ходу или смонтированный на буровой раме |
На бетонном узле на шахтной поверхности |
Рельсовый, шахтная колея при тяге аккумуляторными электровозами |
” |
Пневмобетононагне-татели типа ПБМА, а также бетоносмесители на тележках шахтной колеи |
Оборудование технологического состава на шахтной колее, включающее бетоносмесители, набрызгбетон-машину и манипулятор для вождения сопла |
То же |
Рельсовый, шахтная колея при тяге электровозами всех типов |
Через клетьевой ствол |
Шахтные опрокидные вагонетки или контейнеры на тележках шахтной колеи |
Перестановочный набрызгбетонный узел на рельсовом ходу, а также оборудование, смонтированное на буровой раме или технологической тележке по типу тележки для нагнетания |
Передвижной агрегат на шахтной колее или манипулятор, смонтированный на буровой раме |
” |
То же |
Через технологическую скважину с подземным перегрузочным бункером-дозатором |
То же; пневмобето-нонагнетатели типа ПБМА |
То же; пневмобето-нонагнетатели |
То же |
” |
Рельсовая, железнодорожная колея 1524 мм с локомотивной тягой |
Через портал выработки |
Бетоносмесители на технологических платформах колеи 1524 мм |
Оборудование технологического состава на железнодорожной колее, включающее бето-носмесители, набрызгбетон-машину и манипулятор для вождения сопла |
” |
То же |
По транспортной штольне к перегрузочному узлу у сбойки штольни с тоннелем |
Саморазгружающиеся вагонетки на шахтной колее, по транспортной штольне до перегрузочного узла бетоносмесителя на технологических платформах железнодорожной колеи |
То же |
Таблица 3
Порядок производства работ в тоннеле при постоянной и временной анкер-набрызгбетонных крепях
(грунты от средней и большей устойчивости, разработка грунтов буровзрывным способом)
| | | | | | | | |
Работы |
Операции |
Последовательность операций |
|
|
1 |
2 |
3 |
4 |
5 |
6 |
7 |
|
Заряжание, взрывание, проветривание |
|
|
|
|
|
|
|
Проходка
выработки |
Уборка породы |
|
|
|
|
|
|
|
Разработка грунта |
Оборка забоя и контура выработки |
|
|
|
|
|
|
|
|
Обуривание забоя |
|
|
|
|
|
|
|
|
Бурение анкерных шпуров |
|
|
|
|
|
|
|
Временное крепление выработки |
Установка анкеров |
|
|
|
|
|
|
|
|
Нанесение набрызгбе-тона |
|
|
|
|
|
|
|
|
Бурение анкерных шпуров |
|
|
|
|
|
|
|
Возведение постоянной обделки |
Установка анкеров |
|
|
|
|
|
|
|
|
Монтаж армосетки |
|
|
|
|
|
|
|
|
Нанесение набрызгбе-тона |
|
|
|
|
|
|
|
Таблица 4
Порядок производства работ в забое выработки при проходке с временной анкер-набрызгбетонной крепью
(грунты ниже средней устойчивости, разработка грунтов буровзрывным способом,
постоянная обделка монолитная бетонная или сборная)
| | | | | | | | | | |
Работы |
Операции |
Последовательность работ |
|
|
1 |
2 |
3 |
4 |
5 |
6 |
7 |
8 |
|
Заряжание, взрывание, проветривание |
|
|
|
|
|
|
|
|
Разработка грунта |
Уборка породы |
|
|
|
|
|
|
|
|
|
Оборка забоя контура выработки |
|
|
|
|
|
|
|
|
|
Обурирание забоя |
|
|
|
|
|
|
|
|
|
Нанесение на- |
I слой |
|
|
|
|
|
|
|
|
|
брызгбетона |
II слой |
|
|
|
|
|
|
|
|
Временное крепление выработки |
Бурение анкерных шпуров |
|
|
|
|
|
|
|
|
|
Установка анкеров |
|
|
|
|
|
|
|
|
|
Монтаж металлической сетки |
|
|
|
|
|
|
|
|
Таблица 5
Ориентировочные показатели сооружения однопутных и двухпутных тоннелей
| | | | | | | | | | |
Показатели |
Единица |
Вид выработки |
|
измерения |
Полный профиль |
Подсводная часть |
Нижний уступ |
|
|
|
|
