ГОСУДАРСТВЕННЫЙ КОМИТЕТ СССР
ПО ДЕЛАМ СТРОИТЕЛЬСТВА (ГОССТРОЙ СССР)
ИНСТРУКЦИЯ
по проектированию, изготовлению и применению
конструкций и изделий из арболита
Утверждена
постановлением Государственного комитета СССР
по делам строительства от 4 мая 1982 г. № 116
Содержит основные положения по проектированию, изготовлению и применению изделий из арболита.
Приведены нормативные и расчетные характеристики, методы расчета арболитовыхконструкций на сжатие, изгиб и изгибаемых элементов по деформациям. Изложены общие вопросы технологии производства изделий из арболита; даны требования к материалам, правила назначения составов арболита, их приготовления, формования, твердения, приемки, транспортирования и контроля качества готовых изделий.
Для специалистов проектных институтов и конструкторских бюро, а также для инженерно-технических работников заводов - изготовителей изделий и конструкций из арболита.
Разработана НИИЖБом Госстроя СССР с участием ПТПО «Сельстройматериалы» Росколхозстройобъединения и ВНИИДрева Минлесбумпрома СССР. Использованы материалы ЦНИИЭПсельстроя Минсельстроя СССР, московского лесотехнического института Минвуза СССР, Горьковского инженерно-строительного института Минвуза СССР, НИИСФ Госстроя СССР, Гипростроммаша Минстройдормаша.
Редакторы - инж. П.А. Демянюк, канд. техн. наук И.В. Белый, инж. И.Д. Бабкин (Госстрой СССР), д-р техн. наук И.Е. Путляев, кандидаты техн. наук В.И. Савин, А.А. Кудрявцев, Г.Е. Колосов (НИИЖБ Госстроя СССР).
|
Строительные нормы |
СН 549-82 |
Государственный
комитет СССР
по делам строительства
(Госстрой СССР) |
Инструкция
по проектированию,
изготовлению и
применению конструкций и изделий из арболита |
( |
1. Общие положения
1.1. Требования настоящей Инструкции необходимо соблюдать при проектировании, изготовлении и применении конструкций и изделий из одной разновидности арболита ( бетона цементного на измельченной древесине (дробленке).
1.2. Конструкции изделия из арболита (именуемые в дальнейшем конструкции) применяются в качестве:
панелей и блоков наружных и внутренних стен;
плит перекрытий и покрытий;
панелей перегородок;
теплоизоляционных плит в ограждающих конструкциях.
1.3. Конструкции из арболита разделяются:
по назначению ( на теплоизоляционные, конструкционно-теплоизоляционные и конструкционные;
по армированию ( на армированные и неармированные;
по количеству слоев ( на однослойные и многослойные.
Примечание: Конструкции с наружным и внутренним отделочными слоями по цементно-песчаного раствора толщиной до 2 см относятся к однослойным.
1.4. Конструкции из арболита должны удовлетворять требованиям соответствующих стандартов и рабочих чертежей. Испытание арболита и конструкций из него должно производиться по ГОСТ 19222(73.
1.5. Изготовление конструкций из арболита должно производиться по утвержденным в установленном порядке технологическим картам, составленным применительно к условиям конкретного производства, сырья и вида конструкций.
1.6. При изготовлении, транспортировании и монтаже конструкций из арболита следует соблюдать правила техники безопасности в строительстве, а также правила противопожарной техники.
1.7. Панели и блоки наружных и внутренних стен из арболита предназначаются для жилых, общественных, промышленных и сельскохозяйственных зданий с относительной влажностью воздуха помещений не более 75 %, при отсутствии в них агрессивных сред и систематическом воздействии температур не выше 50(С и не ниже минус 40(С. Допускается применять ограждающие конструкции из арболита в животноводческих зданиях со слабоагрессивной средой при устройстве на внутренних поверхностях этих конструкций пароизоляционного слоя, который должен предусматриваться рабочими чертежами.
Степень агрессивного воздействия газовых сред и меры защиты должны приниматься согласно главе СНиП по защите строительных конструкций от коррозии (как для конструкций из бетонов на пористых заполнителях).
1.8. Плиты покрытий и перекрытий из арболита допускается применять в зданиях различного назначения с относительной влажностью воздуха помещений не более 60 % и при отсутствии агрессивных сред только в виде составных конструкций в сочетании с железобетоном.
1.9. Арматуру в конструкциях из арболита необходимо защищать антикоррозионными покрытиями в соответствии с Инструкцией по изготовлению изделий из ячеистого бетона.
Внесена
НИИЖБом
Госстроя СССР |
Утверждена постановлением Государственного комитета СССР по делам строительства
от 4 мая 1982 г. № 116 |
Срок введения
в действие
1 января 1983 г. |
1.10. Наружная поверхность конструкций из арболита, соприкасающаяся с атмосферной влагой, независимо от влажностного режима помещений, должна иметь отделочный (фактурный) слой, обеспечивающий защиту арболита от увлажнения.
2. Требования к исходным материалам,
арболиту и конструкциям из него
2.1. Для изготовления конструкций из арболита применяются следующие материалы:
вяжущее (портландцемент и его разновидности), заполнители (отходы лесозаготовок, лесопиления и деревообработки, одубина), химические и порообразующие добавки (хлорид кальция, жидкое стекло, сернокислый алюминий и др.), арматура, материалы для антикоррозионной защиты арматуры и отделки поверхностей конструкций.
2.2. Вяжущие должны удовлетворять требованиям следующих стандартов:
портландцемент и быстротвердеющий портландцемент ГОСТ 10178(76;
цемент сульфатостойкий ГОСТ 22266(76;
портландцемент белый ГОСТ 965(78;
портландцемент цветной ГОСТ 15825(80.
2.3. Заполнители готовятся из органического древесного технологического сырья путем дробления и рассева.
2.4. Заполнители должны приготовляться из следующих пород древесины: ели, сосны, кедра, пихты. Допускается использовать березу, ольху, липу, тополь, осину и другие породы древесины, а также их смеси после лабораторной проверки при соблюдении требований п. 2.12.
2.5. Технологическое древесное сырье поставляется на предприятие как отдельно по породам, так и в смешанном виде в различных соотношениях.
Диаметр заготовок сырья в круглом виде устанавливается от 5 до 15 см. Сырье заготовки диаметром более 15 см подлежит расколке на части, наибольшая линия раскола по торцу которого не должна превышать 15 см.
2.6. В технологическом сырье допускаются пороки древесины (по ГОСТ 2140(71), в том числе гниль внутренняя заболонная мягкая и наружная трухлявая, если она занимает не более 5% площади торца дровяного сырья или 5% общего объема партии. Гниль превышающую указанные количества, необходимо удалить.
2.7. Дрова и кусковые отходы укладывают, принимают и учитывают в соответствии с ГОСТ 3243(46 (с изм. № 2). Древесное технологическое сырье в круглом виде хранится в соответствии с ГОСТ 9014.0(75 (с изм. № 1).
2.8. Кусковые отходы древесины должны измельчаться в щепу и выдерживаться в кучах под навесом не менее месяца при положительной температуре.
Применение свеже срубленной древесины всех пород для производства арболита допускается при соблюдении требований п. 2.12.
2.9. Выдержанные отходы древесины превращают в щепу на рубильных машинах, а затем измельчают в дробленку на молотковых мельницах, дробилках или стружечных станках.
2.10. При дроблении и рассеве необходимо применять древесину равновесной относительной влажности не более 30%, при влажности выше этого предела нарушается нормальная работа дробилок, сит и грохотов.
2.11. Технологическая щепа при постановке по размерам частиц и показателям засоренности должна соответствовать требованиям ГОСТ 15815(70, предъявляемым к щепе, используемой для производства древесно-волокнистых плит.
2.12. Дробленка должна удовлетворять требованиям ГОСТ 19222(73, а также следующим требованиям:
показатель пригодности (удельный расход цемента на единицу прочности арболита при сжатии) должен быть не более 15;
содержание водо-растворимых редуцирующих веществ должно быть не более 2%.
2.13. Химические добавки для арболитовой массы должны удовлетворять требованиям следующих стандартов:
хлорид кальция ГОСТ 450(77;
жидкое стекло ГОСТ 13078(67;
силикат-глыба ГОСТ 13079(67;
сернокислый глинозем ГОСТ 5155(74;
окись кальция (известь) ГОСТ 9179(77.
Допускается введение порообразующих добавок, используемых при производстве поризованных легких бетонов, а также других химических добавок, в том числе комплексных, после лабораторной проверки по согласованию с базовой организацией ( НИИЖБ Госстроя СССР.
2.14. Химические добавки для арболитовой массы применяются в виде водных растворов требуемой плотности как в отдельности, так и в сочетании друг с другом. Плотность замеряется денсиметром.
2.15. Жидкое стекло должно иметь модуль от 2,4 до 3. Модуль жидкого стекла определяется по ГОСТ 13078(67. Для быстрой предварительной оценки модуля жидкого стекла может быть применен полевой способ согласно Инструкции по технологии приготовления жаростойкого бетона.
2.16. Вода для затворения арболитовых смесей и бетона (раствора) отделочных слоев должна удовлетворять требованиям ГОСТ 23732(79.
2.17. Для армирования конструкций из арболита должна применяться арматура классов А-I, А-II и А-III диаметром не более 16 мм и проволочная арматура класса Вр-I. Арматурные изделия и закладные металлические детали должны удовлетворять требованиям ГОСТ 19222(73 и ГОСТ 10922(75, а также дополнительным указаниям, приведенным в рабочих чертежах конструкций. Арматура должна иметь заводской сертификат с указанием марки стали. Применение арматурных изделий и закладных металлических деталей со следами ржавчины, грязи и масла не допускается.
2.18. Заполнители для бетона (раствора) наружных и внутренних отделочных слоев конструкций из арболита должны соответствовать требованиям:
плотный песок ГОСТ 8736(77;
плотный щебень или гравий ГОСТ 8267(75 и ГОСТ 8268(82;
неорганические (пористые мелкий и крупный заполнители ГОСТ 9757(73.
Предельная крупность щебня или гравия принимается 20 мм при толщине бетонного слоя более 30 мм и 10 мм при толщине бетонного слоя до 30 мм.
3. Проектирование конструкций из арболита
3.1. Стеновые блоки и панели из арболита, как правило, должны выполняться однослойными с наружным отделочным слоем из декоративного бетона или раствора на плотных минеральных заполнителях, рис. 1, в.