|
|
Проходческие работы |
Площадь сечения выработки |
м2 |
120 |
120 |
92 |
59,8 |
52,8 |
52,8 |
63,7 |
63,7 |
Коэффициент крепости |
— |
4—6 |
6(8 |
8 |
4(6 |
4(6 |
6(8 |
4(6 |
6(8 |
Продвигание забоя за цикл |
м |
2 |
2,0 |
3,5 |
2,7 |
3,2 |
3,2 |
3,6 |
3,6 |
Продолжительность цикла |
ч |
24 |
28 |
41 |
34 |
33 |
42 |
28 |
21 |
Скорость проходки по циклограмме |
м/мес |
40 |
42,5 |
50 |
47,5 |
57,5 |
45 |
77,5 |
102,5 |
Временная крепь |
( |
Арки,
набрызгбетон |
Клиновые анкеры, набрызг-бетон |
Железобетонные анкеры |
Железобетонные анкеры, набрызг-бетон |
Железобетонные
анкеры,
набрызгбетон |
Металлические
анкеры,
набрызгбетон |
Трудозатраты на 1 м3 породы |
чел.-см. |
0,04 |
0,04 |
0,05 |
0,08 |
0,08 |
0,11 |
0,05 |
0,03 |
Состав звена |
чел. |
5 |
5 |
4 |
5 |
6 |
6 |
6 |
6 |
Установочная мощность оборудования |
кВт |
180 |
180 |
50 |
150 |
250 |
250 |
250 |
250 |
Потребность в сжатом воздухе |
м3/мин |
100 |
100 |
80 |
80 |
100 |
100 |
100 |
100 |
Потребность в воде |
л/мин |
60 |
60 |
60 |
50 |
50 |
50 |
50 |
50 |
|
|
|
|
|
|
Возведение обделки |
Объем бетона на 1 м тоннеля |
м3 |
31,9 |
6,7 |
2,5 |
4,5 |
31,9 |
5,7 |
31,9 |
5,7 |
Толщина обделки:
свод и стены |
мм |
400—600 |
200 |
100 |
200 |
500(1000 |
200 |
500—1000 |
200 |
обратный свод |
|
400—800 |
( |
( |
200(400 |
400—1150 |
( |
400(1150 |
( |
Скорость бетонирования:
свод и стены |
м/мес |
150 |
400 |
478 |
508 |
150 |
308 |
150 |
308 |
обратный свод |
|
400 |
— |
— |
559 |
300 |
— |
300 |
— |
Продолжительность цикла;
свод и стены |
ч |
43,4 |
10,7 |
4,4 |
3,2 |
42 |
7 |
42 |
7 |
обратный свод |
|
9 |
— |
— |
12 |
12 |
— |
12 |
— |
Состав звена:
свод и стены |
чел. |
6 |
4 |
4 |
4 |
6 |
4 |
6 |
4 |
обратный свод |
|
5 |
— |
— |
5 |
4 |
( |
4 |
— |
Трудозатраты на 1 м3 |
чел./см. |
0,10 |
0,15 |
0,15 |
0,15 |
0,10 |
0,15 |
0,10 |
0,15 |
бетона:
свод и стены |
|
0,10 |
0,15 |
0,15 |
0,15 |
0,10 |
0,15 |
0,10 |
0,15 |
обратный свод |
|
0,14 |
— |
— |
0,25 |
0,16 |
— |
0,16 |
— |
Установленная мощность оборудования |
кВт |
150 |
20 |
20 |
20 |
30 |
20 |
30 |
20 |
Потребность в сжатом воздухе |
м3/мин |
20 |
15 |
15 |
15 |
30 |
15 |
30 |
15 |
Потребность в воде |
л/мин |
50 |
10 |
10 |
10 |
50 |
10 |
50 |
10 |
Приложение 15
Обязательное
ФОРМЫ ЖУРНАЛОВ ОПЕРАЦИОННОГО КОНТРОЛЯ КАЧЕСТВА ПРИ ВОЗВЕДЕНИИ НАБРЫЗГБЕТОННОЙ КРЕПИ И ОБДЕЛКИ
Журнал контроля качества песка, щебня, ПГС (песчано-гравийной смеси)
| | | | | | | | | | | | | | |
Дзта испы |
Место отбора |
Фракционный состав, % |
Объемно-насыпная |
Влажность, % |
Содержание пылевидных илистых и |
тания |
проб, массы пробы |
более
20 мм |
20(
10 мм |
10(
5 мм |
5(
2,5 мм |
2,5—
1,25 мм |
1,25(
0,63 мм |
0,63(
0,315 мм |
0,315—
0,14 мм |
менее
0,14 мм |
масса, т/м3 |
|
глинистых частиц, % |
1 |
3 |
3 |
4 |
5 |
6 |
7 |
8 |
9 |
10 |
11 |
12 |
13 |
14 |
|
|
|
|
|
|
|
|
|
|
|
|
|
|
Испытание провел ф., и., о., должность
Журнал испытания цемента по ГОСТ 10178—76*; ГОСТ 310.3—76; 310.4—76
Дата испытания |
Завод-изготовитель |
Марка цемента по паспорту |
Нормальная густота цементного |
Сроки схватывания начало ,
конец |
Обеспеченность равномерности изменения |
Предел прочности, МПа, в возрасте, сут. |
|
|
завода |
теста, % |
ч, мин |
объема (да, нет) |
3 |
7 |
28 |
1 |
2 |
3 |
4 |
б |
6 |
7 |
8 |
9 |
|
|
|
|
|
|
|
|
|
_________
* Для определения активности цемента допускается применение ускоренной методики ЦНИИПС-2.
Испытание провел ф., и., о., должность
Журнал контроля режима набрызгбетонирования
Место отбора пробы пикета |
Дата работы |
Давление воздуха Рн/бм, в набрызгбетон-машине, МПа |
Давление воды в магистрали Рв, МПа |
Расстояние от поверхности нанесения до сопла l, м |
Угол наклона сопла к поверхности, град |
Величина отскока, Q, % |
Отказы при работе оборудования |
1 |
2 |
3 |
4 |
б |
6 |
7 |
8 |
|
|
|
|
|
|
|
|
Контроль осуществил Ф., и., о., должность
Журнал контроля работоспособности комплекса оборудования для набрызгбетонных работ
|
|
|
|
|
Гидрав- |
|
|
|
|
|
Набрызгбетон-машина |
|
|
|
|
Дата |
Матери-альные шланги
|
Воздухопроводная сеть |
Манжеты и уплотне-ния |
Арматура |
лические шланги и цилин-дры манипу-лятора |
Распределители гидравлические РС-1 |
Масло фильтры |
Давление в гидросистеме |
Дроссели на пульте управления и стреле |
Стрелы манипулятора |
стаканы барабана |
верхний и нижний диски |
воздушная арматура |
вкладыши камеры смешения |
Электрооборудование |
Примечания |
Задания по ремонту |
Подпись сменного инженера |
1 |
2 |
3 |
4 |
5 |
6 |
7 |
8 |
9 |
10 |
11 |
12 |
13 |
14 |
15 |
16 |
17 |
18 |
19 |
|
|
|
|
|
|
|
|
|
|
|
|
|
|
|
|
|
|
|
Журнал контроля состава сухой смеси, приготовления и транспортировки
| | | | | | | | | | | |
Место отбора |
Теоретический расход материалов на 1 м3 сухой смеси, кг |
Фактический расход материалов на 1 м3 сухой смеси, кг |
Время |
Вид доставки компонентов |
Время
доставки смеси |
пробы |
Цемент |
Песок |
Щебень |
Химические добавки |
Цемент |
Песок |
Щебень |
Химические
добавки |
перемешивания смеси, мин |
смеси (раздельный. совместный) |
(компонентов) от БСУ до рабочего места, ч, мин |
1 |
2 |
3 |
4 |
5 |
6 |
7 |
8 |
9 |
10 |
11 |
12 |
|
|
|
|
|
|
|
|
|
|
|
|
Испытание провел Ф., и., о., должность
Журнал контроля соответствия работ по набрызгбетонированию ППР
| | | | | | | | | | | |
Место контроля, пикет |
Оборка поверхности выработки (да, нет) |
Количество шпуров под анкеры; наличие сетки шпуров |
Глубина шпура под анкеры, м |
Угол забуривания шпура, град |
Количество ампул-патронов на 1 шпур |
Время вращения анкера, с |
Вид сетки, размер ячеек, мм |
Способ крепления сетки с анкером (сварка, шайба и т. д.) |
Максимальная и минимальная величины зазора между сеткой и грунтом, см |
Мытье поверхности выработки перед н/б (да, нет) |
Толщина слоя набрызгбетона, см |
1 |
2 |
3 |
4 |
5 |
6 |
7 |
8 |
9 |
10 |
11 |
12 |
|
|
|
|
|
|
|
|
|
|
|
|
Дата проведения контроля
Контроль провел Ф., и., о., должности
Приложение 16
Рекомендуемое
УСКОРЕННЫЙ СПОСОБ ОПРЕДЕЛЕНИЯ МОРОЗОСТОЙКОСТИ НАБРЫЗГБЕТОНА
1. Применение ускоренного метода определения морозостойкости
1.1. Ускоренное определение морозостойкости осуществляется для контроля морозостойкости набрызгбетонов тоннельных обделок.
1.2. Контролю подвергаются набрызгбетоны рабочего состава, твердевшие 28 суток в условиях, аналогичных условиям твердения набрызгбетона в обделке тоннелей.
1.3. Метод предусматривает оценку морозостойкости набрызгбетонов по параметрам структуры образцов бетона.
1.4. Для контроля морозостойкости проводятся испытания бетонных образцов по приведенному ниже способу.
2. Приборы и оборудование
Для проведения испытаний требуется следующее оборудование и приборы:
металлические формы размерами 100 х 100 х 100 или 150 х 150 х 150 мм для изготовления образцов, соответствующие требованиям государственного стандарта;
термовакуумный или сушильный шкаф, обеспечивающий температуру в камере до +95°С;
колбы Ле-Шателье—Кандло или объемометры, обеспечивающие точность измерения 0,1 см3;
лабораторные весы типа ВЛТ или ВЛТК или другого типа, обеспечивающие измерение массы до 1 кг с точностью измерения 0,1 г;
пресс для испытаний образцов на сжатие, обеспечивающий усилие сжатия не менее 1,2 МН.
3. Изготовление образцов
3.1. Для проведения ипытаний из рабочей смеси набрызгбетона изготавливают 6 образцов размерами 100 х 100 х 100 (150 х 150 х 150) мм.
3.2. Образцы изготавливают из набрызгбетонной смеси состава, идущего на приготовление обделки, морозостойкость которых определяется.