Минимальная толщина однослойных элементов из арболита должна определяться расчетом и во всех случаях быть не менее 8 см.
Размеры сечений сжатых элементов стен принимаются такими, чтобы отношение l/h не превышало значений, указанных в табл. 5.
3.2. Стеновые блоки и панели из арболита для повышения их несущей способности могут проектироваться слоистыми, рис. 1, а.
Блоки перемычки (при блочной разрезке стен) или стеновые панели-перемычки, на которые опираются перекрытия, должны проектироваться слоистыми, рис. 1, б.
В слоистых блоках и панелях слои должны выполняться из бетона цементного на плотных или пористых заполнителях классов по прочности на сжатие В15(В25.
Рабочая арматура в слоистых блоках и панелях должна выполняться в виде сварных сеток или каркасов из стали класса Вр-1 и располагаться в бетонных слоях.
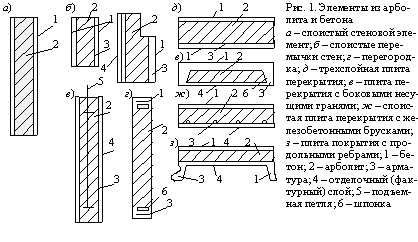
3.3. Панели-перегородки зданий из арболита, как правило, должны проектироваться однослойными. Для повышения их несущей способности (при воздействии на них транспортных и монтажных нагрузок) они должны проектироваться с боковыми железобетонными гранями из тяжелого или мелкозернистого бетона класса по прочности на сжатие В15(В25 (рис. 1, г).
3.4. Для плит покрытий и перекрытий арболит применяется в сочетании с тяжелым, легким или мелкозернистым бетоном класса по прочности на сжатие В15-В25, в котором должна располагаться рабочая арматура.
Конструктивные решения таких элементов приведены на рис. 1, д(з. Толщина защитного слоя бетона в конструкциях составного сечения должна приниматься в соответствии с нормами проектирования бетонных и железобетонных конструкций.
3.5. В конструкциях плит покрытий и перекрытий во всех случаях в сжатой зоне должен предусматриваться слой толщиной не менее 20 мм из тяжелого, легкого или мелкозернистого бетона.
Класс арболита по прочности на сжатие принимается в пределах В1,5(В3,5 в зависимости от типа конструкций.
3.6. Плиты перекрытий зданий, как правило, должны проектироваться в виде трехслойных элементов (рис. 1, д).
Толщину нижнего железобетонного слоя следует принимать из условия расположения в нем арматуры с обеспечением необходимых защитных слоев. Толщина верхнего бетонного слоя должна назначаться исходя из расчета на прочность плит (см. п. 3.39).
Класс арболита по прочности на сжатие для таких плит должен приниматься не менее В2.
В случае если совместная работа слоя в трехслойных конструкциях перекрытий не обеспечивается (см. п. 3.40), плиты перекрытий должны проектироваться с боковыми несущими гранями (рис. 1, е). Ширина боковых граней принимается из условий размещения рабочей арматуры в бетоне с обеспечением необходимых защитных слоев при изготовлении элементов.
Допускается рабочую арматуру в плитах перекрытий располагать в бетонных брусках или вкладышах (рис. 1, ж).
Примечание: Плиты перекрытий с боковыми несущими гранями, а также панели-перегородки с железобетонными гранями (п. 3.3) допускается изготовлять в следующем порядке. В подготовленную форму к продольным ребрам закрепляются съемные инвентарные вкладыши на всю длину элемента. После укладки и уплотнения арболита борта форму закрывают, вкладыши удаляются и борта вновь закрывают. В образовавшиеся продольные пазы укладывают арматурные каркасы и пазы заполняют бетонной смесью.
3.7. Плиты покрытий зданий следует проектировать ребристыми (рис. 1, з). Толщина арболитового слоя в таких плитах назначается исходя из теплотехнического расчета. Высота ребер назначается из условия обеспечения достаточной жесткости плит. Арматура в верхнем слое не предусматривается.
3.8. Монтажные (подъемные) петли для всех видов конструкций из арболита следует выполнять в соответствии с действующим ГОСТ на легкобетонные изделия.
В однослойные элементы подъемные петли закладывают на глубину не менее 50 диаметров стержня; при этом на концах заделываемые подъемные петли должны иметь крюки, заводимые за арматурные элементы (сетки) или приваренные стержни, пластины и т. д.
Подъемные петли в элементах составных сечений должны быть заанкерены в бетонных слоях или в бетонных несущих гранях и во всех случаях заведены за арматурные каркасы или сетки.
Стальные закладные изделия, анкерные стержни и арматурные каркасы, а также соединительные накладки, применяемые для соединения конструкций из арболита, должны быть защищены от коррозии в соответствии с Инструкцией по изготовлению изделий из ячеистого бетона.
Нормативные и расчетные характеристики арболита
3.9. Класс арболита по прочности при сжатии (В) представляет собой гарантированную прочность арболита.
Средняя фактическая прочность арболита на сжатие, МПа, соответствующая его классу, назначается равной
Rcж = 1,43В (1)
и контролируется по действующим государственным стандартам на образцах 150(150(150 мм.
3.10. Для конструкций из арболита предусматриваются следующие классы арболита по прочности на сжатие:
В0,5; В7,75; ( для теплоизоляционных;
В1; В1,5; В2; В2,5; В3 и В3,5 ( для конструкционных.
3.11. Нормативными сопротивлениями арболита являются:
сопротивление осевому сжатию призм (призменная прочность), Rbk;
сопротивление осевому растяжению, Rbtk.
3.12. Нормативная призменная прочность арболита при его средней естественной влажности по массе 15(20 % принимается равной
Rbk = 0,78В (2)
Нормативные сопротивления арболита Rbk (с округлением) в зависимости от класса арболита по прочности на сжатие при средней естественной влажности по массе 15-20 % даны в табл. 1.
3.13. Нормативное сопротивление арболита осевому растяжению Rbtk принимается в зависимости от класса арболита по прочности на сжатие согласно табл. 1.
Таблица 1
Вид
сопротивления |
Обозначение |
Нормативные сопротивления арболита Rbk и Rbtk, расчетные сопротивления предельных состояний второй группы Rb(ser и Rbt(ser при классе арболита по прочности на сжатие |
|
|
В0,5 |
В0,75 |
В1 |
В1,5 |
В2 |
В2,5 |
В3 |
В3,5 |
Сжатие осевое (призменная прочность)
Растяжение осевое |
Rbk и Rbk,ser
Rbtk и Rbtk,ser |
0,39
4
0,13
1,33 |
0,58
5,92
0,2
2,04 |
0,78
7,95
0,25
2,55 |
1,17
11,9
0,36
3,67 |
1,56
15,9
0,48
4,9 |
1,95
19,9
0,57
5,82 |
2,33
23,8
0,67
6,8 |
2,73
27,3
0,74
7,5 |
Примечание: Над чертой указаны значения в МПа, а под чертой ( кгс/см2.
3.14. Расчетные сопротивления арболита при расчете по предельным состояниям первой группы определяются путем деления нормативных сопротивлений на соответствующие коэффициенты надежности по арболиту
и , (3)
где (bc и (bt коэффициенты надежности по арболиту, приготовленному на древесной дробленке, при сжатии и растяжении соответственно принимаемые как для тяжелого бетона по главе СНиП по проектированию бетонных и железобетонных конструкций.
Расчетные сопротивления арболита на древесной дробленке приведены в табл. 2.
Таблица 2
Вид
сопротивления |
Обозначение |
Расчетные сопротивления арболита для предельных состояний первой группы Rb и Rbt, при классе арболита по прочности на сжатие |
|
|
В0,5 |
В0,75 |
В1 |
В1,5 |
В2 |
В2,5 |
В3 |
В3,5 |
Сжатие осевое (призменная прочность)
Растяжение осевое |
Rb
Rbt |
0,3
3,06
0,087
0,89 |
0,45
4,6
0,13
1,33 |
0,6
6,1
0,17
1,73 |
0,9
9,18
0,24
2,45 |
1,2
12,2
0,32
3,26 |
1,5
15,3
0,38
3,87 |
1,8
18,3
0,44
4,53 |
2,1
21,4
0,57
5,78 |
Примечание: Над чертой указаны значения в МПа, а под чертой ( кгс/см2.
В случаях, указанных в п. п. 3.15 расчетные сопротивления Rb и Rbt следует умножать на соответствующие коэффициенты условий работы арболита.
3.15. Для случаев, указанных ниже, при расчете конструкций расчетные сопротивления арболита, принимаемые по табл. 1 и 2, следует умножать на коэффициенты условий работы (bi имеющие следующие значения:
для арболита, приготовленного методом вертикального прессования или трамбования, (bi = 0,85;
для арболита, укладываемого в вертикальные формы (кассеты) на высоту более 50 см, независимо от способа уплотнения (bi = 0,9;
для простенков и блоков сечением менее 0,15 м2 (bi = 0,8;
для всех элементов при расчете прочности на монтажные нагрузки при влажности арболита выше 20% (bi = 0,8.
3.16. Марки по плотности (объемной массе) арболита и конструкциях в высушенном до постоянной массы состоянии, указываемые в рабочих чертежах, не должны превышать значений, приведенных в табл. 3.
Таблица 3
|
Марки по плотности арболита, кг/м2 |
Класс арболита |
на древесной дробленке из отходов |
по прочности
на сжатие |
лесопиления
и
деревообработки |
лесозаготовок |
В0,5
В0,75
В1
В1,5
В2
В2,5
В3
В3,5 |
450
500
600
650
650
700
750
800 |
500
500
600
700
750
750
800
850 |
При определении нагрузок плотность (объемная масса) арболита принимается с учетом влажности. Установившаяся влажность для конструкций из арболита принимается в соответствии с главой СНиП по строительной теплотехнике, влажность арболита в конструкциях при распалубке ( 35 %, а при отпуске конструкций потребителю ( не более 25 % (по массе).
3.17. Величина начального модуля упругости арболита Ев принимается по табл. 4.
Таблица 4
Плотность (объемная масса) арболита при средней естественной влажности |
Начальные модули упругости арболита
при сжатии и растяжении Rb
при классе арболита
по прочности на сжатие |
по массе 15-20% |
В0,5 |
В0,75 |
В1 |
В1,5 |
В2 |
В2,5 |
В3 |
В3,5 |
400
500
600
700
800 |
250
2550
340
3470
440
4480
500
5100
580
5900 |
300
3060
410
4180
510
5200
590
6000
680
6940 |
(
500
5100
600
6120
700
7140
800
8150 |
(
620
6320
750
7650
900
9170
1050
10700 |
(
(
1000
10200
1150
11700
1400
14300 |
(
(
1300
133001500
153001700
17300 |
(
(
(
1820
1850
2000
20400 |
(
(
(
2140
218002300
23800 |
Примечание: Над чертой указаны значения в МПа, под чертой ( кгс/см2.