3.3. Режим приготовления и твердения набрызгбетонных образцов должны быть такими же, как и при изготовлении и твердении обделки, морозостойкость которых определяется.
3.4. Образцы изготавливают на специальном стенде или любым способом, обеспечивающим получение образцов с той же плотностью и структурой, что и набрызгбетон в обделке.
3.5. После изготовления и твердения полученные образцы проверяют на наличие в них видимых дефектов (отколов, раковин и др.). Образцы, имеющие дефекты, исключают из испытаний.
4. Проведение испытаний и прогнозирование морозостойкости
4.1. Изготовленные образцы испытывают с целью определения их структурных характеристик: условно-замкнутой Пу.з интегральной Пи пористостей.
4.2. Каждый изготовленный образец испытывают на сжатие и из оставшейся после испытании части образца отбираются отдельные куски из различных частей образца для получения среднего значения пробы таким образом, чтобы общая масса отобранных частей составляла не менее 300 г.
4.3. Определение интегральной и условно замкнутой пористостей производится согласно требованиям ГОСТ 12730.0, ГОСТ 12730.1—78, ГОСТ 12730.2—78, ГОСТ 12730.03—78, ГОСТ 12730.04—78, ГОСТ 12730.05—78.
4.4. Определение величины Пи ведут в следующем порядке. Из кусков образцов, отобранных согласно и. 4.2, удаляется крупный заполнитель и разрушенные некрепкие части. Затем каждый из кусков насыщают водой до полного насыщения путем постепенной заливки водой. После этого образцы вынимают из воды, взвешивают и определяют массу водонасыщенных образцов тв.
После этого производят гидростатическое взвешивание водонасыщенных кусков образца и определяют массу водонасыщенного образца в воде тн. Далее определяют объем образца Vo пo формуле
(1)
где (H2O — плотность воды, принимаемая равной 1 г/см3.
Затем отобранные части образцов высушивают до постоянной массы в термовакуумном шкафу при температуре 25°С и давлении 66,6 Па или в сушильном шкафу при температуре не выше 95°С и определяют массу каждого высушенного куска mc. После этого определяют среднюю плотность каждого (о по формуле
(2)
и вычисляют среднее значение (о для образца.
Затем определяют интегральную (открытую) пористость, численно равную водопоглощению по массе по формуле
. (3)
4.5. Условно-замкнутую пористость определяют следующим образом. Вначале определяют истинную плотность кусков образцов, полученных по п. 4.4. Для этого высушенные куски образца перетирают в порошок до такой тонкости, чтобы он проходил через сито 008, перемешивают отдельные части образца для получения однородного порошка и испытывают с помощью объемомера типа Ле-Шателье—Кандло, заполненного керосином или другой инертной к цементу жидкостью. Истинную плотность ( определяют но формуле
, (4)
где т—масса порошка, пошедшая на испытание; V—объем жидкости, вытесненной массой порошка, используемого для испытания.
Затем определяют общую пористость По по формуле
, (5)
где (с и ( определены по формулам (2) и (5).
После этого определяют условно замкнутую пористость Пу.з как разность между общей и интегральной из выражения
Пу.з = По ( Пи. (6)
4.6. После проведения испытаний по определению значений Пу.з и Пи на всех 6 образцах для дальнейших расчетов берется среднее значение всех определений.
4.7. По полученным значениям условно замкнутой и интегральной пористости вычисляется значение критерия морозостойкости Кмрз по формуле
, (7)
где Пи н Пу.з определяют по формулам (3) и (6) соответственно.
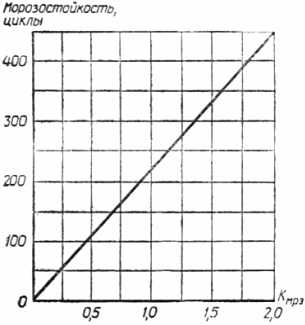
Зависимость морозостойкости от критерия морозостойкости Кмрз
4.8. Марка набрызгбетона по морозостойкости F определяется по номограмме (рисунок) или по формуле
F=Кмрз(А, (8)
где Кмрз — критерий морозостойкости, определяемый по формуле (7); А — эмпирический коэффициент, который для набрызгбетона принимается равным 200.
Приложение 17
Справочное
ПРЕДВАРИТЕЛЬНО-НАПРЯГАЕМЫЕ АНКЕРЫ
Предварительно напрягаемые анкеры (ПНА) в зависимости от характера трещиноватости и обводненности породного массива могут выполняться в виде стержневых конструкций, омоноличенных либо по всей длине, либо за пределами закрепляемой зоны в замке (корне) и в оголовке (корневые анкеры).
ПНА предназначаются для крепления большепролетных выработок и вертикальных обнажении горного массива в трещиноватых скальных грунтах с коэффициентом крепости f(2 (см. п. 4.28 настоящих Норм).