3.18. Начальный коэффициент поперечной деформации арболита (коэффициент Пуассона) принимается равным 0,2.
3.19. Марка бетона (раствора) наружных отделочных слоев по морозостойкости должна соответствовать главе СНиП по проектированию бетонных и железобетонных конструкций и указываться в рабочих чертежах.
3.20. Марка арболита и бетона (раствора) наружных отделочных слоев по морозостойкости должна соответствовать указанной в рабочих чертежах и быть не менее:
Мрз 25 ( для конструкций, применяемых в зданиях с относительной влажностью воздуха помещений не более 60 %;
Мрз 35 ( для конструкций, применяемых в зданиях с относительной влажностью воздуха помещений от 60 до 75 %;
Мрз 50 ( для конструкций, применяемых в зданиях с относительной влажностью воздуха помещений свыше 75 %, а также для бетона (раствора) наружного отделочного слоя.
Основные расчетные положения
3.21. Конструкции из арболита следует рассчитывать по несущей способности (по предельным состояниям первой группы) на воздействие расчетных нагрузок с учетом расчетных сопротивлений арболита и арматуры.
Изгибаемые элементы, кроме того, рассчитываются по деформациям на воздействие нормативных нагрузок, а конструкции составного сечения ( по деформациям и раскрытию трещин (по предельным состояниям второй группы).
3.22. Все конструкции из арболита следует рассчитывать также на усилия, возникающие при распалубливании, транспортировании и монтаже; при этом собственная масса конструкций принимается с учетом влажности по п. 3.16 настоящей Инструкции, а также с учетом коэффициента динамичности 1,5. Расчетные сопротивления арболита при распалубке и складировании конструкций принимаются равными 70 % нормируемых их значений в 28-дневном возрасте.
3.23. Расчет конструкций из арболита, например панелей и блоков, усиленных в необходимых случаях монтажной арматурой, производится по прочности и деформациям как однослойных элементов в соответствии с настоящей Инструкцией. Отделочные (фактурные) слои из раствора толщиной до 2 см у таких элементов при расчете прочности и деформации не учитываются, однако рабочая высота элемента (толщина) принимается с учетом толщины отделочных слоев.
Конструкции составного сечения, например панели покрытий и перекрытий и др., рассчитываются по прочности, деформациям и раскрытию трещин с учетом толщины слоев из бетона по приведенной их площади сечений (см. п. 3.49). При этом расчетные сопротивления бетона и арматуры и их модули упругости принимаются в соответствии с главой СНиП по проектированию бетонных и железобетонных конструкций.
3.24. Ширина раскрытия трещин (в бетоне), нормальных к оси элемента, у конструкций составного сечения при продолжительном действии нагрузки не должна превышать 0,3 мм, а при непродолжительном ( 0,4 мм.
Прогибы всех изгибаемых элементов, определенные с учетом длительного действия нагрузки, не должны превышать значений, указанных в главе СНиП по проектированию бетонных и железобетонных конструкций.
При проектировании изгибаемых элементов составного сечения допускается предусматривать строительный подъем (обратный выгиб) в соответствии с п. 3.50.
3.25. При расчете несущей способности стен из панелей или блоков следует проверить прочность сечения стен в пределах высоты этажа и опорные сечения стен, примыкающие к горизонтальным растворным монтажным швам в уровне перекрытий.
3.26. Максимальную приведенную гибкость l/h несущих и самонесущих стен из панелей и блоков в пределах этажа следует принимать не более указанной в табл. 5.
Таблица 5
Вид стены |
Схема разрезки стены |
l/h |
Из панелей |
Однорядная
Двухрядная |
15
12 |
Из блоков |
Однорядная
Двухрядная
Четырехрядная
Трехрядная |
15
13
9
9 |
Примечание: В табл. 5 и 6 приведенная гибкость равна отношению l/h, где l ( высота этажа, h ( толщина элемента (полная высота сечения).
3.27. Предельные (максимальные) расстояния между температурно-усадочными швами однослойных стен из арболитовых панелей или блоков в отапливаемых и неотапливаемых зданиях принимают в соответствии с действующими нормативными документами как для аналогичных стен из легких бетонов.
3.28. Расчет стен из панелей и блоков, возводимых в зимних условиях, следует производить с учетом требований главы СНиП по проектированию каменных и армокаменных конструкций.
Расчет элементов по предельным состояниям первой группы
Внецентренно-сжатые элементы
3.29. Элементы стен (панели, блоки) на вертикальные нагрузки рассчитываются как внецентренно-сжатые. При расчете стеновых панелей и блоков следует учитывать случайный эксцентриситет, принимаемый в соответствии с требованиями главы СНиП по проектированию бетонных и железобетонных конструкций, который суммируется с эксцентриситетом продольной силы, получаемым из статического расчета конструкций.
3.30. При расчете однослойных панелей или блоков в пределах каждого этажа приложение усилий от вертикальных нагрузок определяют по следующим правилам:
а) усилие от нагрузки верхних этажей или покрытий (крыши) считают приложенным по оси площади контакта между панелями в горизонтальном шве;
б) усилие от нагрузки перекрытия над данным этажом принимают приложенным на расстоянии 1/3 глубины заделки настила от внутренней грани стены;
в) нагрузку от собственной массы панели перекрытий в пределах рассматриваемого этажа считают приложенной в центре ее тяжести.
3.31. Изгибаемый момент от давления ветра на наружные стены по вертикальному пролету определяют как для разрезных однопролетных балок по известным в строительной механике методам.
3.32. Элементы стен из панелей и блоков однорядной разрезки на вертикальные нагрузки с учетом продольного изгиба рассчитываются из условий, что эксцентриситет продольной силы не должен превышать 0,4 h. Расчет таких элементов стен производится по формуле
, (4)
где Аb ( площадь сечения однослойного элемента;
( ( коэффициент, учитывающий продольный изгиб и длительное воздействие нагрузки, принимаемый по табл. 6;
Таблица 6
Nдл |
Значения ( при l/h |
N |
4 |
6 |
8 |
10 |
12 |
14 |
15 |
0
0,5
1 |
1
0,95
0,8 |
1
0,85
0,72 |
0,9
0,77
0,63 |
0,83
0,7
0,55 |
0,76
0,63
0,47 |
0,7
0,57
0,38 |
0,66
0,55
0,35 |
Примечание. Nдл ( длительно действующая нагрузка;
N ( общая нагрузка на элемент.
eo ( эксцентриситет продольной силы, определяемый по главе СНиП по проектированию бетонных и железобетонных конструкций.
Для промежуточных значений l/h величина ( определяется по интерполяции.
Применение сжатых конструкций с l/h > 15 не допускается.
3.33. При определении коэффициента ( расчетную длину (высоту) стен l принимают в соответствии с главой СНиП по проектированию бетонных и железобетонных конструкций.
Если прочность однослойных блоков или панелей, рассчитываемых по формуле (4), окажется недостаточной, следует применять трехслойные элементы из арболита и бетона (рис. 1, а). При этом толщина бетонных слоев должна быть принята не менее 3 см с каждой стороны. Трехслойные блоки и панели рассчитывают по формуле (4), в которой значения Rb принимаются с коэффициентом условий работ (bc.
Значения коэффициента (bc необходимо принимать: при классе бетона В 15 ( (bc = 1,3; при классе бетона В 20 ( (bc = 1,4.
3.34. При проверке прочности опорных сечений стены (из панелей или блоков), примыкающих к горизонтальным монтажным швам, влияние контактного шва и глубины опирания плит перекрытий учитывают умножением Rb на коэффициент Km определяемый по формуле
, (5)
где d1 и d2 ( глубина заделки соответственно каждого из перекрытий, опирающихся на стены с обеих сторон; при одностороннем опирании перекрытий на однослойные стены d1 обозначает глубину заделки перекрытия, а d2 ( ширину остальной части заполненного раствором горизонтального шва, за вычетом толщины вертикального шва у торца перекрытия;
d ( толщина однослойной стеновой панели (блока);
В и В’ ( класс арболита и раствора (бетона) соответственно по прочности на сжатие;
К3 ( коэффициент, учитывающий влияние монтажа в зимних условиях на несущую способность стены в любом возрасте; при монтаже стен в зимних условиях К3 = 0,8, в летних условиях К3 = 1.
Если перекрытия не пересекают стену и нагрузка передается через заполненный раствором шов, влияние монтажного шва учитывают формулой (5), принимая d1 + d2 = d.
Указания, приведенные в настоящем пункте, относятся к случаям когда все монтажные швы заполнены раствором и толщина горизонтальных швов не превышает 25 мм, вертикальных ( 50 мм.
Изгибаемые элементы
3.35. Однослойные изгибаемые элементы (неармированные или с монтажной арматурой) рассчитывают по формуле
M ( RbtWpl, (6)
где Wpl ( момент сопротивления, определяемый с учетом неупругих свойств арболита.
Элементы прямоугольного сечения рассчитываются по формуле
, (7)
где Rbt ( расчетное сопротивление арболита при осевом растяжении, принимаемое по табл. 2 настоящей Инструкции;
b и h ( ширина и высота поперечного сечения, см.
3.36. Конструктивную арматуру в однослойном изгибаемом элементе учитывают путем определения дополнительного момента М’ по формулам:
; (8)
, (9)
где Аs ( площадь сечения растянутой арматуры;
Rs ( расчетное сопротивление арматуры класса А-II или Вр-I, в однослойном элементе, принимаемое не выше 180 МПа.
При этом прочность такого изгибаемого элемента проверяется из условия
M ( RbtWpl + M’, (10)
где М ( действующий внешний расчетный изгибающий момент.
3.37. В плитах покрытий и перекрытий, а также в навесных перемычечных стеновых панелях рабочую арматуру необходимо располагать в соответствии с п. 3.2. Конструктивные решения таких элементов приведены на рис. 1.
3.38. Прочность изгибаемых элементов составных сечений рассчитывают по нормальным сечениям и на сдвиг слоев относительно друг друга.