В этих условиях прочность закрепления замков должна обеспечиваться не ниже 550 кН. При пересечении замками анкеров зон дробления или глинистых прослоек толщиной более 1 м (по направлению оси замка) возможно снижение прочности закрепления в результате ослабления сцепления цементно-песчаного раствора со стенками скважины. В этих случаях вопрос о способах повышения прочности закрепления замков должен решаться на основании результатов дополнительных контрольных испытаний замков.
Для изготовления анкерных стержней используют арматуру периодического профиля, металлические канаты, арматурные проволоки, пряди, для омоноличивания—песчано-цементные и полимерные составы. При использовании песчано-цементных составов работы по установке ПНА должны производиться при температуре воздуха в тоннеле и раствора не ниже плюс 5°С, при полимерных—не ниже минус 5°С.
Конструктивно омоноличенный по всей длине ПНА представляет собой установленный в буровую скважину арматурный стержень, изготовляемый из стали марки 25Г2С класса A-III, который после предварительного натяжения омоноличивается нагнетанием в скважину цементно-песчаного раствора.
Стержень по возможности должен изготовляться из цельной арматуры без стыка, а соединение его с хвостовиком осуществляется встык контактной сваркой под флюсом.
Предел прочности в 7-суточном возрате образцов растворов, применяемых для омоноличивания ПНА, должен быть не ниже 20 МПа.
Основание оголовка ПНА выполняется из бетона марки М300 (класс В22,5).
Предел прочности в 7-суточном возрасте образцов бетона должен быть не менее 15 МПа.
Оборудование для приготовления раствора и инъектирования скважин включает:
растворосмесительную установку вместимостью 40—80 л; рекомендуется для применения растворомешалка турбулентная типа С-868 с вертикальным использованием вала вместимостью 80 л;
плунжерный растворонасос типа С-757 или С-251 производительностью до 1 м3/ч с виброситом;
ручной растворонасос типа С-420А;
инъекционные резиновые шланги диаметром от 1 до 11/2’’, рассчитанные на давление до 1,0 МПа;
инъекционные трубки с внутренним диаметром 20—22 мм и толщиной стенок 2—3 мм, длиной 10 м, изготовленные из полиэтилена высокой плотности или стальные;
мерные емкости для дозировки раствора.
Оборудование для натяжения стержней ПНА состоит из гидравлического домкрата усилием не менее 600 кН, установочных приспособлений к нему и насосной станции типа НСП-400.
В состав вспомогательного оборудования входят подмости для производства работ по установке, лебедка грузоподъемностью 0,3—0,4 т для подъема стержней ПНА и других материалов на подмости, а также различный ручной инструмент (лопаты, кувалды, ключи гаечные и т. п.).
К месту работ по установке ПНА должны быть подведены электроэнергия, вода и сжатый воздух.
Установке анкеров предшествует бурение скважин с продувкой для очистки от буровой мелочи, осыпавшейся породы и удаления скопившейся воды. При водопритоке более 1 л/мин производятся цементация скважины до его прекращения и повторное разбуривание.
Непосредственно после инъектирования в скважину вводится стержень ПНА и устанавливается в проектное положение. Разрыв во времени между окончанием инъектирования и установкой стержня более 30 мин не допускается.
При устройстве оголовка конец обсадной трубы должен быть введен в устье скважины. Закладные детали установить так, чтобы плоскость плиты была перпендикулярна оси скважины.
По периметру плиты устанавливается опалубка, после чего пространство между ней и скальной поверхностью заполняется бетоном.
После выполнения указанных операций предусматривается технологический перерыв не менее 7 суток для набора необходимой прочности раствором замка и бетоном оголовка, после чего производится вторичное инъектирование.
Натяжение стержня ПНА следует производить не позднее чем через 1 ч с момента окончания вторичного инъектирования.
До установки в скважины стержни ПНА должны пройти испытания на прочность по специальной методике.
Приложение 18
Обязательное
ФОРМА ЖУРНАЛА ИСПЫТАНИЙ МЕТАЛЛИЧЕСКИХ АНКЕРОВ
Название выработки______________________________________________
Дата установки ________________________ Дата испытания ___________
Пикет __________________________________________________________
№ анке- |
Нагрузка, кН |
Примечание |
ров |
Скольжение, мм |
|
|
|
|
|
|
|
|
|
|
|
|
|
|
|
Схема расположения анкеров и краткое описание состояния
выработки в месте испытания
Подписи: Начальник участка Начальник смены
Маркшейдер участка Сменный маркшейдер
Номограммы для пролета выработки:
а—при В=3,0 м; б—при В=6,6 м; в—при В=9,0 м; г—при В=12,0 м
Приложение 19
Рекомендуемое
МЕТОДИКА ОПТИМИЗАЦИИ ПАРАМЕТРОВ АНКЕР-НАБРЫЗГБЕТОННОИ КРЕПИ
Выражение затрат стоимости или труда С на возведение анкернабрызг-бетонной крепи в расчете на один метр тоннеля записывают в виде
, (1)
где Lв—периметр контура выработки, м; (, (, (—приведенные коэффициенты себестоимости (трудозатрат) по возведению крепи принимают по ЕНиР.