3.39. Прочность изгибаемых составных элементов по нормальным сечениям рассчитывают из условия
. (11)
Положение нейтральной оси (высота сжатой зоны х) определяется из выражения
, (12)
где Аs ( площадь сечения рабочей арматуры, расположенной в бетоне растянутой зоны; ( ширина слоя из бетона, расположенного в сжатой зоне.
При этом во всех случаях должно соблюдаться условие x ( (где толщина верхнего слоя из бетона). Виды и классы бетона слоев и классы арматуры принимаются в соответствии с п. 2.17 и п. 3.2 настоящей Инструкции. Расчетные сопротивления бетона слоев и арматуры принимаются по главе СНиП по проектированию бетонных и железобетонных конструкций.
3.40. Прочность изгибаемых слоистых элементов на сдвиг слоев рассчитывают из условия
. (13)
3.41. Прочность по наклонным сечениям на сдвиг слоев изгибаемых элементов с боковыми несущими гранями (рис. 1, е) рассчитывают по формуле
, (14)
где ( расчетное сопротивление бетона на растяжение, принимаемое в соответствии с главой СНиП по проектированию бетонных и железобетонных конструкций; b ( суммарная ширина боковых граней.
При невыполнении условия (14) в боковых несущих гранях предусматривается поперечная арматура (хомуты), и прочность по наклонным сечениям боковых граней рассчитывают в соответствии с главой СНиП по проектированию бетонных и железобетонных конструкций как для таврового элемента без учета арболита.
Расчет на местное сжатие (смятие)
3.42. Расчет на местное сжатие производится по формуле
N (((locRlocAloc, (15)
где N ( расчетная нагрузка, приложенная к части рассматриваемого сечения (местная или сумма местной и основной нагрузок);
Аloc ( площадь смятия под поверхностью;
(loc ( коэффициент, зависящий от равномерности распределения нагрузки и площади опорной поверхности: (loc = 1 при опирании на выравнивающий слой из раствора и (loc = 0,8 при опирании без выравнивающего слоя;
Rloc ( расчетное сопротивление местному сжатию арболита, определяемое по формуле
Rloc = (bRb, (16)
где (b ( коэффициент, зависящий от места приложения нагрузки на элемент (рис. 2). При схемах а и б (b = 1,5; при схеме в (b = 1,2; при схемах г и д (b = 0,8.
Если прочность однослойных элементов на смятие, рассчитанных по формуле (15), окажется недостаточной, необходимо применять слоистые элементы из арболита и бетона (см. рис. 1, б). При этом толщина бетонного слоя должна быть не менее 3 см.
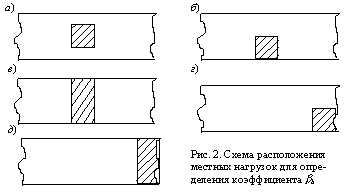
Расчет слоистых элементов на смятие может быть выполнен по формуле (15), в которой значение Rloc принимается с коэффициентами условия работы при классе бетона по прочности на сжатие равными:
В15 (вс = 1,4;
В20 (вс = 1,5;
В25 (вс = 1,6.
Расчет на продавливание
3.43. Расчет на продавливание однослойных плит из арболита от местных нагрузок производится из условия
P ( 0,4Rbtumh0, (17)
где Р ( расчетная продавливающая сила;
um ( среднее арифметическое величин периметров верхнего и нижнего оснований пирамиды, образующейся при продавливании в пределах рабочей высоты сечения h (рис. 3).
um = u1 + u2 + u3 + u4. (18)
При определении величины um предполагается, что продавливание происходит по боковой поверхности пирамиды, меньшим основанием которой служит площадь действия продавливающей силы, а боковые грани наклонены под углом 45( к горизонтали (см. рис. 3).
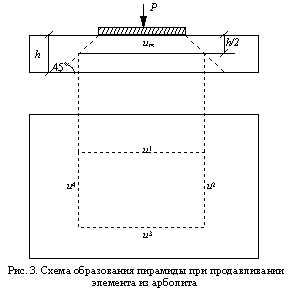
3.44. Одновременно с расчетом на продавливание плиты при больших толщинах (h>15 см) проверяют на прочность по смятию согласно п. 3.42.
Элементы составных сечений, указанные на рис. 1, д(з, следует рассчитывать на продавливание как однослойные плиты по п. 3.43.
Расчет элементов по предельным состояниям второй
группы
Расчет по раскрытию трещин
3.45. При проектировании слоистых элементов перекрытий (см. рис. 1, д), если не соблюдается условие
М ( Rbt,sezWpl (19)
рекомендуется проверять ширину раскрытия трещин в нижнем слое,
где Wpl ( момент сопротивления приведенного сечения (рис. 4), определяемый по формуле
Wpl = (0,292 + 0,075(1 + 0,75(2)bh2. (20)
В формуле (20):
и , (21)
где bf и ( ширина слоя из бетона, расположенного в растянутой и сжатой зоне соответственно;
hf и ( толщина нижнего и верхнего слоя из бетона соответственно.
Размеры приведенного сечения определяются по п. 3.49 и рис. 4.
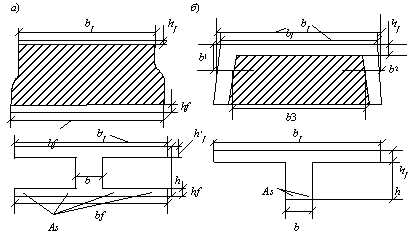
Рис. 4. Схема поперечных сечений составных элементов
а ( трехслойное ; б ( с боковыми несущими гранями 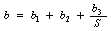
3.46. Ширина раскрытия трещин для слоистого элемента определяется по формуле
, (22)
где (s ( напряжение в арматуре, определяемое по формуле
, (23)
lcz расстояние между трещинами, принимаемое по табл. 7.
Таблица 7
hf, |
lcz при ( = As fAb, % |
см |
0,15 |
0,2 |
0,25 |
0,3 |
0,35 и выше |
2,5
3
4 |
30
25
20 |
25
20
16 |
22
18
15 |
20
16
14 |
17
14
13 |
Ab ( полная площадь поперечного сечения слоистого элемента;
К ( коэффициент, зависящий от класса бетона нижнего слоя (см. п. 3.2), принимаемый:
для бетона класса В15 1;
для бетона класса В20 0,85;
для бетона класса В25 0,7.
( ( коэффициент, зависящий от вида продольной растянутой арматуры, равный:
для стержней периодического профиля класса A-II и A-III ( = 0,7;
для сварных каркасов и сеток из стали класса Bp-I ( = 1,25;
(l ( коэффициент, учитывающий длительное действие нагрузки, определяемый из выражения
, (24)
где Mд ( момент от длительно действующей части нагрузки;
М ( общий момент от кратковременной и длительной нагрузки.
В табл. 7 для промежуточных значений h и ( величина lcz принимается по интерполяции.
Расчет элементов по деформациям
3.47. Прогибы изгибаемых элементов из арболита определяются от нормативных нагрузок по формулам строительной механики в соответствии с требованиями пп. 3.47-3.50. Величины прогибов изгибаемых элементов от кратковременного и длительного действия нагрузок не должны превышать значений, приведенных в главе СНиП по проектированию бетонных и железобетонных конструкций.
3.48. Прогибы однослойных элементов определяют как для сплошного упругопластичного тела с учетом работы арболита сжатой и растянутой зон (без трещин), при этом в расчет вводят полное сечение элемента.
Полная величина прогибов изгибаемого однослойного элемента из арболита при кратковременном и длительном действии нагрузки определяется по формуле:
, (25)
где ( прогиб от кратковременно действующей части нагрузки Мк
; (26)
S ( параметр, зависящий от схемы загружения элемента и определяемый известными в строительной механике методами;
мд ( кратковременный прогиб от длительно действующей части нагрузки, определяемый по формуле (26) при замене в ней Мк на Мд;
(cc,r ( коэффициент, учитывающий влияние длительной ползучести арболита на деформации однослойного элемента, значение которого принимают для арболита на древесной дробленке равным (cc,r = 4.
Примечание. При ограничении прогибов эстетическими требованиями значение прогиба в формуле (25) не учитывается.
3.49. Прогибы изгибаемых элементов составного сечения из арболита и бетона рассчитываются по приведенному сечению (см. рис. 3). При этом составное сечение приводится к однородному из бетона сжатой зоны по коэффициенту приведения .
Значения начальных модулей упругости бетона Eв принимаются в соответствии с главой СНиП по проектированию бетонных и железобетонных конструкций, а арболита ( по табл. 4 настоящей Инструкции.
Полная величина прогибов изгибаемого элемента составного сечения при кратковременном и длительном действии нагрузки определяется по формуле
fм = fмк + fмд(сс,з, (27)
где fмк прогиб от кратковременно действующей части нагрузки (Мк) элемента составного сечения, определяемый по формуле
, (28)
fмд ( кратковременный прогиб от длительно действующей части нагрузки, определяемый по формуле (28) при замене в ней Мк на Мд;
S ( то же, что и в п. 3.48;
(сс,1 и (сс,3 ( коэффициенты, учитывающие влияние кратковременной и соответственно длительной ползучести бетона в элементе составного сечения и принимаемое по табл. 8;
( начальный модуль упругости бетона верхнего слоя в элементе составного сечения, принимаемый по главе СНиП по проектированию бетонных и железобетонных конструкций.
Примечание. При ограничении прогибов эстетическими требованиями значение прогиба fмк в формуле (27) не учитывается.
Таблица 8
| | |
Типы |
Коэффициенты |
элементов |
(сс,1 |
(сс,3 |
Слоистые с верхним слоем из тяжелого или легкого бетона (см. рис. 1, д(з)
То же, с верхним слоем из мелкозернистого бетона
С боковыми несущими гранями из тяжелого или легкого бетона (см. рис. 1, е)
То же из мелкозернистого бетона |
0,4
0,35
0,75
0,65 |
3,2
4,5
3
4,2 |
3.50. В случае если изгибаемые элементы удовлетворяют требованиям по прочности и раскрытию трещин, но не удовлетворяют требованиям по прогибам, допускается в таких элементах предусматривать строительный подъем (обратный выгиб), но не более 1/300l; при этом величина строительного подъема вычитывается из полученной расчетом величины общего прогиба элемента.
Для плит перекрытий длиной более 4 м должна производиться проверка по зыбкости: дополнительный прогиб от кратковременно действующей сосредоточенной нагрузки 1000 Н (100 кгс) при наиболее невыгодной схеме ее приложения должен быть не более 0,7 мм.
4. Порядок подбора и назначения состава
арболита
4.1. Подбор и назначение состава арболита должны производиться заводской лабораторией любым проверенным на практике способом.
Подобранный состав при принятых технологических режимах производства должен обеспечить получение арболита с заданными проектными показателями при минимальном расходе цемента. Назначенный состав арболита должен утверждаться главным инженером и контролироваться заводской лабораторией.
4.2. Подбор состава арболита включает:
оценку и выбор исходных материалов, испытание контрольных образцов, обработку полученных результатов и назначение рабочего состава;
проверку назначенного состава в производственных условиях и корректировку дозировок материалов на 1 замес.
4.3. Исходные материалы для приготовления арболита должны оцениваться и выбираться на основании требований разд. 1 в соответствии с действующими стандартами и методиками, изложенными в ГОСТ 19222(73 и настоящей Инструкции.
4.4. Расчет и назначение состава арболита следует производит в соответствии с прил. 3. Там же даны ориентировочные расходы материалов на 1 м3 арболитовой смеси.
4.5. Расчетные составы арболита проверяют в лабораторных или производственных условиях путем изготовления и испытания контрольных образцов-кубов по ГОСТ 10180(78. Опытные образцы для определения класса арболита по прочности при сжатии хранятся в течение 28 сут при температуре 20(2 С( и относительной влажности воздуха 70(10 %. Для уточнения распалубочной или отпускной прочности изготавливаются и испытываются образцы в возрасте 1(7 сут.
Рабочий состав арболита должен назначаться на основании обработки результатов испытаний контрольных образцов.
4.6. Рабочий состав арболита должен проверяться в производственных условиях при изготовлении конструкций по действующей на заводе технологии путем изготовления и испытания контрольных образцов-кубов по ГОСТ 10180(78 с учетом п. 4.5.
4.7. После производственной проверки рабочего состава арболита в соответствии с п. 4.6 следует составить таблицы объемно-весового дозирования с указанием расхода всех материалов по массе, а дробленки ( по объему с учетом колебаний насыпной плотности (см. прил. 2).
4.8. Рабочий состав арболита должен корректироваться при организации изготовления конструкций, изменении проектных характеристик арболита, вида и поставщика древесного сырья или цемента и при изменении технологических режимов производства.
4.9. Состав бетона (раствора) отделочного слоя конструкций устанавливается по общим правилам подбора состава бетона (раствора).
5. Приготовление и транспортирование арболитовых смесей
5.1. Древесную дробленку со склада к месту дозирования следует транспортировать ленточными транспортерами, скиповыми устройствами, пневмотранспортом и другими средствами, исключающими ее загрязнение.
5.2. Древесная дробленка в момент подачи на дозирование должна иметь положительную температуру. В зимнее время допускается замачивать ее в подогретой до 70 (С воде.
Длительность замачивания древесной дробленки назначается на основании результатов лабораторных испытаний и должна составлять не менее 15 мин.
5.3. Арболитовая смесь приготовляется и транспортируется с использованием оборудования, применяемого на заводах сборного железобетона.
5.4. Древесная дробленка должна дозироваться объемно-весовым способом с последующей корректировкой состава смеси арболита на основе контроля насыпной плотности дробленки в весовом дозаторе (см. прил. 2).
5.5. Точность дозирования материалов, % , должна быть:
цемента по массе (2;
древесной дробленки:
по объему (5;
или по массе (3;
воды по массе или объему (2;
раствора химдобавок по массе или объему (2.
5.6. Арболитовая смесь должна приготовляться в смесителях принудительного цикличного действия типа СБ-35 (С-773), СБ-62 (С-951) или лопастных растворо-смесителях типа С-209, СМ-290.
5.7. Должна соблюдаться следующая последовательность загрузки смесителей составляющими арболитовой смеси:
при предварительном замачивании дробленки ( древесная дробленка, цемент. Раствор химических добавок подается в течение всего времени загрузки;
при применении дробленки с равновесной влажностью (относительная влажность до 30 %) ( древесная дробленка, растворы химических добавок, цемент, вода. Вода может заменяться водным раствором химической добавки.
Допускается применять двухстадийное перемешивание. Для этого часть цемента (примерно 15(20 % общего его количества на замес), подогретого до температуры 150(250 (С, перемешивают в течение 1(2 мин с органическим заполнителем, а затем в смесь добавляют остальную часть цемента (с нормальной температурой) и воду, подогретую до 80 (С, а также раствор химической добавки, после чего смесь перемешивают обычным порядком в течение 2(3 мин.
5.8. Вода к смесителю должна подаваться по трубопроводу с регулируемой подачей.
5.9. Продолжительность перемешивания арболитовой смеси, считая с момента загрузки всех материалов и смеситель циклического действия и до начала ее выгрузки, определяется опытным путем и должна быть не менее 3 мин.
5.10. Поданная к месту укладки арболитовая смесь должна иметь:
требуемую плотность в уплотненном состоянии с отклонениями не более (5%;
показатель расслоения не более 10%;
показатель отделимости цементного теста в пределах 20(30 с;
температуру в пределах 10(30 (С.
Арболитовая смесь должна иметь жесткость 20(45 с по техническому вискозиметру или подвижность не менее 2 см по осадке конуса.
5.11. Арболитовая смесь от смесителя к месту укладки должна транспортироваться бетонораздатчиками, кюбелями и другими транспортными средствами, исключающими ее расслаивание и потерю составляющих.
5.12. Подача арболитовой смеси ленточными транспортерами допускается при условии, что количество перегрузок должно быть не более двух; угол наклона транспортера ( не более 15( при подъеме смеси и 10( ( при ее спуске, длина транспортера ( не более 30 м, скорость движения ленты транспортера не должна превышать 1 м/с.
5.13. Высота падения арболитовой смеси при перегрузках не должна превышать 1 м до верхней кромки приемного бункера.
6. Формирование конструкций из арболита
6.1. Допускаются следующие способы формирования и уплотнения конструкций из арболитовой смеси:
послойное укатывание,
силовой вибропрокат,
вибропрессование,
прессование,
послойное механическое требование,
уплотнение на виброплощадках.
Методы формирования конструкций из арболита должны выбираться в зависимости от требуемой плотности арболита, вида конструкции, наличия оборудования и обосновываться технико-экономическим расчетом.
6.2. Конструкция из арболитовой смеси формуют в горизонтальных или вертикальных металлических формах, снабженных при необходимости зажимными металлическими крышками, которые снимают после приобретения арболитом распалубочной прочности.
Формы должны удовлетворять требованиям ГОСТ 18886(73.
6.3. Перед формированием поддоны и бортоснастка должны быть тщательно очищены, формы собраны и смазаны. В зимнее время формы должны иметь положительную температуру, но не более 40 (С.
6.4. Арматура и накладные изделия в формах должны устанавливаться в соответствии с требованиями проекта. Для предупреждения смещений и обеспечения требуемой толщины защитного слоя бетона арматуру и накладные изделия следует фиксировать специальными приспособлениями.
6.5. При закладке арболитовой смеси в формы необходимо соблюдать следующие требования:
время от момента выгрузки из смесителя до укладки должно быть не более 30 мин для арболитовой смеси и 20 мин для поризованной арболитовой смеси;
применять специальные бетоноукладчики и другие механизмы с рабочими органами, обеспечивающими равномерное распределение смеси по всей площади формуемой конструкции;
поверхности деревянных дверных и оконных коробок, соприкасающиеся с арболитом, должны быть изолированы гидрофобными антисептирующими смазками, слоем водонепроницаемой бумаги или пленкой в соответствии с проектом;
арболитовую смесь укладывать без перерывов. Допускаются перерывы при укладке отдельных слоев до 20 мин.
6.6. При уплотнении арболитовых смесей необходимо:
обеспечивать расчетное уплотнение смеси по всему объему конструкции;
не допускать расслоения арболитовой смеси в верхнем слое конструкции, а также оседания цементного теста в нижнем слое;
добиваться равномерной укладки арболитовой смеси, соблюдая горизонтальность уложенных слоев;
не допускать вытекания цементного теста из формы;
тщательно уплотнять смесь у бортов формы и закладных деталей.
6.7. Арболитовые смеси в горизонтальных формах на установке послойного формования СМЖ-506 должны уплотняться с учетом следующих требований:
толщина уплотняемого слоя арболитовой смеси должна быть не более 100 мм;
число слоев должно составлять 2(4;
коэффициент уплотнения арболитовой смеси, определяемый расчетно-экспериментальным методом в зависимости от класса арболита по прочности и контролируемый в процессе формирования, должен быть не более: для класса В0,5 ( 1,15; В0,75 ( 1,25; В1 ( 1,3; В1,5 ( 1,6; В2 ( 1,8; В2,5; В3,5 ( 2;
укатывание смеси каждого слоя производить не менее чем за один челночный проход укатывающей тележки.
6.8. При формовании конструкций с немедленной распалубкой технологические параметры должны выбираться с учетом сохранения целостности кромок конструкции, обеспечения минимальных деформация арболита на всех последующих операциях и отклонений от проектных размеров конструкций после затвердения в соответствии с ГОСТ 19222(73, а также стандартов или технических условий на данный вид конструкций.
6.9. Отделку наружных поверхностей конструкций следует производить материалами и способами, указанными в проекте. Допускается применять для отделки наружных поверхностей конструкций из арболита материалы и способы, указанные в Инструкции по изготовлению изделий из ячеистого бетона.
7. Твердение конструкций из арболита
7.1. Отформованные конструкции из арболита должны твердеть в условиях, обеспечивающих достижение арболитом распалубочной или отпускной прочности в наиболее короткие сроки при соблюдении требований по экономии цемента и качеству готовых конструкций.
7.2. Твердение конструкций из арболита должно осуществляться следующими способами:
в естественных условиях при температуре воздуха не ниже 15 (С и относительной влажности воздуха 60-80 %;
тепловой обработкой в камерах при температуре не более 40 (С и относительной влажности воздуха 50-60 %;
электропрогревом при температуре не более 50 (С.
7.3. Для конструкций из арболита режим тепловой обработки должен обеспечивать как требуемую отпускную и проектную прочность, так и отпускную влажность арболита в конструкциях.
Тепловую обработку конструкций, офактуренных с двух сторон раствором, необходимо производить в камерах при температуре не более 60 (С, оборудованных термоэлектронагревателями (ТЭНами), калориферами, инфракрасными излучателями или газовыми горелками с устройством в них дополнительной вентиляции. Тепловая обработка конструкций из арболита в среде насыщенного пара или паровоздушной среде, а также на термоподдонах не допускается.