Слагаемые в скобках определяют затраты:
первое—на бурение шпуров под анкеры; второе—на установку анкеров; третье—на возведение набрызгбетонного покрытия.
Для решения задачи оптимизации рекомендуется пользоваться программой “Комбинированная крепь” (см. приложение 10).
Для определения себестоимости S, руб., при оптимальных параметрах крепи из набрызгбетона и железобетонных анкеров, устанавливаемых в грунтах с коэффициентом крепости f от 3 до 10 разной трещиноватости (характеризуемой коэффициентом Кт) в выработках пролетом В от 3 до 12 м рекомендуется использовать номограммы, приведенные на рисунке, стр. 122—123.
Например, в породах с f=6, Кт=2,5 и для выработки пролетом В=3 м оптимальной является конструкция из анкеров длиной l=l,5 м, установленных с шагом а=0,85 м и набрызгбетонного покрытия толщиной h=6 см.
Приложение 20
Рекомендуемое
ОПТИМИЗАЦИЯ ПАРАМЕТРОВ АРОЧНО-НАБРЫЗГБЕТОННОЙ ОБДЕЛКИ
Оптимизируется конструкция, в которой металлические арки являются армирующим элементом набрызгбетонной обделки.
Общая структура функций цели V определяется объемом работ, связанных с сооружением арочно-набрызгбетонной крепи
V=V1+V2+V3+V4, (1)
где объемы V1, V2, V3, V4 определяются технико-экономическими показателями, соответственно изготовления арок, их установки, обеспечения набрызгбетоном гарантированного контакта, нанесения набрызгбетонного заполнения.
При этом основными функциями цели являются функции стоимости Sк и металлоемкости М, которые определяются по формулам
, (2)
, (3)
где а—шаг арок; h—толщина покрытия из набрызгбетона; N—номер профиля арки; S1, S2, S3, S4—коэффициенты, характеризующие, соответственно, сметную стоимость изготовления арки, ее установки, обеспечения контакта, нанесения контакта, нанесения набрызгбетона; (—удельная металлоемкость.
Проведя по программе “Рак” (см. приложение 10) серию расчетов для арок, изготовленных из различных профилей, можно определить шаг арок, согласно которому выбирается в соответствии с п. 3.30 настоящих Норм необходимая толщина набрызгбетона.
Затем вычисляют Sк и Ми, сопоставляя по ним различные варианты сочетаний N, a, h, выбирают оптимальную по стоимости или металлоемкости конструкцию.
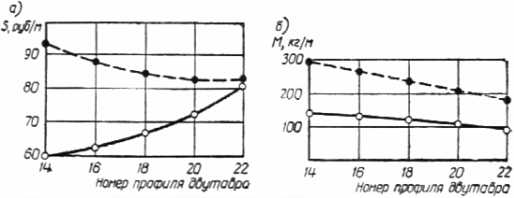
Пример оптимизации конструкции арочно-набрызгбетонной
крепи по сметной стоимости (а) и металлоемкости (б) в
расчете на 1 м штольни:
с гарантированным контактом арок с поверхностью выработки;
то же без гарантированного контакта
В качестве примера рассмотрим оценочные показатели крепления выработки транспортной штольни высотой 4,5 м и пролетом 5 м, заложенной в грунте с коэффициентом крепости f=2.
На графиках (рисунок) приведены зависимости суммарной сметной стоимости S и металлоемкости М комбинированной конструкции крепления от профиля двутавра, из которого изготовлены арки.
Анализ этих графиков указывает на целесообразность устройства гарантированного контакта арок с поверхностью выработки. В этом случае металлоемкость крепи существенно уменьшается, а стоимость, несмотря на тенденцию к увеличению с ростом мощности двутавров, остается также ниже, чем при контакте в отдельных местах.
Рост стоимости при гарантированном контакте обусловлен возрастанием стоимости бетонных работ в этом типе обделки. Очевидно, при этом, что наибольший эффект достигается при использовании двутавров с небольшими номерами сечения (до № 20).
При невозможности устройства контакта по всему периметру арки экономически целесообразными становятся более мощные двутавры.
Приложение 21
Справочное
РАСЧЕТ АРОЧНОЙ КРЕПИ
Параметры конструкции арочной крепи следует определять из условии прочности и устойчивости при действии расчетных нагрузок от давления горных пород (первая группа предельных состояний).
Величину и характер распределения нагрузок на арку следует принимать по результатам измерений в условиях строящегося тоннеля пли в аналогичных условиях. При отсутствии указанных данных нагрузки определяют в зависимости от возможности образования свода обрушения или отдельных вывалов, если исключена возможность давления полного столба налегающих пород.
Интенсивность нормативных вертикальной q и горизонтальной р нагрузок на крепь принимается в зависимости от состояния грунтов:
для слаботрещиноватых
q=0,28 ( K ( (B; р=0; (1)
для трещиноватых
q=0,54 ( K ( (В; р=0,136 к (Hст; (2)
для сильнотрещиноватых
q=0,65 ( K ( (В; р=0,164 к (Hст; (3)
для раздробленных
q=0,9 (B; ; (4)
для нескальных пород при сводообразовании
; ;
; ; (5)
без сводообразования
q1=1,1(H; q2=0,81q1; p1=1,2( ( (h + 0,5H)tg2(; p2=0,66p1. (6)
Для скальных грунтов с коэффициентом крепости в куске f(4 нормативные нагрузки следует принимать в зависимости от трещиноватости грунтов (табл. 1).