7.4. При назначении общего цикла твердения следует учитывать вид древесного заполнителя и химических добавок, способ твердения, величину распалубочной и отпускной прочности и длительность выдерживания конструкций после тепловой обработки.
7.5. При твердении конструкций, изготовленных на портландцементе марки 400 и более, в естественных условиях при температуре (20(2) (С и относительной влажности воздуха (70(10) % арболит приобретает прочность при сжатии 50 % от средней прочности Rсж (см. п. 3.9) через 3(5 сут, на БТЦ ( через 1(2 сут.
7.6. При тепловой обработке конструкций из арболита в камерах при температуре 40 (С и относительной влажности воздуха 50(60 % длительность отдельных периодов должна назначаться в соответствии со следующими требованиями:
продолжительность выдерживания отформованных конструкций до начала тепловой обработки должна быть не менее 12 ч;
скорость подъема температуры среды в камере и скорость остывания конструкций после изотермического прогрева должна быть не более 10 (С/ч;
изотермический прогрев должен осуществляться при температуре теплоносителя не более 40 (С, относительной влажности теплоносителя 50(60 % и скорости его движения 2(3 м/ч в течение 12(14 ч.
Общий цикл тепловой обработки при этих условиях не должен превышать 24 ч.
Примечание. При тепловой обработке конструкций из арболита, офактуренных с двух сторон раствором, в формах температура теплоносителя может быть повышена до 50(60 (С.
7.7. Элетротермообработку конструкций из арболита следует осуществлять электропрогревом и электрообогревом.
При электропрогреве следует применять электроды из металлических стержней и струн диаметром не менее 6 мм или из полос шириной не менее 15 мм, выполненных из листовой стали и прикрепленных на внутренних поверхностях форм, а также специальными щитами, устанавливаемыми на открытую поверхность конструкций.
При электрообогреве следует применять нагреватели инфракрасного излучения или низкотемпературные нагреватели (сетчатые, коаксиальные, ТЭНы).
Предварительный разогрев смеси электроэнергией допускается до температуры 40 (С.
7.8. При электротермообработке при температуре 50 (С арболит приобретает прочность при сжатии 50 % средней прочности по п. 3.9 через 20(24 ч прогрева и последующего выдерживания без тепловой обработки при температуре не ниже 15 (С в течение 1(2 сут.
7.9. После приобретения арболитом прочности при сжатии, равной 50 % средней прочности по п. 3.9, но не менее 0,5 МПа, конструкции распалубливаются и выдерживаются в цехе при температуре не ниже 15 (С в течение 5(6 сут, после чего они хранятся на крытом складе готовой продукции.
В зимних условиях конструкции из арболита после распалубки хранят в закрытом помещении с температурой не ниже 15 (С до приобретения средней прочности арболита на сжатие, соответствующей его классу.
8. Распалубка, доводка,
хранение и транспортировка
конструкций из арболита
8.1. Распалубка конструкций из арболита должна производиться при разнице температур окружающей среды и открытой поверхности конструкции не более 30 (С.
8.2. Крупноразмерные конструкции, не рассчитанные на работу при изгибе, после распалубки следует устанавливать в рабочее положение при помощи специальных кантователей.
8.3. Окончательную доводку и комплектацию конструкций, а также отделку лицевой поверхности их после распалубки следует производить на специализированных отделочных постах или конвейерных линиях с применением механизированного инструмента.
8.4. Внешний вид и качество отделки поверхностей конструкций из арболита должны соответствовать утвержденному эталону и отвечать требованиям ГОСТ 19222(73.
8.5. Конструкции из арболита, принятые ОТК, следует хранить и транспортировать в соответствии с требованиями ГОСТ 19222(73, ГОСТ 13015(75. а также ГОСТов и ТУ на конкретные виды конструкций.
9. Особенности производства конструкций из арболита в зимнее время
9.1. Для нормальной организации производства конструкций из арболита в зимнее время следует выполнять следующие мероприятия:
обеспечить запас древесных отходов в объеме, необходимом для работы в зимний период, с предварительной выдержкой их в летнее время;
подогревать органический заполнитель, песок, гравий и воду до положительной температуры;
отформованные конструкции из арболита прогревать в специальных камерах или применять электротермообработку с соблюдением установленных режимов в соответствии с п.п. 7.3(7.8;
применять быстротвердеющие цементы марок 500 и выше (БТЦ и ОБТЦ);
подогревать окружающий воздух в отделениях твердения и выдерживать конструкции из арболита при температуре не менее (20(2) (С.
10. Контроль качества исходных материалов, арболита и готовых конструкций
10.1. Соответствие показателей качества исходных материалов, арболита и готовых конструкций из него, а также параметров технологических режимов производства нормируемым показателям, указанным в стандартах или технических условиях на конструкции конкретных видов, и требованиям технологической документации устанавливают по данным входного, операционного и приемочного контроля в соответствии с требованиями ГОСТ 13015.1(81.
10.2. Номенклатура показателей качества конструкций и параметры технологических режимов, подвергаемые входному, операционному и приемочному контролю, принимаются по ГОСТ 13015.1(81.
10.3. Качество материалов, применяемых для приготовления изделий из арболита, следует определять:
цемента ( по ГОСТ 310.1(76 ( ГОСТ 310.4(81;
древесной дробленки ( по ГОСТ 19222(73 с учетом дополнений, изложенных в настоящей Инструкции (прил. 1);
плотных крупных заполнителей ( по ГОСТ 8269(76;
плотных песков ( по ГОСТ 8735(75;
пористых заполнителей ( по ГОСТ 9758(77;
арматуры и закладных изделий ( по ГОСТ 10922(75;
химических добавок ( по стандартам или техническим условиям на данный вид химической добавки.
10.4. Контроль приготовления арболитовой смеси и проверку ее качества следует производить путем отбора проб из арболита каждого класса не реже двух раз в смену и испытания их по ГОСТ 10181.0(81 ( ГОСТ 10181.4(81 и ГОСТ 10180(78.
10.5. Для контроля прочности при сжатии и плотности арболита, а также контроля назначенного технологического режима ежесменно для каждого класса арболита изготовляют по режиму, принятому на производстве, три серии образцов, по три образца в каждой, размером 150(150(150 мм. Первую серию выдерживают в течение 28 сут в условиях по п. 4.5 настоящей Инструкции. Две серии контрольных образцов должны твердеть по одинаковому с контролируемыми конструкциями режиму до момента определения отпускной прочности (7 сут), после чего вторая серия испытывается на сжатие с обмером и взвешиванием для определения плотности и влажности по ГОСТ 12730.1(78 и ГОСТ 12730.2(78.
Последующее твердение образцов третьей серии, предназначенных для определения прочности арболита в проектном возрасте, должно происходить в условиях по п. 4.5 настоящей Инструкции. Через 28 сут на образцах первой и третьей серии определяют среднюю прочность при сжатии (единичное значение прочности) арболита, учитываемые при статистической обработке по п. 1.7 ГОСТ 18105.0(80, а плотность ( по ГОСТ 12730.1(78.
Сравнение средней прочности арболита на сжатие, определенной на образцах, твердевших в стандартных условиях (п. 4.5), со средней прочностью арболита, определенной на образцах, полученных в условиях твердения и формования по принятой технологии (фактическая прочность), а также с заданной в проекте прочностью и полученные при этом расходы цемента характеризуют качество арболита и технико-экономическую эффективность технологии производства работ.
Для уточнения распалубочной прочности арболита следует изготавливать и испытывать образцы в возрасте 1(3 сут.
10.6. Средняя фактическая прочность (класс) и плотность арболита признается удовлетворяющей проектным требованиям, если прочность его не ниже требуемой, а плотность испытанных образцов не превышает проектное значение более чем на 5 %.
10.7. Отпускную прочность при сжатии бетона (раствора) отделочных слоев проверяют на образцах 7(7(7 см или 10(10(10 см в соответствии с ГОСТ 10180(78. Образцы для проверки класса бетона (раствора) отделочных слоев изготовляют один раз в сутки.
10.8. Влажность арболита в конструкциях проверяют не менее одного раза в месяц по ГОСТ 19222(73.
10.9. Плотность арболита в конструкциях контролируют путем взвешивания конструкций динамометром с обязательной проверкой фактической толщины отдельных слов. Плотность арболита в конструкциях целесообразно проверять на конструкциях, в которых производится контроль отпускной влажности арболита.
10.10. Морозостойкость арболита следует определять по ГОСТ 7025(78, а для тяжелого бетона отделочных слоев по ГОСТ 10060(76.
Морозостойкость арболита следует определять перед началом производства конструкций, а затем через каждые 3 мес или при изменении технологии изготовления.
10.11. До начала производства конструкций, а также в сроки, указанные в стандартах и технических условиях на конкретные виды конструкций, следует проверять следующие показатели арболита:
водопоглощение ( по ГОСТ 12730.3(78;
коэффициент теплопроводности ( по ГОСТ 7076(78.
10.12. Предприятие-изготовитель должно отпускать потребителю конструкции, принятые ОТК. При этом потребителю должен выдаваться паспорт, подписанный ОТК и руководителем предприятия-поставщика, или заверенная копия паспорта той партии, к которой принадлежат поставляемые потребителю конструкции.
Приложение 1
Методы испытаний древесной дробленки, арболитовой смеси и затвердевшего арболита
1. Методика определения показателя пригодности дробленки
Показатель пригодности дробленки определяется путем ее испытания в арболите.
Для приготовления арболитовой смеси применяют портландцемент марок 400(500 по ГОСТ 10178(76, испытываемую дробленку в сухом состоянии и разделенную на фракции 0(5, 5(10 и 10(20 мм, хлористый кальций по ГОСТ 450(77 и воду по ГОСТ 23732(79.
В случае получения отрицательного результата хлористый кальций должен быть заменен комплексной химической добавкой, например, смесь сернокислого железа, гидрата окиси кальция и хлористого кальция в соотношении от 1 : 8 : 1 до 2 : 10 : 2 (по массе) в количестве 10(12 % массы цемента.
Для испытания изготовляют три замеса арболитовой смеси, каждый объемом около 12 л в уплотненном состоянии. Соотношение расхода цемента, дробленки и хлористого кальция указаны в табл. 9.
Таблица 9
|
Расход |
№
замеса |
цемента, кг |
хлористого кальция, |
дробленки в сухом состоянии, при
фракции, мм |
|
|
кг |
0(5 |
5(10 |
10(20 |
1
2
3 |
4,25
4,75
5,25 |
0,085
0,095
0,105 |
8
8
8 |
8
8
8 |
9
9
9 |
Дробленку дозируют по массе с учетом насыпной плотности отдельных фракций.
Расходы воды для затворения арболита принимается из расчета, чтобы В/Ц затворения было равно 1/1.
Арболитовую смесь приготовляют путем перемешивания вручную в течение 10 мин или в бетоносмесителе принудительного действия ( в течение 5 мин и укладывают в форму кубов размером 10(10(10 см.
Формы заполняют арболитовой смесью в два слоя высотой по 5 см и уплотняют трамбованием стальной болванкой (рис. 5).
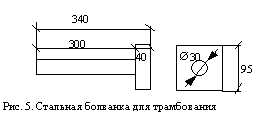
Каждый слой уплотняют 15(20 нажимами с высоты 2(3 см, с тем чтобы коэффициент уплотнения арболитовой смеси находился в пределах 1,9(2. После уплотнения смеси поверхность образцов заглаживают.
Допускается при изготовлении контрольных образцов применять уплотняющие устройства, используемые для изготовления конструкций из арболита.
Из каждого замеса изготовляют шесть кубов и определяют плотность свежеуложенного арболита (см.
Фактический расход цемента Ц на 1 м3 уплотненного арболита для каждого из трех замесов вычисляют по формуле
,
где Ц,ц ( расход цемента, кг, соответственно на 1 м3 и на замес;
(см ( плотность свежеуложенного арболита, кг/м3;
(Р ( расход всех компонентов на замес, включая фактически потраченную воду, кг.
Фактический расход всех остальных компонентов на 1 м3 уплотненного арболита вычисляют по ГОСТ 11051(70.
Изготовленные кубы из арболита извлекают из форм через 3 сут и переносят в камеру для стандартного твердения по ГОСТ 19222(73. Образцы из арболита на сжатие стандартного твердения испытывают в 28-дневном возрасте.
Перед испытанием на сжатие производится обмер и взвешивание образцов с определением плотности арболита (б.
После испытания образцов из кусов арболита берется навеска 500 г, высушивается при температуре 80(5 (С до постоянной массы и определяется влажность, %, по массе W, после чего вычисляется плотность арболита в сухом состоянии ((б(с) по формуле
.
По результатам испытания прочности при сжатии арболита отдельных образцов определяют среднюю прочность его в серии образцов, для чего предварительно отбраковывают аномальные значения по ГОСТ 10180(78.
Среднесерийные результаты испытаний трех серий образцов наносят на график с координатами: расход цемента, кг/м3, прочность при сжатии, МПа, и плотность (б(с, кг/м3.
По построенным кривым, соединяющим три экспериментальные точки, определяют прочность при сжатии, МПа, Rб, соответствующую расходу цемента 360 кг/м3.
По результатам испытаний определяется коэффициент пригодности дробленки, равный отношению показателя активности цемента (Ац), МПа, к показателю прочности арболита.
.
2. Определение содержания водорастворимых редуцирующих веществ в дробленке
Метод определения водорастворимых редуцирующих веществ основан на восстановлении сахарами основной соли двухвалентной меди до ее закиси. Содержание сахара определяют по количеству перманганата калия, пошедшего на титрование двухвалентного железа, образовавшегося в результате реакции трехвалентного железа с закисью меди.
Приборы и реактивы
Сульфат меди, пентогидрат меди, CuSO4(5H2O по ГОСТ 4165(68. Растворяют 40 г соли CuSO4(5H2O в 1 л воды.
Сегнетова соль, C4H4O6KNa(4H2O по ГОСТ 5845(70. Гидроксид натрия по ГОСТ 4328(66. Щелочной раствор сегнетовой соли готовят следующим образом: растворяют 200 г соли в 600 мл воды, добавляют 150 г NaOH и разбавляют дистиллированной водой до 1 л.
Железоаммонийные квасцы Fe(NH4SO4)2(12Н2О по ГОСТ 4205(68.
Серная кислота (плотность 1,84 г/см3) по ГОСТ 4204(66. Раствор железоаммонийных квасцов готовят следующим образом: 100 г железоаммонийных квасцов растворяют в 700 мм дистиллированной воды, добавляют 110 мл H2SO4 и разбавляют водой до 1 л.
Перманганат калия по ГОСТ 4527(65; 0,1 и титрованный раствор.
Асбест волокнистый. Предварительно асбест кипятят в дистиллированной воде в течение 1 ч, отфильтровывают и высушивают при 105 (С.
Сушильный шкаф
Воронка Шотта с фильтром № 2
Водоструйный насос
Колбы Буназена
Песочные часы.
Проведение анализа
Для определения содержания водорастворимых редуцирующих веществ в дробленке приготовляют водную вытяжку.
Поступившую на испытание дробленку измельчают до размеров опилок (0,2(2 мм), хорошо перемешивают, подсушивают до воздушно-сухого состояния и хранят в плотно закрытой склянке. Перед анализом определяют влажность пробы и все расчеты в дальнейшем ведут на сухую навеску (высушенную при 85 (С).
Для приготовления вытяжки берут 2 г пробы (дробленки), взвешивают ее с точностью 0,0002 г, помещают в коническую колбу емкостью 250 мм и приливают 10 мл дистиллированной воды. Колбу закрывают пробкой и ставят в термостат при 25 (С.
Экстрагирование проводят в течение 48 ч, периодически перемешивая содержимое колбы. Затем вытяжку отфильтровывают. В коническую колбу емкостью 150 мм вливают 20 мл раствора сульфата меди и 20 мл щелочного раствора сегнетовой соли, перемешивают и добавляют в нее 20 мл водной вытяжки из дробленки, снова перемешивают и нагревают до кипения. С момента появления первого пузырька раствор кипятят 3 мин (по песочным часам) и фильтруют в колбу Буназена через воронку Шотта с фильтром № 2, на который предварительно помещают небольшое количество асбеста. Осадок на асбесте промывают 100-150 мл горячей воды (необходимо осадок все время держать под водой, так как CuO2 на воздухе окисляется). Затем фильтр с осадком, покрытым водой, быстро переставляют на чистую колбу Буназена. Осадок обрабатывают 20 мл раствора железоаммонийных квасцов. После растворения осадка подключают водоструйный насос и асбест промывают холодной водой до нейтральной реакции промывных вод (проба по лакмусовой бумажке).
Фильтрат титруют 0,1 раствором перманганата калия до появления устойчивой розовой окраски.
Различным объемам перманганата калия, идущего на титрование, соответствуют определенные количества сахара, указанные в табл. 2. Зная объем перманганата калия, израсходованный на титрование 20 мл водной вытяжки, взятой на анализ, по табл. 2 находят содержание сахара (редуцирующих веществ).
Количество редуцирующих веществ в дробленке определяют по формуле
,
где РВ ( количество водорастворимых редуцирующих веществ в дробленке, % от сухой навески;
b ( количество сахара, мг, соответствующее объему перманганата калия, пошедшего на титрование пробы, найденное по табл. 10, ч;
Vo ( объем воды, использованной для приготовления водной вытяжки, мл;
V1 ( объем водной вытяжки, взятой на анализ, мл;
g ( навеска сухой дробленки, г.
Таблица 10
| | | | | | | | | | |
Содержание сахара, мг, при объеме титра перманганата калия |
цельные |
десятые доли единицы |
единицы |
0 |
1 |
2 |
3 |
4 |
5 |
6 |
7 |
8 |
9 |
0
1
2
3
4
5
6
7
8
9
10
11
12
13
14
15
16
17
18
19
20 |
(
2,93
6,10
9,30
12,60
15,80
19,00
22,30
25,70
29,10
32,40
35,90
39,40
43,00
46,40
50,00
53,60
57,20
60,90
64,58
68,35 |
0,30
3,25
6,40
9,60
1290
16,10
19,30
22,70
26,00
29,40
32,80
36,20
39,70
43,20
46,80
50,40
54,00
57,60
61,30
64,94
68,80 |
0,60
3,55
6,76
9,95
1320
16,40
19,70
23,00
26,30
29,70
33,10
36,60
40,00
43,60
47,20
50,60
54,40
58,00
61,90
65,30
69,29 |
0,85
3,89
7,05
10,30
13,50
16,80
20,00
23,30
26,70
30,00
33,50
36,90
40,50
43,90
47,50
51,20
54,70
58,40
62,20
60,00
69,56 |
1,15
4,20
7,40
10,60
13,85
17,10
20,30
23,70
27,00
30,40
33,80
37,30
40,70
44,30
47,80
51,40
54,90
58,70
62,50
66,08
69,75 |
1,45
4,50
7,70
11,00
14,15
17,40
20,60
24,00
27,30
30,70
34,10
37,60
41,10
44,70
48,30
51,80
55,40
59,00
62,83
66,60
70,25 |
1,75
4,86
8,00
11,20
14,50
17,70
20,90
24,30
27,70
31,10
34,50
38,00
41,40
45,00
48,60
52,20
55,80
59,40
63,10
66,90
70,62 |
2,05
5,15
8,35
11,60
14,85
18,00
21,20
24,70
28,00
31,40
34,80
38,30
41,80
45,40
48,80
52,60
56,20
59,80
63,68
67,20
71,01 |
2,03
5,45
8,65
11,95
15,15
18,40
21,60
25,00
28,40
31,70
35,20
38,60
42,20
45,70
49,30
52,90
56,60
60,10
63,82
67,54
71,37 |
2,60
5,75
8,95
12,30
15,45
18,75
22,00
25,30
28,70
32,10
35,70
39,00
42,50
46,10
49,60
53,20
56,90
60,50
64,20
67,90
71,80 |
3. Методика определения образования высолов на поверхности арболита
1. Из арболита с максимальным, средним и минимальным количеством химической добавки, выбранной для изготовления конструкций, изготовляются по три образца-близнеца размерами 10(10(30 или 15(15(45 см. После выдерживания при температуре 20 (2 (C в относительной влажности воздуха 70(10% в течение 28 сут образцы погружаются торцом в ванну с водой на 3(5 см, причем образцы каждой серии помещаются в различные ванны. Наружная поверхность образцов обдувается воздухом с температурой 20(30 (С.
2. В процессе испытания производится периодический осмотр поверхности призм. Наличие высолов отмечается визуально по появлению выцветов или налету соли. Отсутствие последних в течение 7 сут свидетельствует о возможности применения данного количества добавки в арболите. Появление высолов на поверхности образцов свидетельствуют об избытке химической добавки.