Для нескальных и сильнотрещиноватых и раздробленных скальных грунтов интенсивность нормативных вертикальной qн и горизонтальной рн равномерно распределенных нагрузок следует определять по формулам:
; (7)
; (8)
где (=arctg f — угол внутреннего трения в грунте.
Таблица 1
№
п/п |
Грунты |
Возможные варианты загружения |
1 |
|
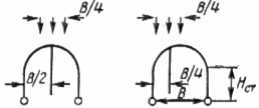
|
2 |
Скальные |
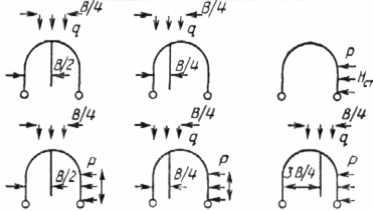
|
3 |
|
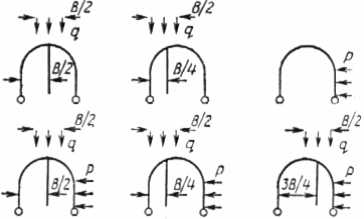
|
4 |
|
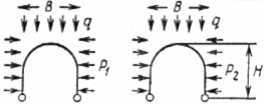
|
5 |
Нескальные |
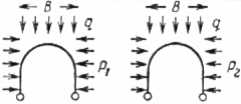
|
6 |
|
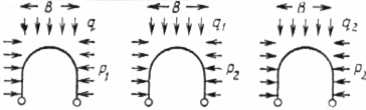
|
Если приведенная высота свода обрушения или возможного вывала превышает половину расстояния от шелыги свода до поверхности или до слоя слабых неустойчивых грунтов, то интенсивность нормативных вертикальной и горизонтальной равномерно распределенных нагрузок следует определять но формулам:
; (9)
, (10)
где (i—удельный вес грунта i-го напластования; Hi—толщина i-го напластования; п—число напластований; (—угол внутреннего трения грунта в окрестности выработки.
Расчетные нагрузки следует определять путем умножения величины нормативной нагрузки на коэффициент надежности, принимаемый по табл. 2.
Таблица 2
| | | | |
Нагрузка от |
Возможные вывалы в грунтах |
Образование свода |
Полный столб |
горного давления |
размокаемых, выветриваемых |
неразмокаемых, не выветриваемых |
нарушения |
налегающих грунтов |
Вертикальная |
1,3 |
1,0 |
1,3 |
1,0 |
Горизонтальная |
1,3 |
1,0 |
1,5 |
1,1 |
Статический расчет арок ведут на заданные нагрузки с учетом отпора грунта.
Коэффициент упругого отпора грунта К при расчете арок допускается принимать постоянным по всему контуру выработки, за исключением пят арок. Величину отпора грунта определяют по данным испытаний (штамповых или прессиометрических) или принимают по аналогии. При этом следует учитывать качество забутовки между аркой и поверхностью выработки с помощью соотношения
K=(Ko, (11)
где Kо—известный коэффициент отпора, полученный для данных условий применительно к монолитной обделке; (—коэффициент, учитывающий толщину забутовки rк, определяемый по графику (рисунок).
Коэффициент упругого отпора грунта под пятами арок Kп определяют по формуле
, (12)
где ha—полная длина арки; Bп—ширина подошвы пяты арки.
При известном модуле деформации массива горных пород Ео и коэффициенте Пуассона ( коэффициент отпора определяют по формуле
, (13)
где —приведенный радиус выработки; So—площадь поперечного
сечения выработки.
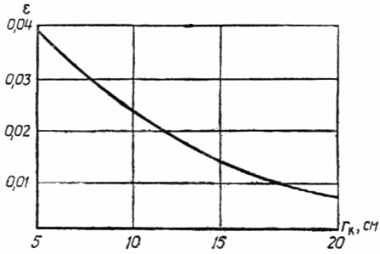
Зависимость коэффициента ( от толщины забутовки rк
Статический расчет арки крепления следует производить для каждого возможного в данных условиях варианта загружения (см. табл. 1) на единичную вертикальную нагрузку qo=1 и соответствующую ей горизонтальную нагрузку Po.
В качестве расчетной схемы следует принимать схему с шарнирами в пятах. Наличие других шарниров определяется конструкцией арки. По результатам статического расчета должны быть определены величины нормальных сил Ni и изгибающих моментов Mi от единичной нагрузки в каждом i-м сечении арки.
Расчетным состоянием конструкции арки следует считать такое, при котором одно из ее сечений переходит в предельное состояние.
Предельное состояние сечения стальной арки надлежит определять согласно требованиям главы СНиП по проектированию стальных конструкций.
Несущую способность i-го сечения следует определять решением относительно величины qi из следующего уравнения:
, (14)
где Fi— площадь i-гo поперечного сечения арки; — пластический момент сопротивления i-го сечения арки для двутавра =1,12Wi, где Wi,— упругий момент сопротивления; Rа— предел прочности материала арки.
Максимальная вертикальная нагрузка, которую способна нести арка qmах определяется соотношением max q = min qi (i = 1, 2, 3, ..., n).
Шаг арок а определяют из соотношения
, (15)
где qp—расчетная нагрузка для данных условий нагружения.
Пример. Определить шаг арок из двутавра № 27 временной крепи с деревянной затяжкой в однопутном железнодорожном тоннеле пролетом B=6,6 м и высотой 8,6 м в грунтах крепостью f=2 коэффициентом отпора K=40 кг/см3.
В результате расчета по программе “RAK” (см. приложение 10) получаем: шаг арок a=0,71 м; наиболее напряженное сечение находится в шелыге свода арки.
Приложение 22
Справочное
РЕКОМЕНДАЦИИ ПО УСТРАНЕНИЮ ВОЗМОЖНЫХ ДЕФЕКТОВ В ОБДЕЛКЕ ИЗ НАБРЫЗГБЕТОНА
Объект |
Признаки |
Необходимые мероприятия |
наблюдения |
появлении дефекта |
по усмотрению производителя работ |
с привлечением проектирующих организаций |
Лоб забоя или грунт вблизи лба забоя |
Потеря устойчивости лба забоя |
Сокращение величины заходки, крепление лба забоя набрызг-бетоном |
Уменьшение сечения выработки в проходке, разработка лба забоя с центральным ядром грунта, крепление лба забоя анкерами и т. п., химическое закрепление грунтов, опережающая забивная крепь, секционный трубчатый экран и т. д. |
|
Появление вывалов |
Ускорение операции разработки грунта и немедленное нанесение набрызгбетона |
Установка противообвальных средств (забивная крепь, секционный трубчатый экран), установка стальной арочной крепи, химическое закрепление грунтов |
|
Появление или усиление водопритока в забой |
Использование добавок—ускорителей схватывания и твердения, для повышения сопротивляемости размыву |
Водопонижение (бурение дренажных скважин, глубинное водопонижение, водопонижение через иглофильтры). Химическое закрепление грунтов |
|
Смещение стен |
Немедленные замыкания обратного свода, крепление обратного свода набрызгбетоном |
Увеличение числа анкеров. Химическое закрепление грунтов |
|
Пучение подошвы выработки |
Ускорение набрызгбетонирования обратного свода |
Анкерное крепление обратного свода, сокращение длины уступа |
Набрызг-
бетон |
Выпучивание или отслаивание набрызгбетона |
Немедленное набрызг-бетонирование после разработки грунта, применение арматурной сетки, увеличение толщины набрызгбетона |
Установка анкеров или дополнительных анкеров |
|
Появление трещин и разрушений сдвиговых |
Применение арматурной сетки, применение дисперсно-армированного набрызгбетона |
Установка дополнительных удлиненных анкеров, установка арок (при необходимости податливых), нарезка прорезей в набрызгбетоне |
Анкеры |
Прогибы опорных пластин, разрыв анкеров |
Увеличение способности анкеров к деформациям—установка упругих прокладок между опорными пластинами |
Установка дополнительных удлиненных анкеров, использование высокопрочных анкеров |
Арочная крепь |
Искривление арок |
Роспуск болтов в соединениях сегментов для обеспечения податливости крепи |
Установка дополнительных удлиненных анкеров, использование податливых арок и прорезей в набрызгбетоне |
Просадки на поверхности и в массиве |
Значительная просадка поверхности и деформация выработки, нарастание скорости развития деформации |
Применение опережающего крепления грунта с удлиненным секционным трубчатым экраном, сокращение промежутка времени между разработкой грунта и креплением, сокращение величины заходки и немедленное поддержание свода выработки |
Уменьшение дополнительных удлиненных анкеров, использование податливых арок и прорезей в набрызгбетоне |
Деформация внутри массива |
Возрастание деформации внутри массива, расширение границы зоны разрушения грунта |
Сокращение периода между разработкой и креплением грунта, уменьшение срока установки анкеров, ускоренное замыкание обратного свода |
Установка анкеров или дополнительных удлиненных анкеров, установка арок, уменьшение длины уступа, переход на проходку минимальным обратным сводом в калотте, нагнетание раствора за крепь или химическое закрепление грунтов |
Деформация сечения выработки |
Увеличение деформаций поперечного сечения выработки, рост скорости их развития |
Сокращение периода времени между разработкой и креплением грунта, ускорение срока установки анкеров, повышение способности анкеров к деформациям—применение упругих прокладок между опорными пластинами анкеров |
Установка дополнительных удлиненных анкеров, уменьшение длины уступа, переход на проходку минимальным уступом или с временным обратным сводом в калотте, нарезка прорезей в случае образования трещин в набрызгбетоне |
|