Приложение 2
Дозирование материалов для приготовления арболита
Древесную дробленку для арболитовой смеси необходимо дозировать в объемно-весовом дозаторе. Рекомендуемые схемы приведены на рис. 6.
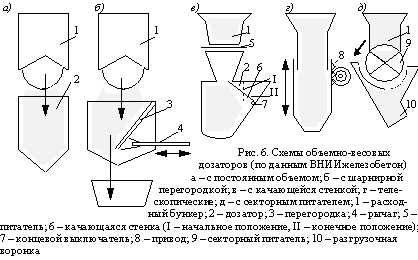
Для установления объема дозатора необходимо производить его предварительную тарировку. С этой целью во время загрузки его по циферблату фиксируют массу отдозированного по объему материала и отбирают усредненную пробу объемом не менее 20 л, составленную из отдельных проб, отобранных во время заполнения дозатора. Проверяют насыпную плотность отобранной пробы. Произведя деление величины зафиксированной массы заполнителя в дозаторе на величину насыпной плотности отобранной пробы, определяют объем дозатора. Среднее значение объема дозатора вычисляют по 20-25 навескам.
По найденному объему дозатора (Vдоз) и принятому расходу древесной дробленки на 1 м3 арболита (Vк) устанавливают объем приготовленного замеса по формуле и далее рассчитывают расход отдельных материалов на замес.
Воду и растворы химических добавок дозируют автоматическими объемными или весовыми дозаторами. При этом допускается химические добавки дозировать весовым дозатором воды.
При назначении дозировки воды и заполнителей следует учитывать влажность дробленки и вносить соответствующие поправки на расход воды и заполнителя на основе таблиц объемно-весового дозирования.
В табл. 11 приведен расход материалов на один замес арболитовой смеси.
Таблица 11
Масса древесной |
Влажность дробления, |
Расход на замес, кг |
дробленки в дозаторе, кг |
% по массе |
цемента |
СаСl2 |
воды |
120
126
132
138
144
150
156
162
168
174
180 |
0
5
10
15
20
25
30
35
40
45
50 |
180
180
180
180
180
180
180
180
180
180
180 |
33,3
33,3
33,3
33,3
33,3
33,3
33,3
33,3
33,3
33,3
33,3 |
150
144
138
132
126
120
114
108
102
96
90 |
Примечания: 1. Раствор хлорида кальция 10% концентрации с плотностью 1,084.
2. Плотность арболитовой смеси в уплотненном состоянии 970(20 кг/м3.
Приложение 3
Пример подбора состава арболита
Требуется подобрать состав конструкционного арболита класса В2,5 плотностью не более 650 кг/м3 (в высушенном состоянии) для панелей наружных стен.
Имеется дробленка из отходов деревообработки хвойных пород зернового состава, удовлетворяющего требованиям ГОСТ 19222(73. Насыпная плотность дробленки в сухом состоянии ( 120 кг/м3, влажность по массе равна 50%. Вяжущее ( портландцемент марки 400.
Подбор состава арболита производится расчетно-экспериментальным методом. По табл. 12(15 определяется ориентировочный расход составляющих для изготовления первого исходного замеса:
по табл. 12 расход цемента составляет 330 кг/м3,
Таблица 12
Вид
заполнителя |
Ориентировочный расход портландцемента марки М 400 на 1 м3 арболита, кг, в зависимости от его класса |
|
В0,5 |
В0,75 |
В1,0 |
В1,5 |
В2,0 |
В2,5 |
Дробленка из отходов:
лесопиления и деревообработки хвойных пород
лесозаготовок хвойных пород
лесопиления и деревообработки смешанных пород
лесозаготовок смешанных пород
Одубина |
240
260
270
290
280 |
250
280
290
310
300 |
280
300
310
330
320 |
300
320
330
350
340 |
330
350
360
380
370 |
360
380
390
(
400 |
Примечание. Приведенные расходы вяжущих рекомендуются лишь для приготовления первого исходного замеса при подборе состава арболитовой смеси и не могут служить нормами расхода вяжущих в производственных условиях.
а сухого органического заполнителя по табл. 13 ( 220 кг/м3.
С учетом влажности расход древесной дробленки составит 330 кг/м3.
Таблица 13
Вид
заполнителя |
Ориентировочный расход сухого органического заполнителя на 1 м3 арболита, кг, при портландцементе марки М 400 и классе заполнителя |
|
В0,5 |
В0,75 |
В1,0 |
В1,5 |
В2,0 |
В2,5 |
Дробленка из отходов:
лесопиления и деревообработки хвойных пород
лесозаготовок хвойных пород
лесопиления и деревообработки смешанных пород
лесозаготовок смешанных пород
Одубина |
140
150
180
140
160 |
160
170
180
160
180 |
180
190
200
180
200 |
200
210
220
200
220 |
220
230
240
220
275 |
240
250
250
240
290 |
По табл. 14 предварительный расход воды (исходный) для назначенного расхода цемента принимается 360 л/м3, хлористого кальция ( 8 кг/м3.
Таблица 14
Вид
заполнителя |
Ориентировочный расход воды на 1 м3 арболита смеси при сухих органических заполнителях, при классе арболита |
|
В0,5 |
В0,75 |
В1,0 |
В1,5 |
В2,0 |
В2,5 |
Дробленка из отходов:
лесопиления и деревообработки хвойных пород
лесозаготовок хвойных пород
лесопиления и деревообработки смешанных пород
лесозаготовок смешанных пород
Одубина |
260
280
310
310
210 |
280
300
330
330
230 |
300
330
360
360
250 |
330
360
390
390
270 |
380
400
430
430
300 |
400
440
460
460
370 |
Хлорид кальция используется 10%-ной концентрации. Содержание соли в 1 л такого раствора плотностью 1,084 составляет 0,108 кг. Следовательно, для введения в арболит необходимого количества соли в виде 10%-ного раствора на 1 м3 смеси его потребуется: 8 : 0,108 = 74,07 л.
В найденном количестве раствора соли воды содержится 1,064 ( 74,07 ( 8 = 72,3.
В древесной дробленке, требуемой на 1 м3 с учетом влажности древесины (50 %), содержание воды составляет 220( = 110 кг (л).
Таблица 15
Вид химических добавок |
Максимальный расход химической добавки на 1 м3 арболита, кг, в зависимости от вида заполнителей |
|
древесная дробленка |
одубина |
Кальций хлористый технический
Стекло натриевое жидкое
Комплексная добавка:
сернокислый глинозем
известь-пушонка |
8
8
20
25 |
8-9
(
(
( |
С учетом воды, содержащейся в древесной дробленке и в растворе добавки, количество воды для приготовления 1 м3 арболитовой смеси составит 360 ( 72,3 ( 110 = 177,7 л.
Плотность арболита в сухом состоянии при данном расходе материалов определяется по формуле
= 1,15Ц + Дсух + Хд = 1,15 ( 330 + 220 + 8 = 608 кг/м3,
где Ц, Дсух, Хд ( соответственно расход цемента, древесной дробленки и химической добавки, кг/м3;
1,15Ц ( масса цементного камня с учетом химически связанной воды, кг/м3.
Плотность уложенной арболитовой смеси при данном расходе материалов составит: (а.см = 330 + 220 + 360 + 8 = 918 кг/м3.
Для установления требуемого расхода цемента необходимо изготовить и испытать три серии образцов с разным расходом цемента: одну ( с намеченным исходным расходом 330 кг/м3 и две дополнительные серии с расходом цемента на 15% меньше и больше принятого, т. е. 280 и 380 кг/м3.
Оптимальный расход щепы для каждого из расходов цемента определяется из условия получения при принятых условиях уплотнения арболита с наибольшим коэффициентом конструктивного качества ККК = при этом не должно наблюдаться расслоения смеси и водоотделения.
Для каждого расхода цемента принимается три расхода воды: установленный по табл. 14 (360 л/м3) и на 5% больше или меньше. ККК арболита определяем на 3(7 сут по результатам испытания трех контрольных кубов размером 15(15(15 см в соответствии с ГОСТ 10180(78. Затем для каждого из трех расходов цемента с оптимальным расходом воды готовят контрольные образцы из арболита для определения марочной прочности. Все образцы изготовляются с соблюдением параметров уплотнения и твердения, близких к производственным.
Опытные образцы для определения марки арболита хранятся в течение 28 сут при (20 (2) (С и относительной влажности воздуха (70(10)%. Для уточнения распалубочной или отпускной прочности при необходимости изготовляются и испытываются образцы в возрасте 1(7 сут.
Средний предел прочности при сжатии образцов для каждого из трех расходов цемента с оптимальным для каждого из них расходом воды наносится на график с координатами: расходы цемента на 1 м3 арболита и предел прочности образцов при сжатии, МПа. Прямая, проходящая через полученные точки, выражает приближенную зависимость прочности арболита от расхода цемента. По графику определяют требуемый расход цемента для получения арболита заданного класса при принятых условиях уплотнения и твердения (в данном случае для класса В2,5).
Контроль плотности арболитовой смеси и арболита осуществляется на свежеотформованных образцах и перед их испытанием на сжатие. Для установления плотности высушенного арболита разрушенные образцы после их испытания на сжатие дробят, берут среднюю пробу и высушивают ее при 80(5 (С до постоянной массы. Плотность высушенного арболита определяется по ГОСТ 12730.1(78.
Расход химической добавки должен оцениваться испытанием на образование высолов по методике, приведенной в прил. 1.
После проверки подобранного состава арболита в производственных условиях он выдается предприятию с указанием расходов материалов на 1 м3 и один замес бетоносмесителя.
Лаборатория после установления фактической влажности дробленки в начале каждой смены, в соответствии с заданным расходом составляющих на 1 м3 арболита, корректирует дозирование воды и заполнителя.
Содержание
1. Общие положения
2. Требования к исходным материалам, арболиту и конструкциям из него
3. Проектирование конструкций из арболита
4. Порядок подбора и назначения состава арболита
5. Приготовление и транспортирование арболитовых смесей
6. Формование конструкций из арболита
7. Твердение конструкций из арболита
8. Распалубка, доводка, хранение и транспортировка конструкций из арболита
9. Особенности производства конструкций из арболита в зимнее время
10. Контроль качества исходных материалов, арболита и готовых конструкций
Приложение 1. Методы испытаний древесной дробленки, арболитовой смеси и затвердевшего арболита
Приложение 2. Дозирование материалов для приготовления арболита
Приложение 3. Пример подбора состава арболита
|